宝马碳纤维车身结构整装待发
By www.carbonfiber.com.cn
宝马合作伙伴西格里复合材料公司(SGL Composites)已经开始为2014款宝马i3和i8车型制造零部件。国际汽车工程杂志(AEI)参观了这家走在行业前列的美国碳纤维工厂,见证了在车辆轻量化方面可能会对铝合金造成巨大挑战的创新材料的生产。
宝马公司在2008年发布了其新开发的电动汽车家族之后不久,这家汽车制造商再次尝试了一次新的冒险,有望使其在未来电动汽车和混合动力车领域获得飞跃性的突破。
为了抵消锂离子电池组带来的重量负担,公司决定车型的整个乘客舱结构用更加坚固、轻质、耐腐蚀的碳纤维增强复合材料成型。碳纤维乘客舱单元——密度只有铝的一半,比钢铁轻50%——将与大量采用铝合金材料的底盘相匹配,而车身外部面板将使用热塑性塑料。
2014款宝马i3电动汽车将于今年晚些时候将投入生产,总的目标是将其重量减轻200kg(440lb),来抵消电池重量。2014款i8车型——插电式混合动力跑车也将获得相同的减重效果。一般来说,一辆车重量减轻100kg(220lb),二氧化碳排放量平均来看最高可降低10g/km。而这些车型(宝马所谓Project i子品牌的首批车型)在乘客防护方面的性能都将受益于碳纤维优越的弹性模量及其拉伸强度——这两个参数都超过硼钢。

宝马公司利用自己的供应链,创造了一个大胆的、接近垂直整合的产品开发和加工战略,希望减少碳纤维材料和部件成本,提高每个部件的生产效率,建立其在碳纤维方面的知识产权。
宝马公司为此押宝于这种一直被认为高成本(30美金/磅)、小批量生产且众所周知的主要用于赛车车身、高尔夫球杆和飞机行业的新型材料上,并与欧洲领先复合材料供应商西格里集团共同成立了一家合资企业——西格里汽车碳纤维公司,负责碳纤维材料的开发和制造。合资公司的工厂位于华盛顿州的摩西湖市,西雅图以东约190mi(306km),厂房面积10,250m2,宝马为此投入了1亿美元,彰显了这家汽车制造商对进入未来轻量化车身结构市场的决心。
“我们的目标是希望接近铝合金材料的成本,目前我们还没做到。”西格里汽车公司总经理Joerg Pohlman博士解释道。“但是我们预见在未来几年内会有这么一天,在整个车身结构方面可以接近铝合金的成本。”
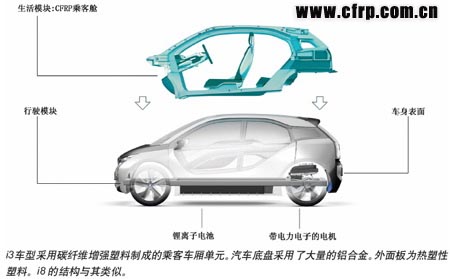
雄心勃勃的增长计划
2011年开业的位于摩西湖市的西格里公司是宝马公司第一批在整个车身结构方面都采用碳纤维材料的量产车型(i3)成功的关键,而且要采用可持续、可靠且成本效率高的加工工艺。选择这个偏远的地区是因为华盛顿州东部的干燥气候(太高的湿度不利于碳纤维生产),当然也是因为这个州在哥伦比亚河上建立的水电大坝可以提供的充足且相对廉价的“绿色”电能。

对于摩西湖的西格里公司,电力来源为40英里(64公里)外的瓦纳庞大坝。“我们每千瓦小时支付约3美分[约为美国平均电价的三分之一],在德国的瓦克斯多夫工厂都需要9美分。”Pohlman博士透露。
碳纤维生产需要消耗大量的电能,这也是碳纤维增强复合材料高成本的原因之一,而传统耗时的热压罐式生产工艺也是这家汽车制造商急切想摒弃的。摩西湖市的工厂有两条183m长的生产线,产线上的多重电加热氧化和碳化炉用于将聚丙烯腈聚合物原料的丝束,也称为原丝,转换成键合在一起的碳原子晶体。
晶体在高温、氮封环境下的平行排列使纤维具有优异的强度体积比。几千个直径为7μm的碳纤维被拉伸、清洗、缠绕、干燥、用环氧树脂涂覆并纺成像纱线一样的“长丝丝束”,缠绕在线轴上。材料会用一个“K”号码标记,即所包含的长丝(股线)数量;例如宝马最多使用的50K长丝丝束就有50,000根长丝。
