FiberSIM在复合材料部件数字化设计制造中的应用
By www.cfrp.com.cn
飞机换代最突出的体现就是对飞机性能要求的不断提高,包括减轻结构重量,降低巡航阻力,增大航程;减少结构疲劳损坏,延长使用寿命;降低制造成本和维护费用。这些要求决定了飞机减重的迫切性,使航空部件材料和结构的选择成为提高飞机性能的关键因素。
碳纤维复合材料具有比强度大、比刚度高、抗疲劳性能好、各向异性以及材料性能可设计的特点,应用于航空领域中,可以获得显著的减重效益,并改善结构性能。目前,复合材料技术已成为影响飞机发展的关键技术之一,逐渐应用于飞机结构的主承力构件中,可达到减重20%~30%的效果。因此,它在航空航天领域的应用日益广泛,已迅速发展成为包括铝、钢、钛在内的四大航空航天结构材料之一。
除减重外,复合材料还具有更好的耐久性,可降低使用维护成本。在人类有动力飞行进入第二个百年之后,复合材料开始“领跑”飞机设计技术,成为“航空航天结构的未来”。
碳纤维复合材料设计制造技术的发展
传统复合材料设计和制造过程是分别进行的。对于复杂的结构,通常较难确定满足铺层边界要求的准确平面展开图样,为避免材料的扭曲变形,需要在制造车间大量地反复试验修改,造成了贵重材料的浪费和大量的车间返工;同时将碳纤维铺放在一起需花费大量时间(铺完一个机翼壁板铺层大约需要90~120min),这在一定程度上反映了制造机翼这样的大型零件所要面临的挑战。
现在,这些问题由于采用了新的复合材料设计制造关键技术而得以解决。
(1)设计与制造一体化技术。
随着计算机和制造技术的进步,复合材料设计制造技术可采用全新的设计理念和手段,将设计和制造融为一体,将程序化的软件用于生产制造中,使制造中的问题在设计初期阶段就能加以考虑,从而加快产品研制进度,提高质量,降低成本。
(2)大面积整体成形技术。
以共固化/共胶接(cocured/cobonded)和无紧固件(fastenerless)为核心的整体成形技术,采用大面积整体成形,少用或不用紧固件,减少了零件数目,减轻了重量,降低了连接、装配和制造的成本。
(3)低成本的制造技术。
先进复合材料自60年代中期问世以来,在军用、民用领域的应用均得到飞速的发展。但复合材料的成本,特别是制造成本较高,成为复合材料进一步应用推广的主要障碍之一。该问题已引起世界各国的普遍重视,特别是以美国为首的西方发达国家纷纷制定低成本的复合材料发展研究计划,努力实践,并已取得较大进展。目前,低成本复合材料技术已成为全世界复合材料发展研究领域的一个核心课题。
复合材料制造成本约占复合材料成本的80%~85%,所以低成本复合材料技术中关键是低成本的制造技术。采用复合材料数字化设计制造技术,能最大限度地节省时间和劳动力,速度较手工提高了10倍;同时能节省原材料,提高制件精度和质量,从而降低了制造成本。
Fibersim复合材料设计制造软件
fibersim是一个可以实现复合材料数字化设计制造一体化的软件,它与cad软件紧密集成,实现了设计和分析自动化,生成制造工程信息和驱动激光投影仪、自动切割机、纤维铺放设备的数据,覆盖复合材料整个工艺设计过程,为复合材料的设计和制造提供全面的解决方案,适应了复合材料设计制造技术的发展要求。
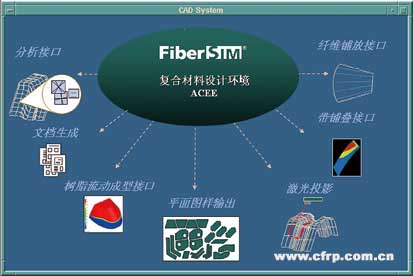
fibersim设计制造一体化环境
fibersim软件已成功用于商用和军用飞机的设计,能够完成复合材料部件的可制造性评估,精确模拟纤维的材料特性,生成平面展开图样,完成复合材料部件的分析、设计和制造,对层合板进行验证。将三维几何模型与层合板的设计联系起来,并将层合板的设计信息与有限元分析软件和制造设备形成无缝连接,可实现制造过程自动化,降低制造成本。
fibersim在飞机复合材料部件数字化设计制造中的应用
