碳纤维复合材料二步法三维编织变截面薄壁壳体RTM工艺数值模拟与试验研究
By www.carbonfiber.com.cn
摘要:采用分段一集合计算方法,对二步法三维编织变厚度变截面薄壁壳体RTM充模工艺过程进行了较深
人的理论研究。提出了较准确的树脂流动速度、树脂充模时问和树脂流动压力计算方程。数值预测值与充模试风电材料设备
验结果具有良好的一致性,所推导理论方程为合理设计RTM充模土艺参数提供了理论依据
关键词:复合材料;二步法三维编织;RTM;分段一集合计算方法;cfrp.cn中国碳纤维网
NUMERICAL SIMULATION AND EXPERIMENTAL STUDY OF RESIN FLOW IN RTM
PROCESSING FOR TWO STEP 3D BRAID SHELL PREFORM WITH VARYING SECTION
ZHANG Guoli,Lilu,I_I Xueming
(Composites Research Institute of Tianjin Polytechnic University, Tianjin 300160,China)
Abstract:hhc filling process of RT M for the two step 3D braid shell prcform with a varying section. was investi gated theoretically by employing a calculating method of divide-integratim.Several formulation、related to the resinvelocity,resin filling time and resin flow pressure were proposed accurately. Good agreement was found between the experimental results and numerical predictive values. The deduced formulations could provide the theoretical basis for suitably designing RTM filling parameters.
Keywords:composites; two. step 3D braiding;RTM;divide-integration method;numerical simulation
采用增强纤维三维空间交织成整体网状结构的三维整体编织(或机织)预成型体,通过合理选择不同的增强纤维、树脂基体和交织结构,可制造具有整体机械性能优异、结构尺寸稳定性好、耐热烧蚀、耐低温和优良的介电性能的新型结构和功能三维编织(或机织)复合材料。目前三维整体编织(或机织)变截面薄壁壳体RTM成型复合材料已替代传统的21)织物铺层壳体复合材料川,成为运载火箭壳体、复合裙、雷达天线罩等构件的首选承载结构之一。由于此类型壳体结构件尺寸大、纤维体积含量高、型面曲线和壁厚公差要求严格川,采用金属闭模RTM成型工艺进行加工时,提高树脂对纤维预制件的宏观和微观浸渗程度川,是确保复合材料质量和性能的技术关键。为解决RTM工艺充模过程中树脂流动规律的可预见性和可控制性的技术难题,国内外研究者多采用有限差分法、有限元控制体积法川、边界元法和贴体坐标法等数值模拟技术,实时地对形状简单的模腔内树脂流动形状和位置、树脂流动速度场、压力场和温度场的分布进行预测,以上数值方法往往程序编制复杂,计算机模拟计算耗时较长五月。本文作者采用分段一集合计算方法对RTM工艺充模过程中树脂流动进行了理论分析和试验研究,获得了典型三维整体编织变截面薄壁壳体树脂流动规律,为优化工艺设计提供重要的理论依据。
1 数学模型的建立
1.1分段一集合计算方法的基本原理
RTM充模的实质是液体树脂饱和充满纤维预制件孔隙并排除其内部所含空气的过程。考虑到三维整体编织变截面薄壁壳体的厚度与其直径和高度相比,数量级较小,且薄壁壳体KTM模具树脂流道的设计一般采用环线注射结构方式,因此树脂充模过程中的流动规律可近似为多孔介质中的一维渗流,即在柱面坐标系统(厂,夕,z)中,压力和速度值仅沿z方向变化。分段一集合计算方法是根据制件截面形状方程的种类数,沿轴线将壳体分成若干单元.利用Darcy分钟定律依次计算出各单元段内树脂流体的运功状态参数,经过数学变换,求得变截面薄壁壳体内不同位置的树脂流动速度场、压力场、位移场和充模时间的分布规律。为简化薄壁壳体树脂流动的理论分析与计算,作如日限设:充模过程中三维编织顶制件不会发生纤维移动和变形;充模过程中不考虑由于化学反应所引起的粘度变化,树脂的粘度值为一定值;充模过程中仅考虑宏观树脂流动现象.惯性和毛细作用忽略不计;树脂注人压力为Po(zo)。行流动前沿处压力为0.



