用于结构件的环氧碳纤维复合材料及加工技术
By www.carbonfiber.com.cn

图1 安装在底盘上的碳纤维复合材料主承载结构
在汽车工业发达国家,一些小批量生产的高档汽车及赛车已使用了采用碳纤维增强环氧树脂复合材料制成的主承力结构件,其强度、刚性及其他各项性能指标均可与传统的金属材料部件相媲美,同时重量也大为减轻。本文主要从材料和加工工艺等方面对此进行阐述。
自20世纪70年代第一次石油危机爆发以来,“汽车轻量化”便成为全球汽车制造业关注的重点之一。几十年来,人们不断地通过优化结构设计以及采用金属替代方案来实现减重的目标。近年来,随着工程塑料及复合材料等非金属材料在汽车内饰、外饰及功能件应用方面的日趋成熟,替代金属将它们用作结构件正成为汽车制造业新的研究课题。这其中,尤其以汽车主承力结构件(简称“主结构件“)的轻量化为制造研究的重点和难点。
近些年来,随着长纤维增强复合材料(LFT)和片状模复合材料(SMC)及其加工技术的快速发展,国内外已出现了由这类材料经模压工艺制成的零部件,如车门骨架、发动机托架、座椅骨架及散热器支架等。然而,由于材料本身的限制,其强度、刚性及抗冲击性等均不能满足结构件特别是主结构件的要求。

图2 在2005年JEC展会中展出的复合材料车身结构
主结构件,包括汽车的A、B、C柱,以及由翼子板、前围、侧围、后围、顶梁和底板等构成的车身框架。由于是汽车的主要承载部件,为了确保足够的安全性能,汽车厂商会选择强度、刚性及耐冲击性能均很高的材料,通常是复合材料层合结构。相比之下,次承力结构件,包括车门、发罩、行李舱门和顶板等,它们通常使用的是复合材料三明治夹心结构(包括蜂窝夹心、泡沫夹心和轻木夹心等芯材)和层和结构。在此,暂不对三明治夹心结构进行表述,主要介绍复合材料实体层合结构。
在汽车工业发达国家,一些小批量生产的高档汽车及赛车已陆续使用了碳纤增强环氧树脂复合材料制成的主结构件和次承力结构件,其强度、刚性、抗疲劳性及其他各项性能指标均可满足设计要求,可与传统的金属材料部件相媲美。此外,此类产品还表现出了极好的抗腐蚀和耐腐蚀性能。与同体积的铝合金构件相比,减重可达50%。下面将从材料、加工工艺等方面对此进行详细阐述。
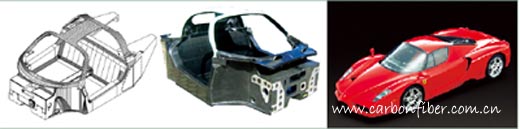
图3 Ferrari Enzo 复合材料车身
碳纤维增强环氧树脂复合材料
作为一种设计灵活、轻质、高强、耐冲击及耐腐蚀的材料,环氧树脂基复合材料可用于制造多种汽车部件。除了车顶棚、门外板、翼子板以及发动机罩等车身部件外,它还可用于汽车主结构件。由此类材料制成的汽车部件不仅大大提高了汽车的安全性能,而且还降低了车重,减少了燃油消耗,提高了经济性,另外改善了美观性,如为车身带来碳纤维的外观效果。

图4 制袋完毕,进入热压罐加热加压固化
