复合材料增韧:从新概念到高技术产品
By www.carbonfiber.com.cn
图1,第一代、第二代和第三代航空复合材料的压缩强度与冲击后压缩强度的关系
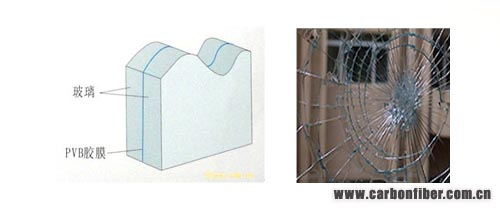
图2,层状化、含柔性高分子夹层材料的防弹、防撞击玻璃制品举例
图3,反应诱导相分离及粗化形成的颗粒状双连续结构示意(上左),热塑性脂增韧的环氧树脂双连续结构示意(上右),以及热塑性树脂增韧的双马来酰亚胺树脂双连续结构示意(下)的扫描显微镜照片

图4,环氧树与脂基复合材料的碳纤维铺层间的结构形貌
图5,富热塑性的颗粒状3-3层间结构向碳纤维层内的浅层扩散示意
图6,“离位”核心技术体系与材料体系
持续提高复合材料的性能是航空复合材料基础研究一个永恒的主题,一如“更高、更快、更强”的奥运会精神。几年前,空中客车公司就飞机复合材料技术的现状和发展方向指出,未来航空复合材料应该具有更高的韧性性质,体现在连续碳纤维增强的航空树脂基复合材料上,就是这些材料必须具备更高的压缩强度和冲击后压缩强度(CAI,Compression After Impact,图1),这样才能保证飞机的安全性。复合材料的压缩强度主要由碳纤维的性能决定,而复合材料的CAI性质则取决于树脂材料的韧性,特别是复合材料的多尺度、多层次结构等。
事实上,寸有所长,尺有所短,没有一种材料是“全才”,也没有一种材料是只有优点而没有弱点的。从总体上看,碳纤维增强材料作为航空复合材料产生优秀力学性能的基础,它本身的韧性就很低,导致用碳纤维增强的树脂基复合材料的韧性水平相对于许多金属材料也偏低,因此,提升结构材料、特别是先进的碳纤维增强树脂基复合材料的韧性性能当然也是航空复合材料领域永恒的研究主题。
增韧新概念的提出与实践
众所周知,玻璃易碎,但夹层防弹玻璃或车窗玻璃却不怕。为什么?就是因为在这些层状化“复合材料”的设计里,在两张薄玻璃层之间设置了一层柔性高分子的插层(如PVC胶膜),并保证两者之间良好黏结,这样,在弹击或撞击事件发生时,夹层玻璃一般不会发生粉碎性、穿透性的灾难性破坏(图2)。显然,夹层玻璃设计没有改变玻璃脆性的本质,但通过层间插入改变了整个系统对外部冲击的响应机制和破坏模式,因此就不怎么害怕冲击破坏了。
为了提升我国航空复合材料的韧性性质,特别是提高航空复合材料的冲击后压缩性质,在国家“973计划”项目等的支持下,北京航空材料研究院先进复合材料国防科技重点实验室的材料科学家提出了复合材料层间增韧和层内增刚的新概念,在2000年前后,在“离位”层间增韧方面,初步实现在保持复合材料比刚度和比强度的同时,大幅度提高复合材料的冲击分层损伤阻抗与容限,这其中,一个关键的概念就是“离位”层间增韧技术,这个技术的形象的理解可以比照夹层防弹玻璃:为了提高比较脆性的热固性复合材料的冲击损伤阻抗,可以在连续碳纤维的铺层之间放置高韧性的热塑性树脂铺层。
实践是检验真理的标准。通过国产双马来酰亚胺树脂基复合材料各3个试样“离位”层间增韧前后的冲击分层损伤超声波C扫描照片、冲击分层损伤的投影面积以及相应的冲击后压缩强度(CAI值)的对比,比较发现,“离位”层间增韧不仅提高了复合材料抗击冲击分层的能力(冲击损伤阻抗),减少了的分层投影面积,而且也提高了复合材料的冲击后剩余压缩强度(冲击损伤容限)。