重9kg(20lb)带有黑色光泽的线轴被运往宝马位于德国的瓦克斯多夫(Wackersdorf)工厂。工厂使用专利无皱褶纺织工艺将长丝丝束转化成碳纤维织物,这正是复合材料结构部件的基础。所用树脂配方也由宝马公司制定。
摩西湖市和瓦克斯多夫的工厂是宝马垂直整合的碳纤维部件生产链上的第二和第三环。生产链最初开始于另一家西格里的合资企业——位于日本大竹的三菱丽阳工厂,它生产摩西湖工厂所用的聚丙烯腈原丝。碳纤维毡在离开瓦克斯多夫工厂后,被送往宝马在德国兰茨胡特(Landshut)的工厂,这家工厂多年来专注于各种预成型、冲压及树脂转移成型的碳纤维部件的生产,包括M3和M5的大型车顶板。宝马公司预期今年将为其M系列车型生产超过100万件的碳纤维部件。
截止2012年末在i3样车中单个部件的最快生产周期“少于10分钟――但还没达到9分钟”,Pohlman博士谨慎地说。最终车身是在莱比锡(Leipzig)组装的。
“一旦两条生产线[摩西湖]在2013年中旬准备就绪,我们一年将生产约3000公吨的碳纤维——大约占全球总生产量的8%。根据行业标准,1500吨一条的产线是相当大的。目前我们还有空间可在现在的场地上再增加4条生产线,我们也可以再多购买60英亩土地。”Pohlman博士说道。
他指出除了“i系列”电动汽车外,宝马公司还将在传统内燃机驱动的汽车中增加碳纤维的使用,公司也可能向其他汽车制造商销售碳纤维。
《国际汽车工程》记者在拜访时发现工厂几乎处于“无人”的运营状态,很难发现有80名雇员的迹象——不过随着宝马i系列的产能提升,员工人数将有所增加。目前工厂为4班12小时运转,28天为一轮换周期。
汽车研究中心(Center for Automotive Research)总裁兼CEO及制造方面的专家Jay Baron博士认为碳纤维每磅12美元或者更高的市场价格,与大约2.5美元/磅的铝和1美元/磅的普通高强度钢铁相比,“就购买性而言高得离谱”。他承认这种材料有很多优势,但同时仍然对其中短期前景持怀疑态度。
“采用先进的复合材料可以把许多独立组装的金属部件融合在一起。”Baron博士解释说。“你可以在需要的地方增加强度,而在不需要的地方减少材料使用而减轻重量。如果实现了部件的整合,工厂可以小得多。你可以扔掉至少四分之三的点焊机,但却要增加粘合剂技术相关的设备,而这也不是小的投入。”
他还说,就车身和油漆车间而言,设计一个碳纤维车身结构(i3车型包括35个部件)的组装厂需要从零开始。在宝马看来,通过不断发展和改进,以及碳纤维生产的进一步自动化,这种黑色材料将最终对铝合金形成挑战。
使用碳纤维也带来了其他一些不太明显的改变。宝马公司加大碳纤维复合材料的使用也使其加入了巴伐利亚的纺织制造商贸易集团。Pohlman博士指出,这一加盟使得宝马公司的碳纤维生产基地可以利用纺织行业较低的工资水平,并加入与主导德国汽车制造商的德国金属工业工会(I.G. Metall union)完全不同的另一个工会。
OEM竞相成为碳纤维先锋
汽车行业对将碳纤维部件制造推向大批量生产的兴趣正不断提高。其他汽车制造商也逐渐加入与宝马竞争的队列中,通过战略合作关系来推动碳纤维技术的发展、降低成本、并提高产量。
日本碳纤维巨头东丽与丰田、富士重工和戴姆勒公司达成合作。而其主要的日本竞争对手帝人株式会社也与通用汽车成立了合资企业。福特和陶氏是碳纤维方面的盟友,奥迪的合作者则是西格里集团的第三大股东福伊特。去年大众汽车也入股西格里。甚至兰博基尼也和Quantum复合材料公司及卡拉威高尔夫公司(Callaway Golf)之间签订了一个三方协议。
通用汽车和普拉森碳复合材料公司(Plasan)也在进行其2014款雪佛兰Corvette C7计划,将每辆车的碳纤维车身部件含量提高到30,000-40,000单位体积的水平,这是一个重大飞跃。而去年丰田公司出人意料地与宝马公司联手,共享车辆轻量化技术信息,目前具体合作的项目依然处于保密状态中。
