智能手机外壳材料变化及发展趋势
By www.carbonfiber.com.cn
过去智能手机材料清一色的只有工程塑料(聚碳酸酯)或是金属机壳,但随著智能手机尺寸越来越大、消费者逐渐追求轻薄的大趋势之下,各种新材料也开始出现在智能手机上。

手机外壳材料选择历史
除了触控屏幕之外,智能手机的外壳可能是使用者最常接触的部分。外壳可说是整部手机的支撑骨架,更攸关手机内各种电子零件的定位及固定、同时在各种外来物体的撞击或渗漏时给予保护。过去手机的外壳材料仅局限于工程塑料与金属合金,然而随着消费者对智能手机的要求越来越高、各种先进材料也逐渐纳入手机品牌厂商的考虑。
过去的手机外壳通常都是由上壳与下壳组成(部分结构复杂的机种还有中壳),理论上来说,上下壳的外形可以重合。早期的手机外壳壳体通常由工程塑料注塑成型,原料主要为聚碳酸酯(Polycarbonate、简称 PC)以及丙烯腈-丁二烯-苯乙烯塑料(Acrylonitrile-Butadiene-Styrene、简称 ABS)。其中聚碳酸酯具有透明性极佳、常温耐冲击强度高、耐高温与高刚性的特性,早已普及于消费者日常生活中,如光碟,眼镜片,水瓶,防弹玻璃,护目镜、银行防子弹玻璃、车头灯等等、宠物笼子等。聚碳酸酯还被用于制作登月太空人的头盔面罩。
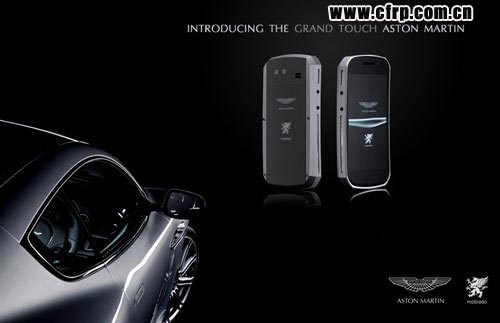
早从智能手机诞生初期,工程塑料就成为了外壳选择的主要材质。而诞生时间更早的 ABS 树脂的最大应用领域为汽车、电子电器和建筑材料,汽车领域的使用包括汽车仪表板、车身外板、内装饰板、方向盘、隔音板、门把、保险桿、通风管等,在消费性电子市场则广泛应用於电冰箱、电视机、洗衣机、空调器、电脑、影印机等产品。ABS 树脂的好处是塑形容易同时价格低廉,适用於对强度要求不太高的零件(不直接受到冲击,不承受可靠性测试中结构耐久性测试的零件,如手机内部的支撑结构(Keypad frame,LCD frame)以及需要电镀的零件(如按钮、侧键、导航键、电镀装饰件等)。过去多数厂商选择搭配使用两种工程塑料材料,但随著以 SAMSUNG 为首的韩国厂商率先全面换用以聚碳酸酯为手机外壳材料,目前看来中高阶手机产品都开始降低 ABS 树脂的使用比例。
镁铝合金(金属材料)外壳的优缺点
在工程塑料之外,手机品牌厂商第一个考虑其他材料就是金属合金材料,过去曾由 NOKIA 及 Apple iPhone 第一代产品掀起了一股金属机壳的风潮。所谓“铝合金材料”,主要原料是铝金属再掺入少量的镁或是其它的金属材料来加强其硬度,依据添加金属的不同而称为镁铝合金或鈦铝合金。铝合金材料既有金属的强度,而且重量轻、也易于散热、同时抗压性较强,在机械强度、耐磨性有了极大的提升。

镁铝合金材质应用于智能手机产品的最大优势在于导热性能和机械强度,其硬度是传统塑料机壳的几倍,因此过去被用于中高阶超薄型或尺寸较小的智能手机产品上。镁铝合金外壳还可通过表面处理工艺上色为粉蓝色和粉红色,可使产品更美观同时增加价值感,其易上色的特性是工程塑料以及碳纤维材料所无法企及的。铝镁合金的散热性远优于塑料材料,能将智能手机内应用处理晶片在高负荷运作时产生的大量热量及时传导至外界。作为金属材质的另一特色是对于外界的的电磁干扰有着良好的屏蔽作用,不过此特色是有利有弊:在对外界电磁干扰屏蔽的同时,手机内收发无线讯号的各式天线性能也大大降低,这也就是金属机壳机种都要在上下方搭配使用塑料材料(于该处安置天线)的原因。
