美国开发碳纤维复合材料汽车发动机
By www.carbonfiber.com.cn
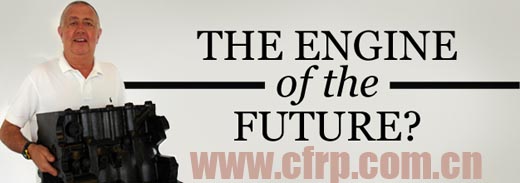
位于美国佛罗里达州棕榈滩的Polimotor Research Inc.复合材料研发公司开发了一种新的、轻巧、碳纤维复合材料四缸发动机缸体,该发动机缸体是由该公司的总裁&创始人Matti Holtzberg设计的。
东邦耐克丝碳纤维被选为环氧树脂基增强材料,复合材料铸件公司使用其专有的成型工艺使高性能混合物模塑成型发动机缸体,该工艺使用低成本的加工材料,循环时间比传统的碳纤维复合材料的成型方法更快。
新发动机缸体重量比铝的轻45%-50%,在高性能发动机业务中轻量化是一个重要的竞争优势,它将吸引来自世界各地汽车行业的兴趣,轻量化是至关重要的,特别在混合动力汽车中。
被浇注的复合材料缸体是净形状,消除了二次加工的麻烦,振动噪声显着减少,耐腐蚀, 意味着碳排放量大量减少碳。此外,和压铸工艺相比,模具工具成本减少50%。碳纤维复合材料缸体比合金的重量轻20磅。在不久的未来,这种四缸和八缸发动机缸体将应用于赛车、OEM汽车、卡车和海洋。

Carbon-fiber composites have infiltrated practically every nook and cranny of today’s supercar. We’ve got carbon monocoque structural cores, carbon-ceramic brake rotors, and carbon-fiber-reinforced body panels. Taking this approach to the radical extreme, Formula 1 constructors have long used molded carbon-fiber suspension, wing, and transmission-housing components. Contemporary F1 steering wheels are even made of this light, stiff material to save a few ounces.
Ironically, the single heaviest part of practically every car—the engine block—is one of the last items awaiting conversion from metal to molded carbon fiber. Enter Florida engineer Matti Holtzberg. For the past four decades, he’s worked to create an ultralight plastic engine with sufficient stamina to replace engine blocks made from cast iron or aluminum. With strategic use of inserts to handle the heat and concentrated loads, he has engineered a composite engine block that may be ready to send cast metal the way of the buggy whip.
After years experimenting with various resins reinforced with glass fibers, Holtzberg recently expanded his focus to include more expensive carbon-fiber materials. Realizing that the hard-core racing community is always eager to gain a competitive weight-saving edge, he knew there was a market for a composite cylinder block capable of trimming a few pounds. Indulging his best entrepreneurial instincts, he purchased tooling and configured his West Palm Beach lab to cast the first dozen carbon-fiber-reinforced engine blocks patterned after Ford’s 2.0-liter Duratec engine.

Now Polimotor's founder, Matti Holtzberg, left, has paired with James Huntsman, right, the owner of a major automotive chemicals supplier, to bring the plastic engine to mass market at last. (Source: New York Times)
According to Holtzberg, his mold is a six-piece aluminum jigsaw puzzle consisting of a base plate, four side panels, and a top cover. A removable core, which forms the water jacket, oil drains, and main oil galley, fits inside. During assembly, the mold also is loaded with various aluminum parts: 71 threaded inserts and five main bearing saddles. After casting, four Siamesed cylinders are placed in the water jacket.
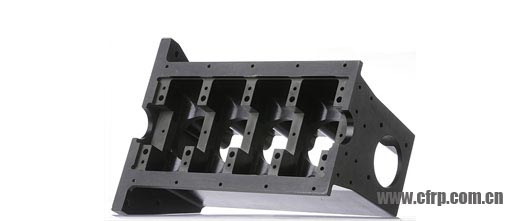
After prepping the mold, epoxy resin and six-mm-long carbon fibers are stirred together in an industrial mixer. The resulting batter, which has the consistency of oatmeal, is warmed slightly and then poured into the mold. It’s left to cure for two hours, although Holtzberg adds that minor procedural changes would allow molding a block in only five minutes.