同样,国产聚酰亚胺复合材料的研究和测试结果也表明,“离位”增韧方面也有力地提升了这种高温复合材料的冲击分层损伤阻抗和损伤容限,复合材料的CAI值提升显著。对国内外其他复合材料例如环氧树脂基以及聚苯并恶嗪基复合材料冲击损伤阻抗和损伤容限的研究与测试结果证实,“离位”层间增韧技术在合适的材料热力学和动力学条件下,均可以取得比较明显的复合材料增韧改性效果。
“离位”增韧的材料科学基础
基复合材料冲击损伤阻抗和损伤容限得到提高的材料学机制是什么呢?现代材料科学告诉我们,决定材料使用性能的关键不仅取决于组成这个材料体系的成分,而且取决于这个材料体系内部的多尺度、多层次的微结构,因此,根据“离位”层间增韧在连续碳纤维的铺层之间放置高韧性的热塑性树脂铺层是一回事,而得到什么样的材料微结构是另一回事。大量的基础研究工作表明,双连续、颗粒化的微观结构将有利于提高材料的冲击韧性(图3),因为在这种结构里,裂纹的引发及其扩展必须穿越大量颗粒以及颗粒间的高韧性的“填充”材料,从而引起大量的能量消耗,换句话说,这样的微结构是一种高韧化的微结构。根据这个思路,重点实验室的科研人员通过材料热力学和动力学的研究,研制获得了这种双连续、颗粒化的热塑性高分子/热固性高分子复相微观结构,选用的树脂材料对象就是我国航空工业的主要复合材料品种。
需要指出,“离位”增韧技术的第二个条件是“定域”,就是说,必须把这种双连续、颗粒化的微观结构准确地放置在层状复合材料的富树脂的层间,并且尽可能地控制层间厚度,以保证复合材料在高增强纤维体积分数条件下的比刚度和比强度。图4所示是一个国产高温环氧树脂基复合材料的碳纤维铺层间的微结构形貌,照片中,特征性的双连续、颗粒状的环氧树脂颗粒连成了一片,层间厚度约相当于2~3根碳纤维的直径。同时我们还可以看到,这种双连续的颗粒微结构已经浅层渗透进入了碳纤维铺层内约几根碳纤维直径的深度,其后,基体树脂仍旧保持为环氧连续相。事实上,正是因为这个浅层渗透的双连续颗粒结构产生了一种“机械”咬合作用,特别是在断裂尖端张开载荷的条件下,
这种咬合将产生“犁地”效应,在裂纹扩展时引发大量纤维的拔出和断裂,导致裂纹扩展或分层的阻力成倍地增长。
根据以上的观测结果,可以初步建立一个“离位”复合材料的层结构模型(图5),初始被表面附载而预置在碳纤维铺层间的热塑性树脂层经过热固性树脂的扩散、交联固化,特别是经过相分离、相反转和相粗化等一系列热力学和动力学过程,形成为一个跨层间的独特的热固性树脂连续结构,其形貌特征是连续的颗粒结构,与此同时,热塑性树脂也是连续地分布在热固性树脂颗粒之间,即“双连续”。特别是这种双连续结构的边界并不是两个碳纤维铺层的层间,而是浅层渗透进入了碳纤维铺层的层内,从而产生机械互锁效应。
概念性研究成果的工程化放大
为了将这个基础研究的成果推向工业应用,在中航工业创新基金项目等的财政支持下,重点实验室的科研人员在热熔预浸机上把“离位”表面附载技术进行了连续化放大试验,结果令人满意。由此获得的预浸料产品命名为ESTM-Prepreg预浸料,北京航空材料研究院获得这个产品的注册商标。
“离位”表面附载增韧技术的提出和发展主要得益于深入的基础研究,图6所示就是“离位”增韧概念研究的全流程,由此可见,基础研究当然需要长期的投入,但更需要在长期财政支持和基础理论指导下开展认认真真的探索,北京航空材料研究院先进复合材料国防科技重点实验室的材料科学家和材料技术工程师们正是这样实践的。(作者单位为中航工业北京航空材料研究院)