许多消费者(尤其是男性消费者)十分喜爱以铝合金材料作为智能手机外壳,主要是认同金属材料的稳重以及价值感。然而手机品牌厂商选用铝合金材料的缺点也十分明显:它的成本较高。从手机生产角度来看,铝金属外壳成型要比 ABS 困难得多(需要用冲压或者压铸工艺)。但由于金属机壳比工程塑料机壳的强度更高、散热性能更好,又比鈦合金、碳纤维等其他材料更便宜,对於搭载 4.5 吋以下触控屏幕的智能手机产品来说,以铝镁合金材料做为外壳材料仍是很好的选择(不过更大尺寸机种则可能会导致手机重量过重)。
碳纤维材料未来或有望扩大占有率
2007 年通信行业进入了触控屏幕时代,从此之后智能手机产品不断挑战屏幕尺寸的极限、从 3.5 吋、3.7 吋、4.3 吋到 4.7 吋甚至5寸或者更大,许多消费者也以手机尺寸作为产品定位的衡量关键(尺寸越大、产品越高端)。在上述大趋势之下,大尺寸智能手机若采用全金属外壳、其重量将让使用者感到不便。其他先进复合材料因此纳入了手机品牌厂商的考虑范围内,而纳米碳纤维就是其中之一。
多数人对纳米(nm)长度单位并不陌生,一纳米指的是十亿分之一公尺。在达到纳米级别的状况下,由于物质中电子和原子的相互作用将受到尺寸大小的影响非常大,因此材料将呈现与过去不同的特性,其基本性质如熔点、磁性、甚至顏色都能够改变、而且还不需要改变物质的化学成份。例如用超微粒子烧製成的陶瓷硬度可以提高,透过纳米技术制造出来的碳纤维材料其强度比以前的碳纤维提高十倍以上,还将大大减小磨损率并增长使用寿命。

碳纤维具有一般碳素材料的特性,如耐高温、耐磨擦、导电、导热及耐腐蚀等,但与一般碳素材料不同的是,碳纤维其外形有显著的各向异性、柔软、可加工成各种织物,沿纤维轴方向表现出很高的强度。与树脂、金属、陶瓷等基体复合而成的复合材料其强度在现有结构材料无人能出其右。也就是因为其材料特性,碳纤维从上个世纪 1950 年代初开始应用在航空太空领域。随著科技的发展,碳纤维复合材料的生产技术上不断进步、成本也越来越低。除了航空太空应用之外,也广泛应用于体育器械、纺织、化工机械及医学领域。
从手机品牌厂商的角度来看,碳纤维材质是很有潜力的外壳材料:它既拥有铝镁合金高雅坚固的特性,又同时拥有 ABS 工程塑料的高可塑性,其外观类似塑料但是强度和导热能力又优于普通的 ABS 塑料。由于碳纤维是一种导电材质,因此可起到类似金属材料的遮罩作用(ABS 塑料外壳则需要另外镀上一层金属膜作为遮罩),采用碳纤维材料还有一个好处:如果它的表面被油性较重圆珠笔、油性水笔等留下的痕跡可被轻松抹掉。
从种种物理特性来看,碳纤维材料完全有望取代传统塑料外壳的材料,不过其最大缺点是目前碳纤维材料的生产成本仍十分昂贵,另外碳纤维外壳的成型技术目前不如 ABS 外壳那样成熟、加上表面处理与上色技术难度也较高,因此碳纤维机壳的形状一般都比较简单缺乏变化、外观上也欠缺时尚。碳纤维机壳还有一个使用上的小缺点,就是如果接地不好会有轻微的漏电感。
其他先进复合材料也开始获得采用
除了前面提及的 ABS、PC、铝镁合金还有尚未普及的碳纤维材料,智能手机品牌厂商在机壳材料上一直不断挖掘创新,其中很多先进的复合材料也被引入智能手机产品内,包括凯夫拉(Kevlar)、液态金属与陶瓷材料等。

凯夫拉(Kevlar)是化工大厂杜邦(DuPont)在芳族聚醯胺类有机纤维材料的注册商标名称。该种纤维是继玻璃纤维、碳纤维、硼纤维之后的先进复合材料、由杜邦公司首先实现工业化生产。凯夫拉纤维最大的特性是具有极高的强度(约为22cN/dtex,其强度是相同重量钢丝的五倍以上、是高强度工业尼龙和玻璃纤维的两倍以上)。同时凯夫拉纤维的热性能极佳而且热稳定性好,还有良好的绝缘性和抗腐蚀性,因此赢得「合成钢丝」的美誉。凯夫拉纤维最早被用来製作军用防弹衣与防弹头盔,目前已经广泛应用於车辆轮胎强化材料、网球拍、汽车安全气囊、安全带、防弹衣、防火衣,运动衣物,手套,鞋子及户外背包等领域。