One of the attributes associated with this accurate molding process is that the composite surfaces require no finishing operations and minimal machining is necessary. After casting, the main bearing saddles are line bored and the cylinders are cut to accept liners. Holtzberg plans on switching to a molybdenum plasma spray coating in place of aluminum cylinder liners to trim additional pounds. That will boost the weight savings over an aluminum block from 18.2 pounds to more than twenty pounds.
Holtzberg will add several carbon-fiber bolt-on components, such as the oil pan, cam cover, intake manifold, and fuel rail to create a kit he intends to offer racers. After purchasing the kit, each customer can commission their favorite engine builder to assemble the package according to specific racing or rallying needs.
Holtzberg has not yet established a price for his carbon-fiber engine, but it’s unlikely many Ford Focus owners will be interested in spending what could be $2500 (or more) per pound of weight saved.
Plastic Milestones
1907–1909 Belgian chemist Dr. Leo Baekeland developed Bakelite, the world’s first commercially successful plastic. Billiard balls, 78-rpm records, and dial-telephone housings were some of the initial applications.
1930s Soybean enthusiast Henry Ford began installing plastic parts in his automobiles. Horn buttons, shift knobs, interior door handles, and distributor heads were molded from the meal processed from soybeans grown on Ford farms.
1940 Anticipating steel shortages during World War II, Henry Ford commissioned a full car body made of molded plastic. At a 1941 demonstration, he swung an ax at his personal Ford which was fitted with plastic trunklid. The ax bounced off without damaging the panel.
1953 Chevrolet began producing Corvettes with bodies made of fiberglass-reinforced plastic. More than 1.5 million have been sold.
1969 Matti Holtzberg read an article in a technical magazine at the Hackensack, New Jersey, public library espousing a new plastic allegedly tough enough to withstand the harsh conditions existing inside car engines. Holtzberg obtained a sample of the French material, which he used to make an experimental piston. After 20 minutes of operation inside an Austin Mini engine, combustion heat burned a hole through his first plastic piston’s crown.
1970s Holtzberg made and sold ultralight plastic pistons—now topped with aluminum crowns—for racing use.
1979 Holtzberg founded Polimotor (shorthand for polymer motor) to develop the world’s first plastic-intensive engine.
1980 After Holtzberg’s first engine ran, Automotive Industries magazine featured it in a cover story.
1982 By the time Popular Science chimed in, Holtzberg’s second-generation Polimotor produced 300 hp and weighed 152 pounds compared to 88 hp and 415 pounds for a contemporary Ford Pinto engine.
1984–1985 A Lola sports car powered by a Polimotor and backed by Amoco Chemical ran a half-dozen IMSA Camel Light road races with a best finish of third at Lime Rock. One broken connecting rod (purchased from a supplier) was the only major failure.
1986 With the durability point proven in racing, Holtzberg shifted his focus to mass production. With Amoco out of the picture, he changed from Torlon to more affordable phenolic resin, the first commercial polymer and the material Henry Ford used to bind his soybean fibers.
1990 Holtzberg established Composite Castings, now located in West Palm Beach, Florida.
1992 After successfully using carbon-fiber-reinforced composite monocoques in Formula 1, McLaren Cars introduced the three-seat F1 coupe for road use.
1998–2002 Three patents covering technology related to the casting of phenolic or epoxy resin reinforced with fiberglass were issued to Holtzberg. More than a dozen licensees now use his technology for rapid prototyping and other applications.
2009 Composite Casting formed a strategic partnership with resin supplier Huntsman Chemical.
2010 A strategic partnership with carbon-fiber supplier Toho Tenax Americas was signed.
2011 Composite Castings manufactured a dozen experimental carbon-fiber-composite versions of Ford’s 2.0-liter Duratec four-cylinder engine block.