复合材料的性能很好地满足了当代新型飞机的相应需求。在美国先进联合攻击战斗机jsf的研制中,波音和洛克希德·马丁公司都分别使用了大量的复合材料构件,对这两家公司都是一大挑战。他们引进了fibersim软件,采用新的技术手段,利用先进的数字化设计制造技术满足联合攻击战斗机(jsf)苛刻的强度要求、成本目标和重量标准,克服了传统复合材料设计制造中的困难,充分体现了新世纪复合材料构件低成本技术的发展水平。
1 在x-32样机研制中的应用
从应用领域来看,碳纤维复合材料主要用于航空航天等领域,波音公司在制造联合攻击战斗机样机x-32的很多大型部件时,就设计采用了单向碳纤维复合材料。并选用了fibersim专用复合材料设计和制造软件和铺层方法来满足jsf部件使用性能的要求。
下面是波音公司复合材料部件的数字化设计制造过程。
(1)波音公司工程师用catia定义模具面、层的位置和边界、泡沫夹芯的位置等。
fibersim软件将层管理起来,为每个层自动生成一个表格,记录非几何信息,如材料、方向和顺序,并将这些信息与层的几何边界、相关的标记等联系起来,确保层在制造过程中能正确定位。
(2)在初步设计阶段,进行层制造可行性分析,软件将显示出在铺层时可能发生制造问题的区域,对层的设计进行优化,并计算层的平面展开图样。fibersim在设计阶段而不是在铺层阶段生成层的展开图样,并优化层间的错列方式,提高了材料的结构特性,避免了反复设计的过程,节省了材料,大大降低了成本。
(3)利用fibersim软件文档功能,生成铺层图、铺层表、材料表和序列表。与原来使用cad系统和电子表格生成这些文档相比,fibersim更加自动化,从而使设计时间降低了约50%。
(4)将fibersim生成的包括层合板信息的数据输入到下料机和喷涂设备。这种设计与制造设备的无缝连接,保证了设计模型与制造产品的一致性。fibersim将平面展开图样输出到优化排料软件包中,排料软件生成下料机的数控程序,对制造过程进行优化,在节省大量时间的同时,提高了加工的精度和材料的使用率。fibersim生成的程序控制喷涂机在模具上进行层的形状和边界的喷涂,对层的铺放进行定位,简化了碳纤维的铺放过程。
采用新的技术和软件来设计和制造复合材料部件后,波音公司节省了5%~25%的初始设计时间,减少了45%的反复设计修改时间,极大降低了手工铺层时间(铺完一个层从90min减到45min),全过程控制复合材料层和带的形状和铺放,消除反复试验过程,提高了产品的质量。
2 在x-35样机研制中的应用
飞机的进气道为形状复杂的大型多曲度管状零件,用复合材料体系成型困难,所以多采用铝金属材料。在jsf样机x-35的设计中,大量采用了复合材料部件,例如进气道,该部件几何形状复杂,铺层时常有扭曲的趋势,纤维方向的偏移将降低零件的整体性能,在一些区域内铺层会聚成一团发生皱缩。洛克希德·马丁公司决定将fibersim专用复合材料设计制造软件用于jsf进气道的验证上,继而应用到其他的零件中。
fibersim软件在铺层的设计阶段仿真层的铺放过程,根据这些信息,优化层的设计,直接对铺层加切口或拼接,软件会计算并显示出层铺放的结果,达到要求后,便完成了铺层几何定义,将材料的扭曲降至公差范围内,消除起皱和开裂现象。设计好铺层的几何参数后,fibersim软件自动生成层的平面展开图样。在制造阶段,软件将各层展开图样输出到数控切割设备。三维模型与切割设备无缝连接,实现切割自动化。同时这种无缝连接方式降低了造成层大小和方向出错的可能。由于fibersim软件生成了平面展开图样,排料软件在机床上优化组合各层的位置,极大地降低了废料的产生。自动化切割替代了手工切割,在提高产品质量的同时,节约了大量的材料和成本。
利用fibersim软件,生成激光投影系统(lps)所需的三维层边界、孔、拼接和标记的数据。激光投影系统读取这些数据,在模具上投影出层的边界。技师们按照连续的激光投影线放置层。将fibersim软件应用到辅助进气道后,设计时间从300h减少到150h,制造时间从450h减少到200h。洛克西德·马丁公司利用fibersim软件不仅节约了大量的时间,而且将不合格样品率降至最低,提高了产品质量和可靠性。