虽然凯夫拉纤维的重量轻、而且强度高於玻璃纤维、碳纤维和硼纤维,但目前在消费性电子产品领域的应用还比较少,主因在於其压缩强度、剪切强度都较低、同时吸水性较高,因此在机壳设计上的局限性很大,另外昂贵的成本也是一大阻力。
工程塑料引进新技术提升性能
在材料科技的进步之下,其实工程塑料(聚碳酸酯)的加工与表面处理已经到了新的境界。随着 3D 辅助建模和注塑科技的革命,越来越多手机设计师相信工程塑料并不一定比金属的质感要差。塑料材质可以实现更经济却更复杂的加工程序,还有更精确的钻孔与更快速的生产速度。
由于对手持式电子产品轻量化的需求越来越高,人类对工程塑料材料的改进从未停止。目前 Intel 工程师正在将过去 NASA 太空梭的设计经验运用到工程塑料机构设计,进而降低 Ultrabook 超薄笔记型电脑的价格。超薄笔记型电脑结合了笔记型电脑和平板电脑的优势,但由於价格过高而无法扩大其销售量。为此 Intel 华盛顿研发中心的工程师研发出一套新技术,可以使得塑料外壳的笔记电脑像更昂贵的金属外壳一样坚固。Intel 研发主管 Ben Broili 表示此种技术将使得超薄笔记型电脑的成本降低 25 美元至 75 美元。而前述技术可能大量使用高玻纤机壳,所谓高玻纤机壳就是塑料机壳的玻璃纤维含量达到 50%,这样的机壳强度和厚薄度都可以做到和金属机壳不相上下,但成本却预估只有金属机壳的三分之一,甚至是四分之一。随著新技术的导入,工程塑料机壳有望在智能手机产品上重新取得主流地位。
过去智能手机材料清一色的只有工程塑料(聚碳酸酯)或是金属机壳,但随著智能手机尺寸越来越大、消费者逐渐追求轻薄的大趋势之下,各种新材料也开始出现在智能手机上。

手机外壳材料选择历史
除了触控屏幕之外,智能手机的外壳可能是使用者最常接触的部分。外壳可说是整部手机的支撑骨架,更攸关手机内各种电子零件的定位及固定、同时在各种外来物体的撞击或渗漏时给予保护。过去手机的外壳材料仅局限于工程塑料与金属合金,然而随着消费者对智能手机的要求越来越高、各种先进材料也逐渐纳入手机品牌厂商的考虑。
过去的手机外壳通常都是由上壳与下壳组成(部分结构复杂的机种还有中壳),理论上来说,上下壳的外形可以重合。早期的手机外壳壳体通常由工程塑料注塑成型,原料主要为聚碳酸酯(Polycarbonate、简称 PC)以及丙烯腈-丁二烯-苯乙烯塑料(Acrylonitrile-Butadiene-Styrene、简称 ABS)。其中聚碳酸酯具有透明性极佳、常温耐冲击强度高、耐高温与高刚性的特性,早已普及于消费者日常生活中,如光碟,眼镜片,水瓶,防弹玻璃,护目镜、银行防子弹玻璃、车头灯等等、宠物笼子等。聚碳酸酯还被用于制作登月太空人的头盔面罩。
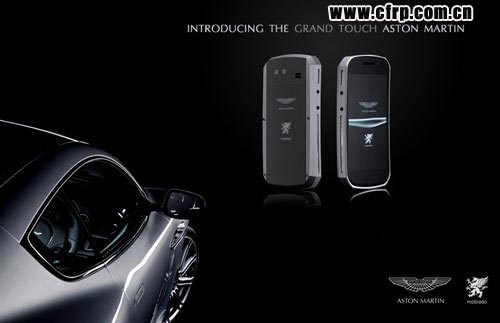