2 试验
2.1三维编织变截面薄壁壳体预制件的编织风电材料设备
采用二步法三维编织工艺,在组合式编织机上,根据图2所示的变截面薄壁壳体预制件的形状结构和尺寸大小.在芯模的周边上合理配置所需数FAVI纱和编织纱,轴向纱和$Tu织纱均使用号数为1200Tex无捻E一玻璃纤维,并利用增、减纱线工罗习实现三维编织薄壁壳体预制件截而厚度尺寸的大小,三维编织工艺参数如表1示。山于变截面薄壁壳体沿二轴方向具有四种截面形状函数方程,因此在数俏模拟理论计算过程中可将两壁壳体分成。
2.2 RTM充模理论计算与试验验证
2.2.1 RTM充模理论计算
利用复化辛卜生数值积分算法和Fortran 99算法语言,对所推导的理论方程(8)、(9)和(11)进行编程和数值计算。由方程(11)可知,在树脂粘度保持恒定及树脂流动前沿位置固定的R丁M充模工艺条件下,注射口压力和三维编织变截面薄壁壳体预制件渗透率与空隙率(妇的乘积值确定了树脂充模溢流时间的大小。图3(a)表示在不同注射口压力条件下渗透率与空隙率的乘积值对树脂充模溢流时间的影响。图3(b)表示在不同的渗透率与空隙率的乘积值条件下注射口压力大小对树脂充模溢流时问变化规律的影响。图4表示在注射r1压力分别为420 kPa和620 kPa的恒压条件下,三个固定位置上(z=100 mm,z2=160 min、=260 mm)压力理论值p(z1)p(z2)和p(z3)与树脂流动前沿位置对应关系曲线。山图4可知,树脂饱和浸润区」或内固定点压力随树脂流动前沿位置递增而增大。
2.2.2试验验证
由方程(8)和(9)可知,固定位置树脂流动压力
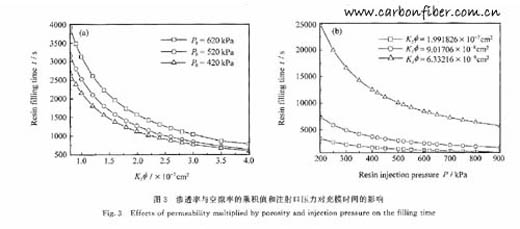


值取决于树脂流动前沿位置和注射日压力的大小。为了验证所提出的三维编织变截面薄壁壳体RTM工艺树脂充模流动分段一集合理论计算方法的正确性,对表1所示的三种规格的三维编织变截面薄壁壳体进行了RTM充模试验。试验选用TDE-85/DDS/BF,乙胺环氧树脂体系,以100:15:1.5的质最比例混配成所需的胶液,在35分钟C经测试,树脂粘度为428.6 mPa·s(树脂粘度测试标准为GB7193-1),固化后其浇注体密度为1. 302 g/crn分钟(密度测试标准为GB 1033-70)。为准确测量树脂充模溢流时间,本试验中采用透明有机玻璃材料加工RTM模具出料口端盖,并且在模具内部相应的位置点上安装压力传感器以测量树脂溢流后固定位置上的树脂流动压力。树脂充模溢流时间理论计算值与实测结果的比较、三个固定位置上树脂流动压力理论计算值与实测结果的对比如表2所示。由表2所列树脂充模溢流时间理论计算值与实测值的比较值可知:当K矛值较大时,树脂充模溢流时间理论计算值具有较高的预测精度场K淤值逐渐减小时,树脂充模溢流时问逐渐增大,并且理论计算值与实测值的相对误差逐渐增大,这主要是由于过长的充模时间引起树脂粘度增加所致。
由表2所示的理论预测、实测值数据的比较结果可知,当树脂溢流后,随着三维编织变截面壁壳体预制件纤维含量和粘滞性树脂流体浸润高度的增加,流动阻力的累加效应会造成压力损失程度的提高,因此树脂流动压力逐渐减小,理论预测值与实测值的误差会相应增大。
3 结论
在一维Darcy分钟s定律和连续性定律基础上,对三维编织变厚度变截面薄壁壳体RTM充模工艺过程中树脂流动速度、树脂充模时间和树脂流动压力进行了较深人的理论和充模试验研究,对比分析理论方程、计算数值和充模试验结果可知:定压注射、恒定粘度RTM充模过程中,饱和浸润模腔内任意点树脂渗流速度和流动压力随其截面形状函数的大小和树脂流动前沿位置而变化,并且流动阻力的累加效应所造成的压力损失程度随纤维含量和粘滞性树脂流体浸润高度的增加而增加。
(1)通过考虑树脂流动重力影响因素,利用分段一集合计算新方法,有效地提高了RTM数值模拟计算精度。
(2)利用Fortran 99算法语言和复化辛卜生数值积分算法,对所推导树脂充模时间和树脂流动压力理论方程进行数滇计算,与RTM充模工艺试验结果比较证明理论预测值与实验值吻合较好.