根据应用的不同,增强材料可选用玻璃纤维、碳纤维及芳纶纤维,甚至硼纤维等。对于主结构件而言,由碳纤维、芳纶纤维或硼纤维增强的环氧树脂基复合材料能够提供更高的强度和刚性,因此成为主结构件的首选材料。近年来,国外一些高档汽车如奔驰、宝马、保时捷和莲花等,以及世界上的几大赛车品牌,如法拉利、玛莎拉蒂、兰博基尼和波尔舍等,均已采用了由碳纤增强环氧树脂复合材料制成的主结构部件。此外,F1方程式赛车还全部采用了碳纤和硼纤维增强环氧树脂复合材料制成的车身。一般,碳纤增强环氧树脂复合材料中的纤维含量在60%~70%左右。与玻纤增强的环氧树脂相比,其密度更低、质量更轻、刚性更好且质感更加美观;与金属材料相比,其强度更优,抗疲劳性能更佳。不仅如此,根据应用要求,还可对碳纤增强环氧树脂进行局部或整体增韧处理,即通过加入一些热塑性树脂,如PEEK和PEKK等,提高材料的耐冲击性能,使其可提供更好的安全性能。由于具有优异的综合性能优势,目前碳纤增强环氧树脂复合材料已被大量用于飞机的主承力结构和次承力结构中,最新研制的波音787商用飞机所使用的复合材料量已占到飞机总质量的50%。
碳纤维增强环氧树脂复合材料主结构件的加工工艺
众所周知,热固性复合材料的可设计自由度非常大。在制件的生产过程中,完全可以根据制品的最终使用性能要求,选择不同的纤维和基体树脂,然后按照不同的方向和厚度完成纤维的铺层。然而,由于此类材料的生产工艺目前仍以手工操作为主,机械化程度不高,因此很少能实现量产。

图5 采用预浸料/热压罐工艺的生产现场
目前常用的热固性复合材料制件的生产工艺主要包括:手糊成型,手糊袋压成型(Hand lay-up with bagging film),喷射成型,缠绕、拉挤成型,树脂传递模塑成型(Resin transfer molding,简称“RTM”),树脂胶膜浸润成型(Resin film infusion,简称“RFI”)以及预浸料/热压罐成型和模压成型等。对于制作汽车主结构件而言,适合的生产工艺主要为手糊袋压成型、RTM、RFI以及预浸料/热压罐成型等。至于手糊成型,由于生产出的部件孔隙率较高,其强度达不到主结构件的要求,因此一般不予采用。目前,只有RTM、RFI和预浸料/热压罐成型是可以量产的生产工艺。
1、手糊袋压成型
与普通的手糊成型相类似,手糊袋压成型也是由手工将树脂和纤维织物交替地铺层在已涂有脱模剂的模具上,使其达到设计厚度要求。所不同的是,在进行加热加压前需要先制袋,制袋的目的是为了在铺层间形成真空并达到一定的接触压力,以降低最终制件的孔隙率,同时提高层间剪切强度。制袋完成后,即可将其放入热压罐或固化炉中,经加热加压后成型。这种工艺方法劳动强度大,生产周期长,工作环境差,但成本低,目前很少被用于主结构件的制造中。
2、树脂传递模塑成型
树脂传递模塑成型(RTM)是一种闭模成型工艺,对于要求双面光滑且形状复杂的部件较为适合,汽车的A、B、C柱以及翼子板等部件可采用该成型工艺。其特点是,先按设计要求在模具型腔中放置增强材料预成型体,然后合模加压,从浇口处向型腔中灌注预先计量好的定量液态树脂,使其充满纤维预成型体的纤维间空隙,经加热固化后成型。当模具本身带有加热功能时,加热固化过程可直接在模具中完成,否则可使用固化炉完成此过程。该工艺可使用的纤维增强材料包括两种类型,一种为手工铺贴纤维,另一种是经过三维编织的预成型纤维。
为了确保主结构件获得更高的强度和质量,还可采用真空辅助的RTM工艺(简称“VARTM”)。该工艺是在合模后,先对型腔抽真空,然后再灌注树脂,这样可以有效地排除型腔中的空气,从而降低制品的孔隙率以提高强度。
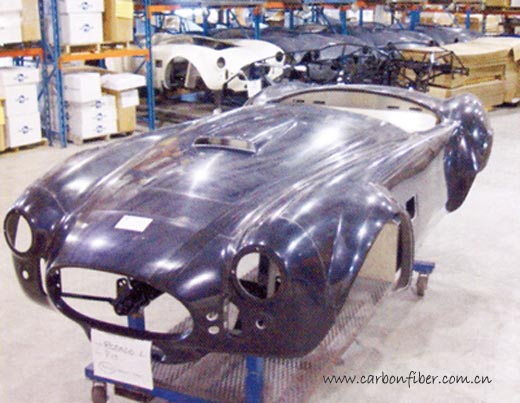
图6 采用RFI工艺制作的车身