图1,第一代、第二代和第三代航空复合材料的压缩强度与冲击后压缩强度的关系
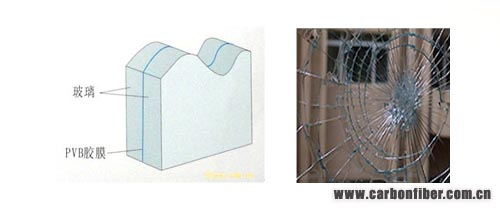
图2,层状化、含柔性高分子夹层材料的防弹、防撞击玻璃制品举例

图3,反应诱导相分离及粗化形成的颗粒状双连续结构示意(上左),热塑性脂增韧的环氧树脂双连续结构示意(上右),以及热塑性树脂增韧的双马来酰亚胺树脂双连续结构示意(下)的扫描显微镜照片

图4,环氧树与脂基复合材料的碳纤维铺层间的结构形貌
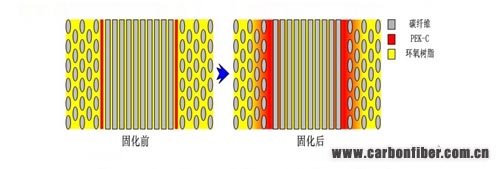
图5,富热塑性的颗粒状3-3层间结构向碳纤维层内的浅层扩散示意
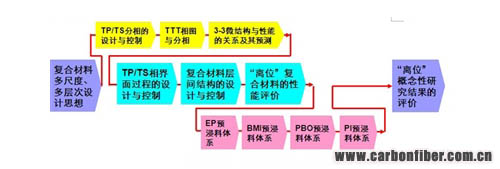
图6,“离位”核心技术体系与材料体系
持续提高复合材料的性能是航空复合材料基础研究一个永恒的主题,一如“更高、更快、更强”的奥运会精神。几年前,空中客车公司就飞机复合材料技术的现状和发展方向指出,未来航空复合材料应该具有更高的韧性性质,体现在连续碳纤维增强的航空树脂基复合材料上,就是这些材料必须具备更高的压缩强度和冲击后压缩强度(CAI,Compression After Impact,图1),这样才能保证飞机的安全性。复合材料的压缩强度主要由碳纤维的性能决定,而复合材料的CAI性质则取决于树脂材料的韧性,特别是复合材料的多尺度、多层次结构等。
事实上,寸有所长,尺有所短,没有一种材料是“全才”,也没有一种材料是只有优点而没有弱点的。从总体上看,碳纤维增强材料作为航空复合材料产生优秀力学性能的基础,它本身的韧性就很低,导致用碳纤维增强的树脂基复合材料的韧性水平相对于许多金属材料也偏低,因此,提升结构材料、特别是先进的碳纤维增强树脂基复合材料的韧性性能当然也是航空复合材料领域永恒的研究主题。
增韧新概念的提出与实践
众所周知,玻璃易碎,但夹层防弹玻璃或车窗玻璃却不怕。为什么?就是因为在这些层状化“复合材料”的设计里,在两张薄玻璃层之间设置了一层柔性高分子的插层(如PVC胶膜),并保证两者之间良好黏结,这样,在弹击或撞击事件发生时,夹层玻璃一般不会发生粉碎性、穿透性的灾难性破坏(图2)。显然,夹层玻璃设计没有改变玻璃脆性的本质,但通过层间插入改变了整个系统对外部冲击的响应机制和破坏模式,因此就不怎么害怕冲击破坏了。
为了提升我国航空复合材料的韧性性质,特别是提高航空复合材料的冲击后压缩性质,在国家“973计划”项目等的支持下,北京航空材料研究院先进复合材料国防科技重点实验室的材料科学家提出了复合材料层间增韧和层内增刚的新概念,在2000年前后,在“离位”层间增韧方面,初步实现在保持复合材料比刚度和比强度的同时,大幅度提高复合材料的冲击分层损伤阻抗与容限,这其中,一个关键的概念就是“离位”层间增韧技术,这个技术的形象的理解可以比照夹层防弹玻璃:为了提高比较脆性的热固性复合材料的冲击损伤阻抗,可以在连续碳纤维的铺层之间放置高韧性的热塑性树脂铺层。
实践是检验真理的标准。通过国产双马来酰亚胺树脂基复合材料各3个试样“离位”层间增韧前后的冲击分层损伤超声波C扫描照片、冲击分层损伤的投影面积以及相应的冲击后压缩强度(CAI值)的对比,比较发现,“离位”层间增韧不仅提高了复合材料抗击冲击分层的能力(冲击损伤阻抗),减少了的分层投影面积,而且也提高了复合材料的冲击后剩余压缩强度(冲击损伤容限)。