早从智能手机诞生初期,工程塑料就成为了外壳选择的主要材质。而诞生时间更早的 ABS 树脂的最大应用领域为汽车、电子电器和建筑材料,汽车领域的使用包括汽车仪表板、车身外板、内装饰板、方向盘、隔音板、门把、保险桿、通风管等,在消费性电子市场则广泛应用於电冰箱、电视机、洗衣机、空调器、电脑、影印机等产品。ABS 树脂的好处是塑形容易同时价格低廉,适用於对强度要求不太高的零件(不直接受到冲击,不承受可靠性测试中结构耐久性测试的零件,如手机内部的支撑结构(Keypad frame,LCD frame)以及需要电镀的零件(如按钮、侧键、导航键、电镀装饰件等)。过去多数厂商选择搭配使用两种工程塑料材料,但随著以 SAMSUNG 为首的韩国厂商率先全面换用以聚碳酸酯为手机外壳材料,目前看来中高阶手机产品都开始降低 ABS 树脂的使用比例。
镁铝合金(金属材料)外壳的优缺点
在工程塑料之外,手机品牌厂商第一个考虑其他材料就是金属合金材料,过去曾由 NOKIA 及 Apple iPhone 第一代产品掀起了一股金属机壳的风潮。所谓“铝合金材料”,主要原料是铝金属再掺入少量的镁或是其它的金属材料来加强其硬度,依据添加金属的不同而称为镁铝合金或鈦铝合金。铝合金材料既有金属的强度,而且重量轻、也易于散热、同时抗压性较强,在机械强度、耐磨性有了极大的提升。

镁铝合金材质应用于智能手机产品的最大优势在于导热性能和机械强度,其硬度是传统塑料机壳的几倍,因此过去被用于中高阶超薄型或尺寸较小的智能手机产品上。镁铝合金外壳还可通过表面处理工艺上色为粉蓝色和粉红色,可使产品更美观同时增加价值感,其易上色的特性是工程塑料以及碳纤维材料所无法企及的。铝镁合金的散热性远优于塑料材料,能将智能手机内应用处理晶片在高负荷运作时产生的大量热量及时传导至外界。作为金属材质的另一特色是对于外界的的电磁干扰有着良好的屏蔽作用,不过此特色是有利有弊:在对外界电磁干扰屏蔽的同时,手机内收发无线讯号的各式天线性能也大大降低,这也就是金属机壳机种都要在上下方搭配使用塑料材料(于该处安置天线)的原因。
许多消费者(尤其是男性消费者)十分喜爱以铝合金材料作为智能手机外壳,主要是认同金属材料的稳重以及价值感。然而手机品牌厂商选用铝合金材料的缺点也十分明显:它的成本较高。从手机生产角度来看,铝金属外壳成型要比 ABS 困难得多(需要用冲压或者压铸工艺)。但由于金属机壳比工程塑料机壳的强度更高、散热性能更好,又比鈦合金、碳纤维等其他材料更便宜,对於搭载 4.5 吋以下触控屏幕的智能手机产品来说,以铝镁合金材料做为外壳材料仍是很好的选择(不过更大尺寸机种则可能会导致手机重量过重)。
碳纤维材料未来或有望扩大占有率
2007 年通信行业进入了触控屏幕时代,从此之后智能手机产品不断挑战屏幕尺寸的极限、从 3.5 吋、3.7 吋、4.3 吋到 4.7 吋甚至5寸或者更大,许多消费者也以手机尺寸作为产品定位的衡量关键(尺寸越大、产品越高端)。在上述大趋势之下,大尺寸智能手机若采用全金属外壳、其重量将让使用者感到不便。其他先进复合材料因此纳入了手机品牌厂商的考虑范围内,而纳米碳纤维就是其中之一。
多数人对纳米(nm)长度单位并不陌生,一纳米指的是十亿分之一公尺。在达到纳米级别的状况下,由于物质中电子和原子的相互作用将受到尺寸大小的影响非常大,因此材料将呈现与过去不同的特性,其基本性质如熔点、磁性、甚至顏色都能够改变、而且还不需要改变物质的化学成份。例如用超微粒子烧製成的陶瓷硬度可以提高,透过纳米技术制造出来的碳纤维材料其强度比以前的碳纤维提高十倍以上,还将大大减小磨损率并增长使用寿命。

碳纤维具有一般碳素材料的特性,如耐高温、耐磨擦、导电、导热及耐腐蚀等,但与一般碳素材料不同的是,碳纤维其外形有显著的各向异性、柔软、可加工成各种织物,沿纤维轴方向表现出很高的强度。与树脂、金属、陶瓷等基体复合而成的复合材料其强度在现有结构材料无人能出其右。也就是因为其材料特性,碳纤维从上个世纪 1950 年代初开始应用在航空太空领域。随著科技的发展,碳纤维复合材料的生产技术上不断进步、成本也越来越低。除了航空太空应用之外,也广泛应用于体育器械、纺织、化工机械及医学领域。