需要说明的是,由于树脂是在闭模状态下被灌注到型腔中的,压力越大,树脂的浸润性就越好,可保证树脂可以充满整个型腔。因此,RTM工艺对模具的要求相对较高,要求模具要具有较高的强度,以承受极高的压力和温度。例如,当固化温度为180℃时,要求模具必须能够耐受200℃的高温,同时要能够承受3~4kg/cm2的压力。当然这是指用于生产数量较少的非金属模具而言,对于批量较大的零件,通常采用金属模具。不仅如此,模具的浇口和冒口位置的选取和设计也非常关键,一般需要凭经验,或在电脑上进行仿真模拟,否则会出现“干区”或“贫胶”现象。除了需要使用RTM注射机等专用设备外,RTM工艺一般不需使用热压罐,因而其设备成本相对较低。总之,采用RTM工艺生产的制品具有较高的力学强度和良好的表面质量和较高的尺寸精度,与手糊袋压成型相比,其生产效率较高。
3、预浸料/热压罐成型与树脂胶膜浸润成型
无论是手糊袋压成型还是树脂传递模塑成型,铺层是一件费时费力的事情,要求技工要富有经验且手艺娴熟。正因如此,使得这两种工艺生产效率低下,不能满足较高的量产需求。
为了解决这一问题,目前一些材料供应商开发出了所谓的“预浸料”。这是一种树脂与纤维预混好的半固化态材料,即纤维预先经过树脂浸润,并将被树脂浸润过的纤维铺放到特殊载体上,形成布状或带状预浸料,甚至丝状预浸料。其工艺特点是,逐层铺贴预浸料于模具上,形成零件叠层,然后经热压罐加压加热固化成型。使用该材料时,在操作过程中不易出现纤维的滑动和弯曲现象,纤维方向的一致性和准直度可以得到较好的控制。此外,在热压罐压力的作用下,可以实现较高的纤维含量,故可以得到较高的力学性能。
由于使用半成品的预浸料,可以连续铺贴,提高了速度,因而取代了以往重复交替的纤维和树脂的逐层铺贴工序,使得生产效率大为提高,成为一种普遍采用的量产化的生产工艺。根据制品的不同,预浸料成型工艺的产量一般在几千到几万件之间,非常适合于定制产品的生产。

图7 Mosler MT900S全复材车身
一般情况下,预浸料成卷状供应。为了防止受热后失效,通常需要将其放置在-18℃的低温环境中保存。使用时,先对其解冻,然后按照电脑上排序好的零件展开图切割下料,其切割可由机器完成。下料后,根据铺层设计、按施工工艺要求在模具上进行手工逐层铺贴。接着进行制袋,以使其内部处于真空状态并产生负压,最终消除成型过程中的孔隙率。制袋完成后,将其送入热压罐或固化炉中,在170~180℃的温度下,6~8h即固化成型。
预浸料/热压罐成型工艺的优点是:施工简便,对工人的技能要求不高,生产效率高,制品质量稳定且强度高,因此,该工艺已成为汽车结构件的主流生产技术。需要说明的是,在热压罐中固化成型的制品与在固化炉中成型的制品相比,其致密性更高。这是因为热压罐可同时加热加压,其施加的压力通常为2~3个大气压,而固化炉则不能施压,这使得在热压罐中成型的制品具有更高的致密度,其强度性能更好,因而更适合于主结构件的成型。对于次结构件而言,固化炉成型完全可满足其强度和质量要求。当然,热压罐的成本几乎为固化炉的2~3倍。
尽管预浸料/热压罐成型工艺能进一步提高制品的强度和质量,同时能实现量产化,但其昂贵的材料及设备成本却使得汽车厂商望而却步,目前也只有一些高档汽车和赛车的结构件采用这种成型工艺。
图8 铺贴制袋完毕的零件准备进热压罐固化