飞机换代最突出的体现就是对飞机性能要求的不断提高,包括减轻结构重量,降低巡航阻力,增大航程;减少结构疲劳损坏,延长使用寿命;降低制造成本和维护费用。这些要求决定了飞机减重的迫切性,使航空部件材料和结构的选择成为提高飞机性能的关键因素。
碳纤维复合材料具有比强度大、比刚度高、抗疲劳性能好、各向异性以及材料性能可设计的特点,应用于航空领域中,可以获得显著的减重效益,并改善结构性能。目前,复合材料技术已成为影响飞机发展的关键技术之一,逐渐应用于飞机结构的主承力构件中,可达到减重20%~30%的效果。因此,它在航空航天领域的应用日益广泛,已迅速发展成为包括铝、钢、钛在内的四大航空航天结构材料之一。
除减重外,复合材料还具有更好的耐久性,可降低使用维护成本。在人类有动力飞行进入第二个百年之后,复合材料开始“领跑”飞机设计技术,成为“航空航天结构的未来”。
碳纤维复合材料设计制造技术的发展
传统复合材料设计和制造过程是分别进行的。对于复杂的结构,通常较难确定满足铺层边界要求的准确平面展开图样,为避免材料的扭曲变形,需要在制造车间大量地反复试验修改,造成了贵重材料的浪费和大量的车间返工;同时将碳纤维铺放在一起需花费大量时间(铺完一个机翼壁板铺层大约需要90~120min),这在一定程度上反映了制造机翼这样的大型零件所要面临的挑战。
现在,这些问题由于采用了新的复合材料设计制造关键技术而得以解决。
(1)设计与制造一体化技术。
随着计算机和制造技术的进步,复合材料设计制造技术可采用全新的设计理念和手段,将设计和制造融为一体,将程序化的软件用于生产制造中,使制造中的问题在设计初期阶段就能加以考虑,从而加快产品研制进度,提高质量,降低成本。
(2)大面积整体成形技术。
以共固化/共胶接(cocured/cobonded)和无紧固件(fastenerless)为核心的整体成形技术,采用大面积整体成形,少用或不用紧固件,减少了零件数目,减轻了重量,降低了连接、装配和制造的成本。
(3)低成本的制造技术。
先进复合材料自60年代中期问世以来,在军用、民用领域的应用均得到飞速的发展。但复合材料的成本,特别是制造成本较高,成为复合材料进一步应用推广的主要障碍之一。该问题已引起世界各国的普遍重视,特别是以美国为首的西方发达国家纷纷制定低成本的复合材料发展研究计划,努力实践,并已取得较大进展。目前,低成本复合材料技术已成为全世界复合材料发展研究领域的一个核心课题。
复合材料制造成本约占复合材料成本的80%~85%,所以低成本复合材料技术中关键是低成本的制造技术。采用复合材料数字化设计制造技术,能最大限度地节省时间和劳动力,速度较手工提高了10倍;同时能节省原材料,提高制件精度和质量,从而降低了制造成本。
Fibersim复合材料设计制造软件
fibersim是一个可以实现复合材料数字化设计制造一体化的软件,它与cad软件紧密集成,实现了设计和分析自动化,生成制造工程信息和驱动激光投影仪、自动切割机、纤维铺放设备的数据,覆盖复合材料整个工艺设计过程,为复合材料的设计和制造提供全面的解决方案,适应了复合材料设计制造技术的发展要求。
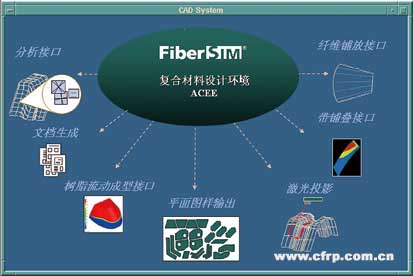
fibersim设计制造一体化环境
fibersim软件已成功用于商用和军用飞机的设计,能够完成复合材料部件的可制造性评估,精确模拟纤维的材料特性,生成平面展开图样,完成复合材料部件的分析、设计和制造,对层合板进行验证。将三维几何模型与层合板的设计联系起来,并将层合板的设计信息与有限元分析软件和制造设备形成无缝连接,可实现制造过程自动化,降低制造成本。
fibersim在飞机复合材料部件数字化设计制造中的应用
