微脱黏法在碳纤维/环氧树脂界面性能评价中的应用
By www.carbonfiber.com.cn
微脱黏法在碳纤维/环氧树脂界面性能评价中的应用
摘要:
利用微脱黏法测定碳纤维/环氧树脂复合材料的界面剪切强度,并分析了造成测试结果分散的影响因素。结果表明:在脱黏过程中,最大脱黏力随碳纤维埋入环氧树脂内长度的增加而线性递增,当埋入长度超过一定值后最大脱黏力趋于稳定;碳纤维与环氧树脂间的接触角对复合材料界面剪切强度有一定影响,接触角越大,界面剪切强度越高;测试结果的分散性与树脂微球的半月板区域、钳口区等因素有关;未经表面处理的碳纤维增强环氧树脂复合材料的界面剪切强度仅为39.4 MPa,低于处理后的复合材料(60.6 MPa)。
在碳纤维增强树脂复合材料中,碳纤维与树脂基体间的有效黏结是复合材料具有优异性能的保证。界面黏结强度与纤维、基体的表面形态结构有关,而两者间形成的界面层也会对其产生重要影响,从而进一步影响复合材料的性能(如强度、韧性、热阻等)[1],因此,需要利用有效的表征手段测定复合材料的界面黏结强度。界面黏结强度的表征测定可以从微观和宏观两个层面上进行:微观测试是将碳纤维丝束中的一根单丝作为研究对象测定复合材料的界面剪切强度;宏观测试是先将束状碳纤维浸在树脂基体中制成预浸料、再经裁剪、模具加工成复合材料,然后利用万能材料试验机测试其层间剪切强度。
界面剪切强度高有利于应力在纤维和树脂基体间转移,复合材料力学性能好;但强度过高也极易导致复合材料韧性降低[2]。界面剪切强度最常用的测试方法有单丝拔出法[3-5]、微脱黏法[6-8]、单丝压出法[1,9-11]和单丝包埋法[12]。前三种方法中,外部载荷直接作用在单根碳纤维上,单丝包埋法中外部载荷是加载在树脂基体上。采用单丝拔出法时,对纤维埋入树脂基体内长度的要求较高,若过长,在拔出过程中纤维易断裂,因此埋入长度的高要求限制了该法的使用[13]。单丝压出法使用坚硬的金刚石压头将碳纤维从树脂中压出,在压出过程中考虑的因素较多(如残余应力、摩擦因子等)[14],存在主要问题是压出过程中在垂直于滑移方向产生的侧向力数值难以估计等[15]。单丝包埋法也称临界断裂长度法,随着作用在基体上外部载荷的逐渐增大,应力也逐步由基体转移到纤维,纤维断裂分成几段,但断裂长度达到临界长度时,确定碳纤维剪切强度困难。因此,用该法测定复合材料界面剪切强度时,基体多选用韧性材料[16]。本工作使用微脱黏法测定了碳纤维/环氧树脂复合材料的界面剪切强度,并分析了界面剪切强度测试过程的影响因素。
1·实验部分
1.1原料
聚丙烯腈基碳纤维,丝束规格为6K(即每束碳纤维中有6 000根单丝),自制;环氧树脂,WSR6101(E-44),蓝星新材料无锡树脂厂生产;三乙烯四胺,分析纯,国药集团化学试剂有限公司提供。
1.2制样及测试
在碳纤维束丝中挑选一根单丝固定黏在试样架上,然后将环氧树脂与固化剂三乙烯四胺按质量比10∶1配制树脂基体,取少量树脂基体滴在碳纤维单丝上形成微球状,在120℃下固化5 h,最后使用日本东荣产业株式会社生产的MODELHM410型复合材料界面评价装置采用微脱黏法测试固化好的碳纤维/环氧树脂。
1.3界面剪切强度测试原理
该复合材料界面评价装置的最大载荷为500mN,检测头的移动速率为0.06 mm/min。实验过程中存在以下假设:在微球脱黏过程中沿碳纤维/环氧树脂基体形成的界面方向上剪切应力不发生改变,因此,得到界面剪切强度计算公式τ=F/πDfLe。式中:τ为复合材料界面剪切强度,F为小球发生脱黏时最大载荷,Df为碳纤维直径,Le为埋入长度。
2·结果与讨论
2.1埋入长度与最大脱黏力的关系
从图1可看出:微球脱黏时,最大脱黏力与埋入长度间存在一定的线性关系。随着埋入长度的增加,所需的最大脱黏力也逐渐增大,因此,当埋入长度在一定范围内脱黏时应力状态可视为不变,但曲线不会无限地线性递增。因为当埋入长度超过一定值时,测试中纤维极易发生断裂而此时微球并未脱黏。因此存在临界埋入长度,当埋入长度大于该临界长度时,最大脱黏力随埋入长度增加不再发生变化。