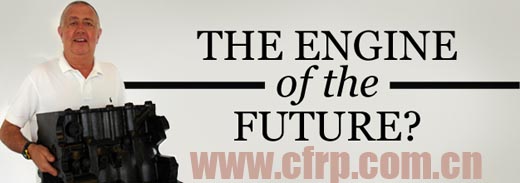
位于美国佛罗里达州棕榈滩的Polimotor Research Inc.复合材料研发公司开发了一种新的、轻巧、碳纤维复合材料四缸发动机缸体,该发动机缸体是由该公司的总裁&创始人Matti Holtzberg设计的。
东邦耐克丝碳纤维被选为环氧树脂基增强材料,复合材料铸件公司使用其专有的成型工艺使高性能混合物模塑成型发动机缸体,该工艺使用低成本的加工材料,循环时间比传统的碳纤维复合材料的成型方法更快。
新发动机缸体重量比铝的轻45%-50%,在高性能发动机业务中轻量化是一个重要的竞争优势,它将吸引来自世界各地汽车行业的兴趣,轻量化是至关重要的,特别在混合动力汽车中。
被浇注的复合材料缸体是净形状,消除了二次加工的麻烦,振动噪声显着减少,耐腐蚀, 意味着碳排放量大量减少碳。此外,和压铸工艺相比,模具工具成本减少50%。碳纤维复合材料缸体比合金的重量轻20磅。在不久的未来,这种四缸和八缸发动机缸体将应用于赛车、OEM汽车、卡车和海洋。

Carbon-fiber composites have infiltrated practically every nook and cranny of today’s supercar. We’ve got carbon monocoque structural cores, carbon-ceramic brake rotors, and carbon-fiber-reinforced body panels. Taking this approach to the radical extreme, Formula 1 constructors have long used molded carbon-fiber suspension, wing, and transmission-housing components. Contemporary F1 steering wheels are even made of this light, stiff material to save a few ounces.
Ironically, the single heaviest part of practically every car—the engine block—is one of the last items awaiting conversion from metal to molded carbon fiber. Enter Florida engineer Matti Holtzberg. For the past four decades, he’s worked to create an ultralight plastic engine with sufficient stamina to replace engine blocks made from cast iron or aluminum. With strategic use of inserts to handle the heat and concentrated loads, he has engineered a composite engine block that may be ready to send cast metal the way of the buggy whip.
After years experimenting with various resins reinforced with glass fibers, Holtzberg recently expanded his focus to include more expensive carbon-fiber materials. Realizing that the hard-core racing community is always eager to gain a competitive weight-saving edge, he knew there was a market for a composite cylinder block capable of trimming a few pounds. Indulging his best entrepreneurial instincts, he purchased tooling and configured his West Palm Beach lab to cast the first dozen carbon-fiber-reinforced engine blocks patterned after Ford’s 2.0-liter Duratec engine.

Now Polimotor's founder, Matti Holtzberg, left, has paired with James Huntsman, right, the owner of a major automotive chemicals supplier, to bring the plastic engine to mass market at last. (Source: New York Times)
According to Holtzberg, his mold is a six-piece aluminum jigsaw puzzle consisting of a base plate, four side panels, and a top cover. A removable core, which forms the water jacket, oil drains, and main oil galley, fits inside. During assembly, the mold also is loaded with various aluminum parts: 71 threaded inserts and five main bearing saddles. After casting, four Siamesed cylinders are placed in the water jacket.
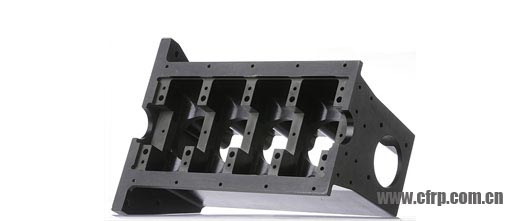
After prepping the mold, epoxy resin and six-mm-long carbon fibers are stirred together in an industrial mixer. The resulting batter, which has the consistency of oatmeal, is warmed slightly and then poured into the mold. It’s left to cure for two hours, although Holtzberg adds that minor procedural changes would allow molding a block in only five minutes.