为了降低成本,可以用树脂胶膜浸润成型(RFI)工艺取代预浸料成型工艺。该工艺是在干纤维的下面铺放胶膜,并将零件和模具包覆于真空袋中,在热压罐内完成固化成型。在固化过程中,随着温度的升高,胶膜熔化,在压力和真空的作用下,树脂浸润分散到纤维内部空隙固化成型。与预浸料/热压罐工艺类似,RFI工艺施工方便,不需要高技能的操作人员,并且制品的质量稳定、强度高。由于该工艺不使用预浸料,因而材料成本相对降低,并可对纤维进行缝编处理,加强了零件方向上的强度,对大型制件有一定益处。当制品需要双面光时,还可采用闭模热压成型的方式。
主要的碳纤维材料供应商
由于制造工艺复杂,目前碳纤维制造技术主要集中在全球少数几家厂商手中,并且每家厂商所采用的工艺也不尽相同。另外随着航空市场的发展,在产能没有增加的情况下,使得全球的小丝束碳纤维需求相对紧张。目前全球可提供小丝束碳纤维的公司主要有:日本的东丽(Toray)公司、东邦(Toho)公司和三菱(Mesitsubishi)公司,美国的Cytec公司和Hexcel公司,以及台湾的台塑。其中日本3家公司的产量占全球产量的85%,其产品品级涉及航空级、工业级和建筑级。美国Cytec公司只提供航空级的产品,除此之外,Cytec还提供碳纤维增强环氧树脂预浸料。该公司的预浸料包括两种固化温度等级,一种为121℃,另一种为177℃。需要说明的是,随着固化温度的提高,材料的强度也就越好,同时其价格也更加昂贵。
基于碳纤维优越的综合性能优势,除航空和汽车工业外,建筑及其他许多工业领域也已开始关注这种材料。随着需求的日益增大,有限的产能导致碳纤维材料的价格一直居高不下,从而阻碍了其在汽车零部件特别是在汽车结构件应用领域的拓展。
结语
碳纤增强环氧树脂复合材料在部分高档汽车及赛车结构件上的成功应用表明,复合材料完全可以替代金属被用于汽车结构件中。然而,由于材料和设备昂贵,再结合目前汽车生产的工艺链和产品链,以及材料回收重复利用等问题,目前其综合考量成本与效益还不具备量产化的条件,导致碳纤增强环氧树脂复合材料在汽车结构件上的应用具有很大的局限性,这使得钢材及高强度铝合金目前仍然是汽车结构件的主流材料。尽管如此,近年来,长纤维增强热塑性复合材料及其加工技术的快速发展让人们看到了新的希望。随着长纤维增强热塑性复合材料在汽车次承力结构件应用方面的日益成熟,相信人们一定会找到更具成本效益的、同时能满足使用性能要求的材料解决方案,以实现汽车结构件、特别是主结构件的轻量化。
另外,还需要强调的是,作为一种完全有别于金属材料的新型材料,复合材料的汽车零部件设计涉及结构设计、铺层设计及强度设计等多个方面,它离不开大量的计算和经验的积累。要实现复合材料汽车零部件的规模化生产,还需要制订相应的各种标准规范,包括材料的检验和测试标准以及生产工艺规范等。在实际的复合材料设计过程中,应根据材料的利弊特性,针对特定的结构形状、性能和成本要求,在结构设计早期即开始为具体的工艺方案、可能出现的问题以及处理方法等做出尽可能细致的分析和规划,这是实现高水平复合材料机构的重要前提。因此,开发复合材料汽车部件是一个非常复杂的系统工程。目前,国外很多整车厂已建有完整的复合材料工艺体系和设计体系,相比之下,国内的汽车行业在此方面还是一个空白。随着复合材料在汽车工业应用的日益增多,建立专业的研发团队已成为国内汽车整车厂商的当务之急。