埋入长度过长,纤维/环氧树脂间剪切强度超过了碳纤维单丝强度,此时碳纤维发生断裂取代微球脱黏成为主要的破坏方式;而埋入长度过低,树脂基体在碳纤维表面铺展时形成的微球直径小,上下剥离刀片形成的钳口难以夹持,测试时易滑脱。因此,使用微脱黏法测界面剪切强度时,选取测试微球的埋入长度宜控制在40~80μm。利用微脱黏法测得的碳纤维/环氧树脂复合材料界面剪切强度均值为60.6 MPa,测试中理想的脱黏状态为树脂微球沿纤维/环氧树脂界面方向只发生位置移动(见图2)。
2.2埋入长度与接触角的关系
碳纤维/环氧树脂基体间的接触角反映了环氧树脂基体对碳纤维润湿能力的大小。由于接触角与微球高度、埋入长度相关,因此,它主观上反映了碳纤维/环氧树脂间形成微球的形态结构。从图3看出:接触角主要分布在40°~60°。通过研究埋入长度与接触角的关系发现:埋入长度不同,碳纤维/环氧树脂间接触角大小也有所不同;当接触角介于40°~50°时,复合材料的界面剪切强度为50.0 MPa左右;当接触角介于50°~60°时,界面剪切强度为60.0 MPa左右。因此,随着接触角的增加,界面剪切强度呈现不断增大的现象。
2.3界面剪切强度的影响因素
利用微脱黏法测得复合材料的界面剪切强度数值具有较大的分散性,这与纤维表面形成树脂微球的半月板区域、脱黏过程中上下刀片形成的钳口及碳纤维表面形态结构等因素有关。
2.3.1树脂微球的半月板区域
由于碳纤维为固相,环氧树脂基体为液相,在两者表面张力作用下会在界面形成半月板区域(模型见图4)。
半月板区域的存在将直接导致界面剪切强度测试结果分散性提高,且树脂微球脱黏时会有部分基体残留在碳纤维表面。其主要原因在于半月板区域影响了测试时钳口的位置,在外部载荷下钳口对微球剥离时,半月板区域的弧面易使钳口发生位置移动,从而使微球不在起始点发生脱黏,造成了脱黏后的部分基体残留(见图5)。综上可知,微球半月板区域越小、微球的圆形度越高,上下刀口位置越易确定,从而有利于微球的理想脱黏。
2.3.2钳口区
在微脱黏测试中上下刀片形成钳口区,在钳口的剥离作用下树脂微球发生剪切破坏,而钳口位置、钳口间距、钳角等均会对界面剪切强度产生一定影响。首先,钳口位置决定了基体发生断裂的位置,由于钳口位置难于控制,每次测量时也不可能保证其位置相同,因此造成测试数据具有一定分散性;其次,钳口间距过短,夹距也较短,测试时易造成纤维的断裂,而间距过大会造成测试时微球的滑脱,得不到有效数据;最后,钳角会影响碳纤维表面的应力分布状态,进而会对界面剪切强度产生一定影响。
2.3.3碳纤维的表面形态结构
经高温预氧化、碳化工艺制备的碳纤维,随着非碳元素的逸出和碳纤维的富集,纤维表面呈惰性,因此需经表面处理增加其表面活性。碳纤维经表面处理后会引入大量—OH,—COOH等活性官能团,碳纤维表面的沟槽也加深加宽,从而有利于碳纤维与树脂基体间的化学键合和物理锚定作用。从图6看出:表面处理后碳纤维表面沟槽加深加宽。表面处理前碳纤维/环氧树脂复合材料的界面剪切强度仅39.4 MPa,而碳纤维经表面处理后复合材料的界面剪切强度增至60.6 MPa,说明表面处理工艺有利于提高复合材料界面剪切强度。
3·结论
a)在利用微脱黏法测试碳纤维/环氧树脂复合材料界面剪切强度时,纤维埋入长度与最大脱黏力之间存在线性关系。
b)碳纤维与环氧树脂基体间接触角的大小随埋入长度的不同而存在差异,接触角对界面剪切强度也有一定的影响,接触角越大,界面剪切强度也越大。
c)在微脱黏实验中,树脂微球的半月板区域、钳口的位置及间距、钳角大小等影响测试结果,造成了界面剪切强度数据具有一定分散性。
d)经过表面处理的碳纤维,其表面形态结构变化较大,而碳纤维/环氧树脂复合材料的界面剪切强度也由处理前的39.4 MPa增大到处理后的60.6 MPa。
钱鑫,王雪飞,欧阳琴,陈友汜
(中国科学院宁波材料技术与工程研究所,碳纤维制备技术国家工程实验室)