2013年宝马斥巨资投资于碳纤维批量生产的决定差点因为全球经济衰退而被边缘化。
“那段时期说服董事会投入碳纤维增强结构件是很难的。”Pohlman博士回忆道,他在西格里公司任职前为宝马华盛顿特区办公室的管理人员。“但是他们也承认我们必须采取大胆果断的行动,因为我们进入混合动力和电动汽车技术领域已经算是晚的了。我们此前的心态一直是,‘我们有柴油发动机’。”
所以公司开始寻找复合材料伙伴,能跟上i项目快速发展的步伐。这让宝马最终选择了西格里公司——欧洲最大的碳纤维供应商。
宝马的领先地位
宝马的工程师已经为制造汽车零件所需要的碳纤维建立了一个产品“目录”——每种碳纤维产品根据部件不同的应用会记录不同的铺层、纤维的方向和单位面积的重量等。据Pohlman博士介绍,目录的内容正在逐渐增加中。当问及目前的纤维规格时,他说在华盛顿生产的碳纤维密度为1.78 g/cm3。1250°C下的拉伸强度为4000MPa(500 ksi),弹性模量为420GPa(60,915 ksi))。
可回收性是i项目的一个重要元素。宝马开发了创新设备来帮助完成碳纤维增强复合材料加工后的回收。
“这一加工过程还生成了一种“抓绒”,它具有原材料30%-40%的工程特性,我们正在想办法加以利用,”Pohlman博士提到。宝马公司去年晚些时候宣布与波音公司合作,波音每年要使用成千上万吨的基于回收技术的碳纤维。
宝马的竞争对手“正等着我们出错,就像波音公司最早的787项目一样。”Pohlman博士认为。但是他相信公司在技术方面领先于竞争对手三年的时间,“(他们需要至少三年)才能走到我们今天的位置,零部件产量才可以达到我们所计划的数量。”
例如,与宝马现在M3车顶使用的碳纤维相比,i系列车型上用到的新材料制造费用只有其三分之一。“这是一个重大进步,”Pohlman博士说。“i3项目的目标是赚钱——而不只是通过3系来补贴。”
宝马合作伙伴西格里复合材料公司(SGL Composites)已经开始为2014款宝马i3和i8车型制造零部件。国际汽车工程杂志(AEI)参观了这家走在行业前列的美国碳纤维工厂,见证了在车辆轻量化方面可能会对铝合金造成巨大挑战的创新材料的生产。
宝马公司在2008年发布了其新开发的电动汽车家族之后不久,这家汽车制造商再次尝试了一次新的冒险,有望使其在未来电动汽车和混合动力车领域获得飞跃性的突破。
为了抵消锂离子电池组带来的重量负担,公司决定车型的整个乘客舱结构用更加坚固、轻质、耐腐蚀的碳纤维增强复合材料成型。碳纤维乘客舱单元——密度只有铝的一半,比钢铁轻50%——将与大量采用铝合金材料的底盘相匹配,而车身外部面板将使用热塑性塑料。
2014款宝马i3电动汽车将于今年晚些时候将投入生产,总的目标是将其重量减轻200kg(440lb),来抵消电池重量。2014款i8车型——插电式混合动力跑车也将获得相同的减重效果。一般来说,一辆车重量减轻100kg(220lb),二氧化碳排放量平均来看最高可降低10g/km。而这些车型(宝马所谓Project i子品牌的首批车型)在乘客防护方面的性能都将受益于碳纤维优越的弹性模量及其拉伸强度——这两个参数都超过硼钢。

宝马公司利用自己的供应链,创造了一个大胆的、接近垂直整合的产品开发和加工战略,希望减少碳纤维材料和部件成本,提高每个部件的生产效率,建立其在碳纤维方面的知识产权。
宝马公司为此押宝于这种一直被认为高成本(30美金/磅)、小批量生产且众所周知的主要用于赛车车身、高尔夫球杆和飞机行业的新型材料上,并与欧洲领先复合材料供应商西格里集团共同成立了一家合资企业——西格里汽车碳纤维公司,负责碳纤维材料的开发和制造。合资公司的工厂位于华盛顿州的摩西湖市,西雅图以东约190mi(306km),厂房面积10,250m2,宝马为此投入了1亿美元,彰显了这家汽车制造商对进入未来轻量化车身结构市场的决心。