One of the attributes associated with this accurate molding process is that the composite surfaces require no finishing operations and minimal machining is necessary. After casting, the main bearing saddles are line bored and the cylinders are cut to accept liners. Holtzberg plans on switching to a molybdenum plasma spray coating in place of aluminum cylinder liners to trim additional pounds. That will boost the weight savings over an aluminum block from 18.2 pounds to more than twenty pounds.
Holtzberg will add several carbon-fiber bolt-on components, such as the oil pan, cam cover, intake manifold, and fuel rail to create a kit he intends to offer racers. After purchasing the kit, each customer can commission their favorite engine builder to assemble the package according to specific racing or rallying needs.
Holtzberg has not yet established a price for his carbon-fiber engine, but it’s unlikely many Ford Focus owners will be interested in spending what could be $2500 (or more) per pound of weight saved.
Plastic Milestones
1907–1909 Belgian chemist Dr. Leo Baekeland developed Bakelite, the world’s first commercially successful plastic. Billiard balls, 78-rpm records, and dial-telephone housings were some of the initial applications.
1930s Soybean enthusiast Henry Ford began installing plastic parts in his automobiles. Horn buttons, shift knobs, interior door handles, and distributor heads were molded from the meal processed from soybeans grown on Ford farms.
1940 Anticipating steel shortages during World War II, Henry Ford commissioned a full car body made of molded plastic. At a 1941 demonstration, he swung an ax at his personal Ford which was fitted with plastic trunklid. The ax bounced off without damaging the panel.
1953 Chevrolet began producing Corvettes with bodies made of fiberglass-reinforced plastic. More than 1.5 million have been sold.
1969 Matti Holtzberg read an article in a technical magazine at the Hackensack, New Jersey, public library espousing a new plastic allegedly tough enough to withstand the harsh conditions existing inside car engines. Holtzberg obtained a sample of the French material, which he used to make an experimental piston. After 20 minutes of operation inside an Austin Mini engine, combustion heat burned a hole through his first plastic piston’s crown.
1970s Holtzberg made and sold ultralight plastic pistons—now topped with aluminum crowns—for racing use.
1979 Holtzberg founded Polimotor (shorthand for polymer motor) to develop the world’s first plastic-intensive engine.
1980 After Holtzberg’s first engine ran, Automotive Industries magazine featured it in a cover story.
1982 By the time Popular Science chimed in, Holtzberg’s second-generation Polimotor produced 300 hp and weighed 152 pounds compared to 88 hp and 415 pounds for a contemporary Ford Pinto engine.
1984–1985 A Lola sports car powered by a Polimotor and backed by Amoco Chemical ran a half-dozen IMSA Camel Light road races with a best finish of third at Lime Rock. One broken connecting rod (purchased from a supplier) was the only major failure.
1986 With the durability point proven in racing, Holtzberg shifted his focus to mass production. With Amoco out of the picture, he changed from Torlon to more affordable phenolic resin, the first commercial polymer and the material Henry Ford used to bind his soybean fibers.
1990 Holtzberg established Composite Castings, now located in West Palm Beach, Florida.
1992 After successfully using carbon-fiber-reinforced composite monocoques in Formula 1, McLaren Cars introduced the three-seat F1 coupe for road use.
1998–2002 Three patents covering technology related to the casting of phenolic or epoxy resin reinforced with fiberglass were issued to Holtzberg. More than a dozen licensees now use his technology for rapid prototyping and other applications.
2009 Composite Casting formed a strategic partnership with resin supplier Huntsman Chemical.
2010 A strategic partnership with carbon-fiber supplier Toho Tenax Americas was signed.
2011 Composite Castings manufactured a dozen experimental carbon-fiber-composite versions of Ford’s 2.0-liter Duratec four-cylinder engine block.