微脱黏法在碳纤维/环氧树脂界面性能评价中的应用
摘要:
利用微脱黏法测定碳纤维/环氧树脂复合材料的界面剪切强度,并分析了造成测试结果分散的影响因素。结果表明:在脱黏过程中,最大脱黏力随碳纤维埋入环氧树脂内长度的增加而线性递增,当埋入长度超过一定值后最大脱黏力趋于稳定;碳纤维与环氧树脂间的接触角对复合材料界面剪切强度有一定影响,接触角越大,界面剪切强度越高;测试结果的分散性与树脂微球的半月板区域、钳口区等因素有关;未经表面处理的碳纤维增强环氧树脂复合材料的界面剪切强度仅为39.4 MPa,低于处理后的复合材料(60.6 MPa)。
在碳纤维增强树脂复合材料中,碳纤维与树脂基体间的有效黏结是复合材料具有优异性能的保证。界面黏结强度与纤维、基体的表面形态结构有关,而两者间形成的界面层也会对其产生重要影响,从而进一步影响复合材料的性能(如强度、韧性、热阻等)[1],因此,需要利用有效的表征手段测定复合材料的界面黏结强度。界面黏结强度的表征测定可以从微观和宏观两个层面上进行:微观测试是将碳纤维丝束中的一根单丝作为研究对象测定复合材料的界面剪切强度;宏观测试是先将束状碳纤维浸在树脂基体中制成预浸料、再经裁剪、模具加工成复合材料,然后利用万能材料试验机测试其层间剪切强度。
界面剪切强度高有利于应力在纤维和树脂基体间转移,复合材料力学性能好;但强度过高也极易导致复合材料韧性降低[2]。界面剪切强度最常用的测试方法有单丝拔出法[3-5]、微脱黏法[6-8]、单丝压出法[1,9-11]和单丝包埋法[12]。前三种方法中,外部载荷直接作用在单根碳纤维上,单丝包埋法中外部载荷是加载在树脂基体上。采用单丝拔出法时,对纤维埋入树脂基体内长度的要求较高,若过长,在拔出过程中纤维易断裂,因此埋入长度的高要求限制了该法的使用[13]。单丝压出法使用坚硬的金刚石压头将碳纤维从树脂中压出,在压出过程中考虑的因素较多(如残余应力、摩擦因子等)[14],存在主要问题是压出过程中在垂直于滑移方向产生的侧向力数值难以估计等[15]。单丝包埋法也称临界断裂长度法,随着作用在基体上外部载荷的逐渐增大,应力也逐步由基体转移到纤维,纤维断裂分成几段,但断裂长度达到临界长度时,确定碳纤维剪切强度困难。因此,用该法测定复合材料界面剪切强度时,基体多选用韧性材料[16]。本工作使用微脱黏法测定了碳纤维/环氧树脂复合材料的界面剪切强度,并分析了界面剪切强度测试过程的影响因素。
1·实验部分
1.1原料
聚丙烯腈基碳纤维,丝束规格为6K(即每束碳纤维中有6 000根单丝),自制;环氧树脂,WSR6101(E-44),蓝星新材料无锡树脂厂生产;三乙烯四胺,分析纯,国药集团化学试剂有限公司提供。
1.2制样及测试
在碳纤维束丝中挑选一根单丝固定黏在试样架上,然后将环氧树脂与固化剂三乙烯四胺按质量比10∶1配制树脂基体,取少量树脂基体滴在碳纤维单丝上形成微球状,在120℃下固化5 h,最后使用日本东荣产业株式会社生产的MODELHM410型复合材料界面评价装置采用微脱黏法测试固化好的碳纤维/环氧树脂。
1.3界面剪切强度测试原理
该复合材料界面评价装置的最大载荷为500mN,检测头的移动速率为0.06 mm/min。实验过程中存在以下假设:在微球脱黏过程中沿碳纤维/环氧树脂基体形成的界面方向上剪切应力不发生改变,因此,得到界面剪切强度计算公式τ=F/πDfLe。式中:τ为复合材料界面剪切强度,F为小球发生脱黏时最大载荷,Df为碳纤维直径,Le为埋入长度。
2·结果与讨论
2.1埋入长度与最大脱黏力的关系
从图1可看出:微球脱黏时,最大脱黏力与埋入长度间存在一定的线性关系。随着埋入长度的增加,所需的最大脱黏力也逐渐增大,因此,当埋入长度在一定范围内脱黏时应力状态可视为不变,但曲线不会无限地线性递增。因为当埋入长度超过一定值时,测试中纤维极易发生断裂而此时微球并未脱黏。因此存在临界埋入长度,当埋入长度大于该临界长度时,最大脱黏力随埋入长度增加不再发生变化。