“我们的目标是希望接近铝合金材料的成本,目前我们还没做到。”西格里汽车公司总经理Joerg Pohlman博士解释道。“但是我们预见在未来几年内会有这么一天,在整个车身结构方面可以接近铝合金的成本。”
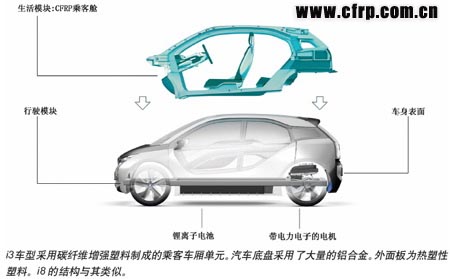
雄心勃勃的增长计划
2011年开业的位于摩西湖市的西格里公司是宝马公司第一批在整个车身结构方面都采用碳纤维材料的量产车型(i3)成功的关键,而且要采用可持续、可靠且成本效率高的加工工艺。选择这个偏远的地区是因为华盛顿州东部的干燥气候(太高的湿度不利于碳纤维生产),当然也是因为这个州在哥伦比亚河上建立的水电大坝可以提供的充足且相对廉价的“绿色”电能。

对于摩西湖的西格里公司,电力来源为40英里(64公里)外的瓦纳庞大坝。“我们每千瓦小时支付约3美分[约为美国平均电价的三分之一],在德国的瓦克斯多夫工厂都需要9美分。”Pohlman博士透露。
碳纤维生产需要消耗大量的电能,这也是碳纤维增强复合材料高成本的原因之一,而传统耗时的热压罐式生产工艺也是这家汽车制造商急切想摒弃的。摩西湖市的工厂有两条183m长的生产线,产线上的多重电加热氧化和碳化炉用于将聚丙烯腈聚合物原料的丝束,也称为原丝,转换成键合在一起的碳原子晶体。
晶体在高温、氮封环境下的平行排列使纤维具有优异的强度体积比。几千个直径为7μm的碳纤维被拉伸、清洗、缠绕、干燥、用环氧树脂涂覆并纺成像纱线一样的“长丝丝束”,缠绕在线轴上。材料会用一个“K”号码标记,即所包含的长丝(股线)数量;例如宝马最多使用的50K长丝丝束就有50,000根长丝。
重9kg(20lb)带有黑色光泽的线轴被运往宝马位于德国的瓦克斯多夫(Wackersdorf)工厂。工厂使用专利无皱褶纺织工艺将长丝丝束转化成碳纤维织物,这正是复合材料结构部件的基础。所用树脂配方也由宝马公司制定。
摩西湖市和瓦克斯多夫的工厂是宝马垂直整合的碳纤维部件生产链上的第二和第三环。生产链最初开始于另一家西格里的合资企业——位于日本大竹的三菱丽阳工厂,它生产摩西湖工厂所用的聚丙烯腈原丝。碳纤维毡在离开瓦克斯多夫工厂后,被送往宝马在德国兰茨胡特(Landshut)的工厂,这家工厂多年来专注于各种预成型、冲压及树脂转移成型的碳纤维部件的生产,包括M3和M5的大型车顶板。宝马公司预期今年将为其M系列车型生产超过100万件的碳纤维部件。
截止2012年末在i3样车中单个部件的最快生产周期“少于10分钟――但还没达到9分钟”,Pohlman博士谨慎地说。最终车身是在莱比锡(Leipzig)组装的。
“一旦两条生产线[摩西湖]在2013年中旬准备就绪,我们一年将生产约3000公吨的碳纤维——大约占全球总生产量的8%。根据行业标准,1500吨一条的产线是相当大的。目前我们还有空间可在现在的场地上再增加4条生产线,我们也可以再多购买60英亩土地。”Pohlman博士说道。
他指出除了“i系列”电动汽车外,宝马公司还将在传统内燃机驱动的汽车中增加碳纤维的使用,公司也可能向其他汽车制造商销售碳纤维。
《国际汽车工程》记者在拜访时发现工厂几乎处于“无人”的运营状态,很难发现有80名雇员的迹象——不过随着宝马i系列的产能提升,员工人数将有所增加。目前工厂为4班12小时运转,28天为一轮换周期。
汽车研究中心(Center for Automotive Research)总裁兼CEO及制造方面的专家Jay Baron博士认为碳纤维每磅12美元或者更高的市场价格,与大约2.5美元/磅的铝和1美元/磅的普通高强度钢铁相比,“就购买性而言高得离谱”。他承认这种材料有很多优势,但同时仍然对其中短期前景持怀疑态度。