来源: 科研转载

图1 安装在底盘上的碳纤维复合材料主承载结构
在汽车工业发达国家,一些小批量生产的高档汽车及赛车已使用了采用碳纤维增强环氧树脂复合材料制成的主承力结构件,其强度、刚性及其他各项性能指标均可与传统的金属材料部件相媲美,同时重量也大为减轻。本文主要从材料和加工工艺等方面对此进行阐述。
自20世纪70年代第一次石油危机爆发以来,“汽车轻量化”便成为全球汽车制造业关注的重点之一。几十年来,人们不断地通过优化结构设计以及采用金属替代方案来实现减重的目标。近年来,随着工程塑料及复合材料等非金属材料在汽车内饰、外饰及功能件应用方面的日趋成熟,替代金属将它们用作结构件正成为汽车制造业新的研究课题。这其中,尤其以汽车主承力结构件(简称“主结构件“)的轻量化为制造研究的重点和难点。
近些年来,随着长纤维增强复合材料(LFT)和片状模复合材料(SMC)及其加工技术的快速发展,国内外已出现了由这类材料经模压工艺制成的零部件,如车门骨架、发动机托架、座椅骨架及散热器支架等。然而,由于材料本身的限制,其强度、刚性及抗冲击性等均不能满足结构件特别是主结构件的要求。

图2 在2005年JEC展会中展出的复合材料车身结构
主结构件,包括汽车的A、B、C柱,以及由翼子板、前围、侧围、后围、顶梁和底板等构成的车身框架。由于是汽车的主要承载部件,为了确保足够的安全性能,汽车厂商会选择强度、刚性及耐冲击性能均很高的材料,通常是复合材料层合结构。相比之下,次承力结构件,包括车门、发罩、行李舱门和顶板等,它们通常使用的是复合材料三明治夹心结构(包括蜂窝夹心、泡沫夹心和轻木夹心等芯材)和层和结构。在此,暂不对三明治夹心结构进行表述,主要介绍复合材料实体层合结构。
在汽车工业发达国家,一些小批量生产的高档汽车及赛车已陆续使用了碳纤增强环氧树脂复合材料制成的主结构件和次承力结构件,其强度、刚性、抗疲劳性及其他各项性能指标均可满足设计要求,可与传统的金属材料部件相媲美。此外,此类产品还表现出了极好的抗腐蚀和耐腐蚀性能。与同体积的铝合金构件相比,减重可达50%。下面将从材料、加工工艺等方面对此进行详细阐述。
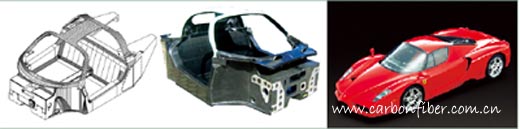
图3 Ferrari Enzo 复合材料车身
碳纤维增强环氧树脂复合材料
作为一种设计灵活、轻质、高强、耐冲击及耐腐蚀的材料,环氧树脂基复合材料可用于制造多种汽车部件。除了车顶棚、门外板、翼子板以及发动机罩等车身部件外,它还可用于汽车主结构件。由此类材料制成的汽车部件不仅大大提高了汽车的安全性能,而且还降低了车重,减少了燃油消耗,提高了经济性,另外改善了美观性,如为车身带来碳纤维的外观效果。

图4 制袋完毕,进入热压罐加热加压固化
根据应用的不同,增强材料可选用玻璃纤维、碳纤维及芳纶纤维,甚至硼纤维等。对于主结构件而言,由碳纤维、芳纶纤维或硼纤维增强的环氧树脂基复合材料能够提供更高的强度和刚性,因此成为主结构件的首选材料。近年来,国外一些高档汽车如奔驰、宝马、保时捷和莲花等,以及世界上的几大赛车品牌,如法拉利、玛莎拉蒂、兰博基尼和波尔舍等,均已采用了由碳纤增强环氧树脂复合材料制成的主结构部件。此外,F1方程式赛车还全部采用了碳纤和硼纤维增强环氧树脂复合材料制成的车身。