埋入长度过长,纤维/环氧树脂间剪切强度超过了碳纤维单丝强度,此时碳纤维发生断裂取代微球脱黏成为主要的破坏方式;而埋入长度过低,树脂基体在碳纤维表面铺展时形成的微球直径小,上下剥离刀片形成的钳口难以夹持,测试时易滑脱。因此,使用微脱黏法测界面剪切强度时,选取测试微球的埋入长度宜控制在40~80μm。利用微脱黏法测得的碳纤维/环氧树脂复合材料界面剪切强度均值为60.6 MPa,测试中理想的脱黏状态为树脂微球沿纤维/环氧树脂界面方向只发生位置移动(见图2)。

2.2埋入长度与接触角的关系
碳纤维/环氧树脂基体间的接触角反映了环氧树脂基体对碳纤维润湿能力的大小。由于接触角与微球高度、埋入长度相关,因此,它主观上反映了碳纤维/环氧树脂间形成微球的形态结构。从图3看出:接触角主要分布在40°~60°。通过研究埋入长度与接触角的关系发现:埋入长度不同,碳纤维/环氧树脂间接触角大小也有所不同;当接触角介于40°~50°时,复合材料的界面剪切强度为50.0 MPa左右;当接触角介于50°~60°时,界面剪切强度为60.0 MPa左右。因此,随着接触角的增加,界面剪切强度呈现不断增大的现象。

2.3界面剪切强度的影响因素
利用微脱黏法测得复合材料的界面剪切强度数值具有较大的分散性,这与纤维表面形成树脂微球的半月板区域、脱黏过程中上下刀片形成的钳口及碳纤维表面形态结构等因素有关。
2.3.1树脂微球的半月板区域
由于碳纤维为固相,环氧树脂基体为液相,在两者表面张力作用下会在界面形成半月板区域(模型见图4)。
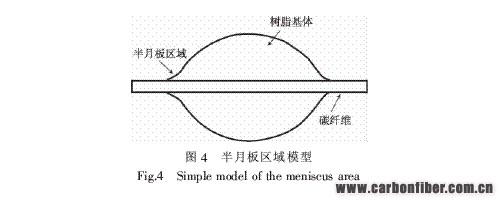
半月板区域的存在将直接导致界面剪切强度测试结果分散性提高,且树脂微球脱黏时会有部分基体残留在碳纤维表面。其主要原因在于半月板区域影响了测试时钳口的位置,在外部载荷下钳口对微球剥离时,半月板区域的弧面易使钳口发生位置移动,从而使微球不在起始点发生脱黏,造成了脱黏后的部分基体残留(见图5)。综上可知,微球半月板区域越小、微球的圆形度越高,上下刀口位置越易确定,从而有利于微球的理想脱黏。

2.3.2钳口区
在微脱黏测试中上下刀片形成钳口区,在钳口的剥离作用下树脂微球发生剪切破坏,而钳口位置、钳口间距、钳角等均会对界面剪切强度产生一定影响。首先,钳口位置决定了基体发生断裂的位置,由于钳口位置难于控制,每次测量时也不可能保证其位置相同,因此造成测试数据具有一定分散性;其次,钳口间距过短,夹距也较短,测试时易造成纤维的断裂,而间距过大会造成测试时微球的滑脱,得不到有效数据;最后,钳角会影响碳纤维表面的应力分布状态,进而会对界面剪切强度产生一定影响。
2.3.3碳纤维的表面形态结构
经高温预氧化、碳化工艺制备的碳纤维,随着非碳元素的逸出和碳纤维的富集,纤维表面呈惰性,因此需经表面处理增加其表面活性。碳纤维经表面处理后会引入大量—OH,—COOH等活性官能团,碳纤维表面的沟槽也加深加宽,从而有利于碳纤维与树脂基体间的化学键合和物理锚定作用。从图6看出:表面处理后碳纤维表面沟槽加深加宽。表面处理前碳纤维/环氧树脂复合材料的界面剪切强度仅39.4 MPa,而碳纤维经表面处理后复合材料的界面剪切强度增至60.6 MPa,说明表面处理工艺有利于提高复合材料界面剪切强度。

3·结论
a)在利用微脱黏法测试碳纤维/环氧树脂复合材料界面剪切强度时,纤维埋入长度与最大脱黏力之间存在线性关系。
b)碳纤维与环氧树脂基体间接触角的大小随埋入长度的不同而存在差异,接触角对界面剪切强度也有一定的影响,接触角越大,界面剪切强度也越大。
c)在微脱黏实验中,树脂微球的半月板区域、钳口的位置及间距、钳角大小等影响测试结果,造成了界面剪切强度数据具有一定分散性。
d)经过表面处理的碳纤维,其表面形态结构变化较大,而碳纤维/环氧树脂复合材料的界面剪切强度也由处理前的39.4 MPa增大到处理后的60.6 MPa。
钱鑫,王雪飞,欧阳琴,陈友汜
(中国科学院宁波材料技术与工程研究所,碳纤维制备技术国家工程实验室)