“采用先进的复合材料可以把许多独立组装的金属部件融合在一起。”Baron博士解释说。“你可以在需要的地方增加强度,而在不需要的地方减少材料使用而减轻重量。如果实现了部件的整合,工厂可以小得多。你可以扔掉至少四分之三的点焊机,但却要增加粘合剂技术相关的设备,而这也不是小的投入。”
他还说,就车身和油漆车间而言,设计一个碳纤维车身结构(i3车型包括35个部件)的组装厂需要从零开始。在宝马看来,通过不断发展和改进,以及碳纤维生产的进一步自动化,这种黑色材料将最终对铝合金形成挑战。
使用碳纤维也带来了其他一些不太明显的改变。宝马公司加大碳纤维复合材料的使用也使其加入了巴伐利亚的纺织制造商贸易集团。Pohlman博士指出,这一加盟使得宝马公司的碳纤维生产基地可以利用纺织行业较低的工资水平,并加入与主导德国汽车制造商的德国金属工业工会(I.G. Metall union)完全不同的另一个工会。
OEM竞相成为碳纤维先锋
汽车行业对将碳纤维部件制造推向大批量生产的兴趣正不断提高。其他汽车制造商也逐渐加入与宝马竞争的队列中,通过战略合作关系来推动碳纤维技术的发展、降低成本、并提高产量。
日本碳纤维巨头东丽与丰田、富士重工和戴姆勒公司达成合作。而其主要的日本竞争对手帝人株式会社也与通用汽车成立了合资企业。福特和陶氏是碳纤维方面的盟友,奥迪的合作者则是西格里集团的第三大股东福伊特。去年大众汽车也入股西格里。甚至兰博基尼也和Quantum复合材料公司及卡拉威高尔夫公司(Callaway Golf)之间签订了一个三方协议。
通用汽车和普拉森碳复合材料公司(Plasan)也在进行其2014款雪佛兰Corvette C7计划,将每辆车的碳纤维车身部件含量提高到30,000-40,000单位体积的水平,这是一个重大飞跃。而去年丰田公司出人意料地与宝马公司联手,共享车辆轻量化技术信息,目前具体合作的项目依然处于保密状态中。
2013年宝马斥巨资投资于碳纤维批量生产的决定差点因为全球经济衰退而被边缘化。
“那段时期说服董事会投入碳纤维增强结构件是很难的。”Pohlman博士回忆道,他在西格里公司任职前为宝马华盛顿特区办公室的管理人员。“但是他们也承认我们必须采取大胆果断的行动,因为我们进入混合动力和电动汽车技术领域已经算是晚的了。我们此前的心态一直是,‘我们有柴油发动机’。”
所以公司开始寻找复合材料伙伴,能跟上i项目快速发展的步伐。这让宝马最终选择了西格里公司——欧洲最大的碳纤维供应商。
宝马的领先地位
宝马的工程师已经为制造汽车零件所需要的碳纤维建立了一个产品“目录”——每种碳纤维产品根据部件不同的应用会记录不同的铺层、纤维的方向和单位面积的重量等。据Pohlman博士介绍,目录的内容正在逐渐增加中。当问及目前的纤维规格时,他说在华盛顿生产的碳纤维密度为1.78 g/cm3。1250°C下的拉伸强度为4000MPa(500 ksi),弹性模量为420GPa(60,915 ksi))。
可回收性是i项目的一个重要元素。宝马开发了创新设备来帮助完成碳纤维增强复合材料加工后的回收。
“这一加工过程还生成了一种“抓绒”,它具有原材料30%-40%的工程特性,我们正在想办法加以利用,”Pohlman博士提到。宝马公司去年晚些时候宣布与波音公司合作,波音每年要使用成千上万吨的基于回收技术的碳纤维。
宝马的竞争对手“正等着我们出错,就像波音公司最早的787项目一样。”Pohlman博士认为。但是他相信公司在技术方面领先于竞争对手三年的时间,“(他们需要至少三年)才能走到我们今天的位置,零部件产量才可以达到我们所计划的数量。”
例如,与宝马现在M3车顶使用的碳纤维相比,i系列车型上用到的新材料制造费用只有其三分之一。“这是一个重大进步,”Pohlman博士说。“i3项目的目标是赚钱——而不只是通过3系来补贴。”