一般,碳纤增强环氧树脂复合材料中的纤维含量在60%~70%左右。与玻纤增强的环氧树脂相比,其密度更低、质量更轻、刚性更好且质感更加美观;与金属材料相比,其强度更优,抗疲劳性能更佳。不仅如此,根据应用要求,还可对碳纤增强环氧树脂进行局部或整体增韧处理,即通过加入一些热塑性树脂,如PEEK和PEKK等,提高材料的耐冲击性能,使其可提供更好的安全性能。由于具有优异的综合性能优势,目前碳纤增强环氧树脂复合材料已被大量用于飞机的主承力结构和次承力结构中,最新研制的波音787商用飞机所使用的复合材料量已占到飞机总质量的50%。
碳纤维增强环氧树脂复合材料主结构件的加工工艺
众所周知,热固性复合材料的可设计自由度非常大。在制件的生产过程中,完全可以根据制品的最终使用性能要求,选择不同的纤维和基体树脂,然后按照不同的方向和厚度完成纤维的铺层。然而,由于此类材料的生产工艺目前仍以手工操作为主,机械化程度不高,因此很少能实现量产。

图5 采用预浸料/热压罐工艺的生产现场
目前常用的热固性复合材料制件的生产工艺主要包括:手糊成型,手糊袋压成型(Hand lay-up with bagging film),喷射成型,缠绕、拉挤成型,树脂传递模塑成型(Resin transfer molding,简称“RTM”),树脂胶膜浸润成型(Resin film infusion,简称“RFI”)以及预浸料/热压罐成型和模压成型等。对于制作汽车主结构件而言,适合的生产工艺主要为手糊袋压成型、RTM、RFI以及预浸料/热压罐成型等。至于手糊成型,由于生产出的部件孔隙率较高,其强度达不到主结构件的要求,因此一般不予采用。目前,只有RTM、RFI和预浸料/热压罐成型是可以量产的生产工艺。
1、手糊袋压成型
与普通的手糊成型相类似,手糊袋压成型也是由手工将树脂和纤维织物交替地铺层在已涂有脱模剂的模具上,使其达到设计厚度要求。所不同的是,在进行加热加压前需要先制袋,制袋的目的是为了在铺层间形成真空并达到一定的接触压力,以降低最终制件的孔隙率,同时提高层间剪切强度。制袋完成后,即可将其放入热压罐或固化炉中,经加热加压后成型。这种工艺方法劳动强度大,生产周期长,工作环境差,但成本低,目前很少被用于主结构件的制造中。
2、树脂传递模塑成型
树脂传递模塑成型(RTM)是一种闭模成型工艺,对于要求双面光滑且形状复杂的部件较为适合,汽车的A、B、C柱以及翼子板等部件可采用该成型工艺。其特点是,先按设计要求在模具型腔中放置增强材料预成型体,然后合模加压,从浇口处向型腔中灌注预先计量好的定量液态树脂,使其充满纤维预成型体的纤维间空隙,经加热固化后成型。当模具本身带有加热功能时,加热固化过程可直接在模具中完成,否则可使用固化炉完成此过程。该工艺可使用的纤维增强材料包括两种类型,一种为手工铺贴纤维,另一种是经过三维编织的预成型纤维。
为了确保主结构件获得更高的强度和质量,还可采用真空辅助的RTM工艺(简称“VARTM”)。该工艺是在合模后,先对型腔抽真空,然后再灌注树脂,这样可以有效地排除型腔中的空气,从而降低制品的孔隙率以提高强度。
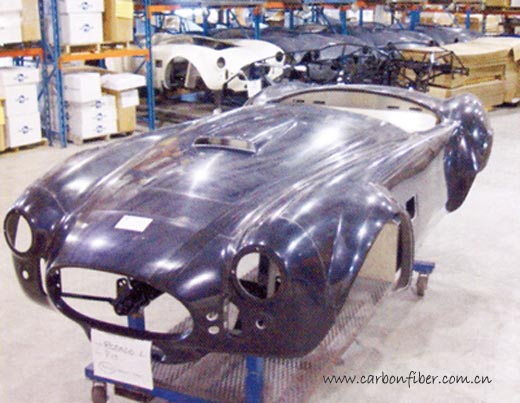
图6 采用RFI工艺制作的车身