复合材料的性能很好地满足了当代新型飞机的相应需求。在美国先进联合攻击战斗机jsf的研制中,波音和洛克希德·马丁公司都分别使用了大量的复合材料构件,对这两家公司都是一大挑战。他们引进了fibersim软件,采用新的技术手段,利用先进的数字化设计制造技术满足联合攻击战斗机(jsf)苛刻的强度要求、成本目标和重量标准,克服了传统复合材料设计制造中的困难,充分体现了新世纪复合材料构件低成本技术的发展水平。
1 在x-32样机研制中的应用
从应用领域来看,碳纤维复合材料主要用于航空航天等领域,波音公司在制造联合攻击战斗机样机x-32的很多大型部件时,就设计采用了单向碳纤维复合材料。并选用了fibersim专用复合材料设计和制造软件和铺层方法来满足jsf部件使用性能的要求。
下面是波音公司复合材料部件的数字化设计制造过程。
(1)波音公司工程师用catia定义模具面、层的位置和边界、泡沫夹芯的位置等。
fibersim软件将层管理起来,为每个层自动生成一个表格,记录非几何信息,如材料、方向和顺序,并将这些信息与层的几何边界、相关的标记等联系起来,确保层在制造过程中能正确定位。
(2)在初步设计阶段,进行层制造可行性分析,软件将显示出在铺层时可能发生制造问题的区域,对层的设计进行优化,并计算层的平面展开图样。fibersim在设计阶段而不是在铺层阶段生成层的展开图样,并优化层间的错列方式,提高了材料的结构特性,避免了反复设计的过程,节省了材料,大大降低了成本。
(3)利用fibersim软件文档功能,生成铺层图、铺层表、材料表和序列表。与原来使用cad系统和电子表格生成这些文档相比,fibersim更加自动化,从而使设计时间降低了约50%。
(4)将fibersim生成的包括层合板信息的数据输入到下料机和喷涂设备。这种设计与制造设备的无缝连接,保证了设计模型与制造产品的一致性。fibersim将平面展开图样输出到优化排料软件包中,排料软件生成下料机的数控程序,对制造过程进行优化,在节省大量时间的同时,提高了加工的精度和材料的使用率。fibersim生成的程序控制喷涂机在模具上进行层的形状和边界的喷涂,对层的铺放进行定位,简化了碳纤维的铺放过程。
采用新的技术和软件来设计和制造复合材料部件后,波音公司节省了5%~25%的初始设计时间,减少了45%的反复设计修改时间,极大降低了手工铺层时间(铺完一个层从90min减到45min),全过程控制复合材料层和带的形状和铺放,消除反复试验过程,提高了产品的质量。
2 在x-35样机研制中的应用
飞机的进气道为形状复杂的大型多曲度管状零件,用复合材料体系成型困难,所以多采用铝金属材料。在jsf样机x-35的设计中,大量采用了复合材料部件,例如进气道,该部件几何形状复杂,铺层时常有扭曲的趋势,纤维方向的偏移将降低零件的整体性能,在一些区域内铺层会聚成一团发生皱缩。洛克希德·马丁公司决定将fibersim专用复合材料设计制造软件用于jsf进气道的验证上,继而应用到其他的零件中。
fibersim软件在铺层的设计阶段仿真层的铺放过程,根据这些信息,优化层的设计,直接对铺层加切口或拼接,软件会计算并显示出层铺放的结果,达到要求后,便完成了铺层几何定义,将材料的扭曲降至公差范围内,消除起皱和开裂现象。设计好铺层的几何参数后,fibersim软件自动生成层的平面展开图样。在制造阶段,软件将各层展开图样输出到数控切割设备。三维模型与切割设备无缝连接,实现切割自动化。同时这种无缝连接方式降低了造成层大小和方向出错的可能。由于fibersim软件生成了平面展开图样,排料软件在机床上优化组合各层的位置,极大地降低了废料的产生。自动化切割替代了手工切割,在提高产品质量的同时,节约了大量的材料和成本。
利用fibersim软件,生成激光投影系统(lps)所需的三维层边界、孔、拼接和标记的数据。激光投影系统读取这些数据,在模具上投影出层的边界。技师们按照连续的激光投影线放置层。将fibersim软件应用到辅助进气道后,设计时间从300h减少到150h,制造时间从450h减少到200h。洛克西德·马丁公司利用fibersim软件不仅节约了大量的时间,而且将不合格样品率降至最低,提高了产品质量和可靠性。