从手机品牌厂商的角度来看,碳纤维材质是很有潜力的外壳材料:它既拥有铝镁合金高雅坚固的特性,又同时拥有 ABS 工程塑料的高可塑性,其外观类似塑料但是强度和导热能力又优于普通的 ABS 塑料。由于碳纤维是一种导电材质,因此可起到类似金属材料的遮罩作用(ABS 塑料外壳则需要另外镀上一层金属膜作为遮罩),采用碳纤维材料还有一个好处:如果它的表面被油性较重圆珠笔、油性水笔等留下的痕跡可被轻松抹掉。
从种种物理特性来看,碳纤维材料完全有望取代传统塑料外壳的材料,不过其最大缺点是目前碳纤维材料的生产成本仍十分昂贵,另外碳纤维外壳的成型技术目前不如 ABS 外壳那样成熟、加上表面处理与上色技术难度也较高,因此碳纤维机壳的形状一般都比较简单缺乏变化、外观上也欠缺时尚。碳纤维机壳还有一个使用上的小缺点,就是如果接地不好会有轻微的漏电感。
其他先进复合材料也开始获得采用
除了前面提及的 ABS、PC、铝镁合金还有尚未普及的碳纤维材料,智能手机品牌厂商在机壳材料上一直不断挖掘创新,其中很多先进的复合材料也被引入智能手机产品内,包括凯夫拉(Kevlar)、液态金属与陶瓷材料等。

凯夫拉(Kevlar)是化工大厂杜邦(DuPont)在芳族聚醯胺类有机纤维材料的注册商标名称。该种纤维是继玻璃纤维、碳纤维、硼纤维之后的先进复合材料、由杜邦公司首先实现工业化生产。凯夫拉纤维最大的特性是具有极高的强度(约为22cN/dtex,其强度是相同重量钢丝的五倍以上、是高强度工业尼龙和玻璃纤维的两倍以上)。同时凯夫拉纤维的热性能极佳而且热稳定性好,还有良好的绝缘性和抗腐蚀性,因此赢得「合成钢丝」的美誉。凯夫拉纤维最早被用来製作军用防弹衣与防弹头盔,目前已经广泛应用於车辆轮胎强化材料、网球拍、汽车安全气囊、安全带、防弹衣、防火衣,运动衣物,手套,鞋子及户外背包等领域。
虽然凯夫拉纤维的重量轻、而且强度高於玻璃纤维、碳纤维和硼纤维,但目前在消费性电子产品领域的应用还比较少,主因在於其压缩强度、剪切强度都较低、同时吸水性较高,因此在机壳设计上的局限性很大,另外昂贵的成本也是一大阻力。
工程塑料引进新技术提升性能
在材料科技的进步之下,其实工程塑料(聚碳酸酯)的加工与表面处理已经到了新的境界。随着 3D 辅助建模和注塑科技的革命,越来越多手机设计师相信工程塑料并不一定比金属的质感要差。塑料材质可以实现更经济却更复杂的加工程序,还有更精确的钻孔与更快速的生产速度。
由于对手持式电子产品轻量化的需求越来越高,人类对工程塑料材料的改进从未停止。目前 Intel 工程师正在将过去 NASA 太空梭的设计经验运用到工程塑料机构设计,进而降低 Ultrabook 超薄笔记型电脑的价格。超薄笔记型电脑结合了笔记型电脑和平板电脑的优势,但由於价格过高而无法扩大其销售量。为此 Intel 华盛顿研发中心的工程师研发出一套新技术,可以使得塑料外壳的笔记电脑像更昂贵的金属外壳一样坚固。Intel 研发主管 Ben Broili 表示此种技术将使得超薄笔记型电脑的成本降低 25 美元至 75 美元。而前述技术可能大量使用高玻纤机壳,所谓高玻纤机壳就是塑料机壳的玻璃纤维含量达到 50%,这样的机壳强度和厚薄度都可以做到和金属机壳不相上下,但成本却预估只有金属机壳的三分之一,甚至是四分之一。随著新技术的导入,工程塑料机壳有望在智能手机产品上重新取得主流地位。