需要说明的是,由于树脂是在闭模状态下被灌注到型腔中的,压力越大,树脂的浸润性就越好,可保证树脂可以充满整个型腔。因此,RTM工艺对模具的要求相对较高,要求模具要具有较高的强度,以承受极高的压力和温度。例如,当固化温度为180℃时,要求模具必须能够耐受200℃的高温,同时要能够承受3~4kg/cm2的压力。当然这是指用于生产数量较少的非金属模具而言,对于批量较大的零件,通常采用金属模具。不仅如此,模具的浇口和冒口位置的选取和设计也非常关键,一般需要凭经验,或在电脑上进行仿真模拟,否则会出现“干区”或“贫胶”现象。除了需要使用RTM注射机等专用设备外,RTM工艺一般不需使用热压罐,因而其设备成本相对较低。总之,采用RTM工艺生产的制品具有较高的力学强度和良好的表面质量和较高的尺寸精度,与手糊袋压成型相比,其生产效率较高。
3、预浸料/热压罐成型与树脂胶膜浸润成型
无论是手糊袋压成型还是树脂传递模塑成型,铺层是一件费时费力的事情,要求技工要富有经验且手艺娴熟。正因如此,使得这两种工艺生产效率低下,不能满足较高的量产需求。
为了解决这一问题,目前一些材料供应商开发出了所谓的“预浸料”。这是一种树脂与纤维预混好的半固化态材料,即纤维预先经过树脂浸润,并将被树脂浸润过的纤维铺放到特殊载体上,形成布状或带状预浸料,甚至丝状预浸料。其工艺特点是,逐层铺贴预浸料于模具上,形成零件叠层,然后经热压罐加压加热固化成型。使用该材料时,在操作过程中不易出现纤维的滑动和弯曲现象,纤维方向的一致性和准直度可以得到较好的控制。此外,在热压罐压力的作用下,可以实现较高的纤维含量,故可以得到较高的力学性能。
由于使用半成品的预浸料,可以连续铺贴,提高了速度,因而取代了以往重复交替的纤维和树脂的逐层铺贴工序,使得生产效率大为提高,成为一种普遍采用的量产化的生产工艺。根据制品的不同,预浸料成型工艺的产量一般在几千到几万件之间,非常适合于定制产品的生产。

图7 Mosler MT900S全复材车身
一般情况下,预浸料成卷状供应。为了防止受热后失效,通常需要将其放置在-18℃的低温环境中保存。使用时,先对其解冻,然后按照电脑上排序好的零件展开图切割下料,其切割可由机器完成。下料后,根据铺层设计、按施工工艺要求在模具上进行手工逐层铺贴。接着进行制袋,以使其内部处于真空状态并产生负压,最终消除成型过程中的孔隙率。制袋完成后,将其送入热压罐或固化炉中,在170~180℃的温度下,6~8h即固化成型。
预浸料/热压罐成型工艺的优点是:施工简便,对工人的技能要求不高,生产效率高,制品质量稳定且强度高,因此,该工艺已成为汽车结构件的主流生产技术。需要说明的是,在热压罐中固化成型的制品与在固化炉中成型的制品相比,其致密性更高。这是因为热压罐可同时加热加压,其施加的压力通常为2~3个大气压,而固化炉则不能施压,这使得在热压罐中成型的制品具有更高的致密度,其强度性能更好,因而更适合于主结构件的成型。对于次结构件而言,固化炉成型完全可满足其强度和质量要求。当然,热压罐的成本几乎为固化炉的2~3倍。
尽管预浸料/热压罐成型工艺能进一步提高制品的强度和质量,同时能实现量产化,但其昂贵的材料及设备成本却使得汽车厂商望而却步,目前也只有一些高档汽车和赛车的结构件采用这种成型工艺。

图8 铺贴制袋完毕的零件准备进热压罐固化
