被编织出来的汽车-宝马i3纯电动车
By www.carbonfiber.com.cn
BMW i3,可谓第一款“编织”出来的汽车。BMW i3碳纤维增强复合材料的车身,是以基于聚丙烯腈的热塑性纺织纤维为原材料,在一定的压力和温度下,转化成极其细长的碳纤维丝线,最后再经过相应的氧化和碳化处理,形成车身材料。这个复杂的多阶段工艺中纤维的各种构成要素会通过气化被逐一剔除,最终只留下几乎纯碳组成、具有稳定的石墨结构仅0.007毫米的纤维直径相当于人类头发直径的十分之一。碳纤维强化塑料(CFRP)的使用将从根本上改变汽车行业。

这些材料最初是以线束的形式存在,根据需要纺织成各种各样的结构和样式,接下来被送往碳纤维增强复合材料裁剪车间,完成相应部件的碳纤维软性板材预成型。随后,被切割成各种不同大小和形状的碳纤维板材,通过高温高压的复合树脂注射技术,让碳纤维复合材料最终成型,最终再通过先进的粘合等技术将个碳纤维车身部件结合成整体车身,这种技术把零部件的总数降低到传统钢制车身使用总量的三分之一。同时,BMW i3的材质选择使得其制造过程颠覆了传统汽车生产过程中的钢板冲压工艺,革命性的改变了汽车的生产流程。
BMW i3在内饰选材上,最大程度地选用可持续材料,包括天然加工而成的皮革、木材、羊毛制品以及可再生回收原材料。其中,浅色木纹饰板的桉木出自BMW集团指定的欧洲桉树种植园。除了桉木饰板以外,BMW i3车厢内的皮革也只使用天然产品处理,鞣制剂是从橄榄树叶中提取的天然原汁。仪表板架和车门饰件由洋麻植物纤维制成,表面经过严格的技术处理,形成独特的视觉和触觉感受。另外,车厢内部25%重量的塑料都来自于可再生原材料。
在过去的十多年时间里,宝马公司一直致力于碳纤维复合材料产品和创新技术的研发,工程师们不断降低产品生产周期以及原材料成本。目前,宝马集团已经成为唯一能够批量生产碳纤维复合材料的汽车制造商。
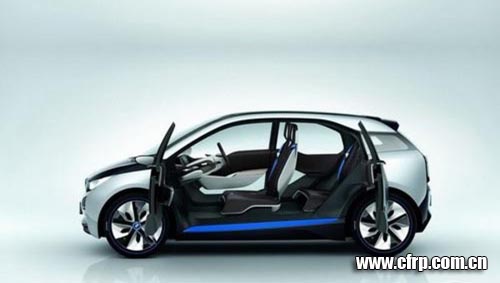
BMW i3,可谓第一款“编织”出来的汽车。BMW i3碳纤维增强复合材料的车身,是以基于聚丙烯腈的热塑性纺织纤维为原材料,在一定的压力和温度下,转化成极其细长的碳纤维丝线,最后再经过相应的氧化和碳化处理,形成车身材料。这个复杂的多阶段工艺中纤维的各种构成要素会通过气化被逐一剔除,最终只留下几乎纯碳组成、具有稳定的石墨结构仅0.007毫米的纤维直径相当于人类头发直径的十分之一。碳纤维强化塑料(CFRP)的使用将从根本上改变汽车行业。


这些材料最初是以线束的形式存在,根据需要纺织成各种各样的结构和样式,接下来被送往碳纤维增强复合材料裁剪车间,完成相应部件的碳纤维软性板材预成型。随后,被切割成各种不同大小和形状的碳纤维板材,通过高温高压的复合树脂注射技术,让碳纤维复合材料最终成型,最终再通过先进的粘合等技术将个碳纤维车身部件结合成整体车身,这种技术把零部件的总数降低到传统钢制车身使用总量的三分之一。同时,BMW i3的材质选择使得其制造过程颠覆了传统汽车生产过程中的钢板冲压工艺,革命性的改变了汽车的生产流程。



BMW i3在内饰选材上,最大程度地选用可持续材料,包括天然加工而成的皮革、木材、羊毛制品以及可再生回收原材料。其中,浅色木纹饰板的桉木出自BMW集团指定的欧洲桉树种植园。除了桉木饰板以外,BMW i3车厢内的皮革也只使用天然产品处理,鞣制剂是从橄榄树叶中提取的天然原汁。仪表板架和车门饰件由洋麻植物纤维制成,表面经过严格的技术处理,形成独特的视觉和触觉感受。另外,车厢内部25%重量的塑料都来自于可再生原材料。


在过去的十多年时间里,宝马公司一直致力于碳纤维复合材料产品和创新技术的研发,工程师们不断降低产品生产周期以及原材料成本。目前,宝马集团已经成为唯一能够批量生产碳纤维复合材料的汽车制造商。