同样,国产聚酰亚胺复合材料的研究和测试结果也表明,“离位”增韧方面也有力地提升了这种高温复合材料的冲击分层损伤阻抗和损伤容限,复合材料的CAI值提升显著。对国内外其他复合材料例如环氧树脂基以及聚苯并恶嗪基复合材料冲击损伤阻抗和损伤容限的研究与测试结果证实,“离位”层间增韧技术在合适的材料热力学和动力学条件下,均可以取得比较明显的复合材料增韧改性效果。
“离位”增韧的材料科学基础
基复合材料冲击损伤阻抗和损伤容限得到提高的材料学机制是什么呢?现代材料科学告诉我们,决定材料使用性能的关键不仅取决于组成这个材料体系的成分,而且取决于这个材料体系内部的多尺度、多层次的微结构,因此,根据“离位”层间增韧在连续碳纤维的铺层之间放置高韧性的热塑性树脂铺层是一回事,而得到什么样的材料微结构是另一回事。大量的基础研究工作表明,双连续、颗粒化的微观结构将有利于提高材料的冲击韧性(图3),因为在这种结构里,裂纹的引发及其扩展必须穿越大量颗粒以及颗粒间的高韧性的“填充”材料,从而引起大量的能量消耗,换句话说,这样的微结构是一种高韧化的微结构。根据这个思路,重点实验室的科研人员通过材料热力学和动力学的研究,研制获得了这种双连续、颗粒化的热塑性高分子/热固性高分子复相微观结构,选用的树脂材料对象就是我国航空工业的主要复合材料品种。
需要指出,“离位”增韧技术的第二个条件是“定域”,就是说,必须把这种双连续、颗粒化的微观结构准确地放置在层状复合材料的富树脂的层间,并且尽可能地控制层间厚度,以保证复合材料在高增强纤维体积分数条件下的比刚度和比强度。图4所示是一个国产高温环氧树脂基复合材料的碳纤维铺层间的微结构形貌,照片中,特征性的双连续、颗粒状的环氧树脂颗粒连成了一片,层间厚度约相当于2~3根碳纤维的直径。同时我们还可以看到,这种双连续的颗粒微结构已经浅层渗透进入了碳纤维铺层内约几根碳纤维直径的深度,其后,基体树脂仍旧保持为环氧连续相。事实上,正是因为这个浅层渗透的双连续颗粒结构产生了一种“机械”咬合作用,特别是在断裂尖端张开载荷的条件下,
这种咬合将产生“犁地”效应,在裂纹扩展时引发大量纤维的拔出和断裂,导致裂纹扩展或分层的阻力成倍地增长。
根据以上的观测结果,可以初步建立一个“离位”复合材料的层结构模型(图5),初始被表面附载而预置在碳纤维铺层间的热塑性树脂层经过热固性树脂的扩散、交联固化,特别是经过相分离、相反转和相粗化等一系列热力学和动力学过程,形成为一个跨层间的独特的热固性树脂连续结构,其形貌特征是连续的颗粒结构,与此同时,热塑性树脂也是连续地分布在热固性树脂颗粒之间,即“双连续”。特别是这种双连续结构的边界并不是两个碳纤维铺层的层间,而是浅层渗透进入了碳纤维铺层的层内,从而产生机械互锁效应。
概念性研究成果的工程化放大
为了将这个基础研究的成果推向工业应用,在中航工业创新基金项目等的财政支持下,重点实验室的科研人员在热熔预浸机上把“离位”表面附载技术进行了连续化放大试验,结果令人满意。由此获得的预浸料产品命名为ESTM-Prepreg预浸料,北京航空材料研究院获得这个产品的注册商标。
“离位”表面附载增韧技术的提出和发展主要得益于深入的基础研究,图6所示就是“离位”增韧概念研究的全流程,由此可见,基础研究当然需要长期的投入,但更需要在长期财政支持和基础理论指导下开展认认真真的探索,北京航空材料研究院先进复合材料国防科技重点实验室的材料科学家和材料技术工程师们正是这样实践的。(作者单位为中航工业北京航空材料研究院)