为了降低成本,可以用树脂胶膜浸润成型(RFI)工艺取代预浸料成型工艺。该工艺是在干纤维的下面铺放胶膜,并将零件和模具包覆于真空袋中,在热压罐内完成固化成型。在固化过程中,随着温度的升高,胶膜熔化,在压力和真空的作用下,树脂浸润分散到纤维内部空隙固化成型。与预浸料/热压罐工艺类似,RFI工艺施工方便,不需要高技能的操作人员,并且制品的质量稳定、强度高。由于该工艺不使用预浸料,因而材料成本相对降低,并可对纤维进行缝编处理,加强了零件方向上的强度,对大型制件有一定益处。当制品需要双面光时,还可采用闭模热压成型的方式。
主要的碳纤维材料供应商
由于制造工艺复杂,目前碳纤维制造技术主要集中在全球少数几家厂商手中,并且每家厂商所采用的工艺也不尽相同。另外随着航空市场的发展,在产能没有增加的情况下,使得全球的小丝束碳纤维需求相对紧张。目前全球可提供小丝束碳纤维的公司主要有:日本的东丽(Toray)公司、东邦(Toho)公司和三菱(Mesitsubishi)公司,美国的Cytec公司和Hexcel公司,以及台湾的台塑。其中日本3家公司的产量占全球产量的85%,其产品品级涉及航空级、工业级和建筑级。美国Cytec公司只提供航空级的产品,除此之外,Cytec还提供碳纤维增强环氧树脂预浸料。该公司的预浸料包括两种固化温度等级,一种为121℃,另一种为177℃。需要说明的是,随着固化温度的提高,材料的强度也就越好,同时其价格也更加昂贵。
基于碳纤维优越的综合性能优势,除航空和汽车工业外,建筑及其他许多工业领域也已开始关注这种材料。随着需求的日益增大,有限的产能导致碳纤维材料的价格一直居高不下,从而阻碍了其在汽车零部件特别是在汽车结构件应用领域的拓展。
结语
碳纤增强环氧树脂复合材料在部分高档汽车及赛车结构件上的成功应用表明,复合材料完全可以替代金属被用于汽车结构件中。然而,由于材料和设备昂贵,再结合目前汽车生产的工艺链和产品链,以及材料回收重复利用等问题,目前其综合考量成本与效益还不具备量产化的条件,导致碳纤增强环氧树脂复合材料在汽车结构件上的应用具有很大的局限性,这使得钢材及高强度铝合金目前仍然是汽车结构件的主流材料。尽管如此,近年来,长纤维增强热塑性复合材料及其加工技术的快速发展让人们看到了新的希望。随着长纤维增强热塑性复合材料在汽车次承力结构件应用方面的日益成熟,相信人们一定会找到更具成本效益的、同时能满足使用性能要求的材料解决方案,以实现汽车结构件、特别是主结构件的轻量化。
另外,还需要强调的是,作为一种完全有别于金属材料的新型材料,复合材料的汽车零部件设计涉及结构设计、铺层设计及强度设计等多个方面,它离不开大量的计算和经验的积累。要实现复合材料汽车零部件的规模化生产,还需要制订相应的各种标准规范,包括材料的检验和测试标准以及生产工艺规范等。在实际的复合材料设计过程中,应根据材料的利弊特性,针对特定的结构形状、性能和成本要求,在结构设计早期即开始为具体的工艺方案、可能出现的问题以及处理方法等做出尽可能细致的分析和规划,这是实现高水平复合材料机构的重要前提。因此,开发复合材料汽车部件是一个非常复杂的系统工程。目前,国外很多整车厂已建有完整的复合材料工艺体系和设计体系,相比之下,国内的汽车行业在此方面还是一个空白。随着复合材料在汽车工业应用的日益增多,建立专业的研发团队已成为国内汽车整车厂商的当务之急。
来源: 科研转载