(3)对于加工特定结构的三维编织变截面薄壁壳体复合材料制件,借助于方程(7)、(8)、(9)和(11)的理论顶测结果,可合理设计RTM充模工艺参数。
参考文献:
[1]丑李嘉禄,孙颖.二步法方型三维编织预制件编织结构参数与工艺参数[J].复合材料学报,2003,20(2):51-37.ti 1 I,Sun Y. Braiding structure parameters and process parameters of the two-step rectangle 31) braided preform [J]ActaMateriae Compositae Sinica,2003,20(2): 81- 87.
[2]郭世峰.RTM -C艺用耐高(a树脂研制仁1」.字航材料T艺, 2001,20(3):36一37.
[3]邵雪明.纺织复合材料预制件多层机织布内气泡形成机理 C17. Y合材料学报,2003,20(3):57-63.Shoo X M. Mechanism of void formation in textile preform multi-layer woven fabrics〔1〕.Acta Materine Composime Simica,2003,20(3): 57-63.
[4]Long A C. Process modeling for liquid moulding of braided preforms[1].Composites Part A,2001,32(7):941-953.
[5]习秦伟,李海晨,张志谦,等RTM工艺树脂流动过程数 值模拟及实验比较[J〕.复合材料学报,2003,20(4): 77-80.风电材料设备Qin W, 1.i 11 C, Zhang Z Q, et at. Comparison between numerical simulation and experimental result of resin flow in RTM [J]. Acta Materiae Compositae Sinica,2003,20(4)77-80.
[6]江顺亮.树脂传递成型加工注射C1位置的快速优化法〔J」. 复合材料学报,2002,9(4): 19-24.
[7]张国利.RFI树脂流动规律的研究〔1〕.天津工业大学学报,2002,21(2), 3已一40.
[8]Dungan F D, Sastry A M, Saturated and unsaturated polymet flows:Microphenomena and Modeling1〕.Joarna1 of Composite Materials.2002, 36(13)t 1581一1$99.www.cnwpem.net
[9]Lin J L, Young W B. T}飞。effect of preheater on the resin transfer molding [1]. Journal of Reinforced Plastics and Composites,1999,1800):954一965.
[10]焦亚男,李嘉禄.李学明.二步编织法制作三维整休预制件 [J]玻璃钢/复合材料,2000(5):27-28.
摘要:采用分段一集合计算方法,对二步法三维编织变厚度变截面薄壁壳体RTM充模工艺过程进行了较深
人的理论研究。提出了较准确的树脂流动速度、树脂充模时问和树脂流动压力计算方程。数值预测值与充模试风电材料设备
验结果具有良好的一致性,所推导理论方程为合理设计RTM充模土艺参数提供了理论依据
关键词:复合材料;二步法三维编织;RTM;分段一集合计算方法;cfrp.cn中国碳纤维网
NUMERICAL SIMULATION AND EXPERIMENTAL STUDY OF RESIN FLOW IN RTM
PROCESSING FOR TWO STEP 3D BRAID SHELL PREFORM WITH VARYING SECTION
ZHANG Guoli,Lilu,I_I Xueming
(Composites Research Institute of Tianjin Polytechnic University, Tianjin 300160,China)
Abstract:hhc filling process of RT M for the two step 3D braid shell prcform with a varying section. was investi gated theoretically by employing a calculating method of divide-integratim.Several formulation、related to the resinvelocity,resin filling time and resin flow pressure were proposed accurately. Good agreement was found between the experimental results and numerical predictive values. The deduced formulations could provide the theoretical basis for suitably designing RTM filling parameters.
Keywords:composites; two. step 3D braiding;RTM;divide-integration method;numerical simulation
采用增强纤维三维空间交织成整体网状结构的三维整体编织(或机织)预成型体,通过合理选择不同的增强纤维、树脂基体和交织结构,可制造具有整体机械性能优异、结构尺寸稳定性好、耐热烧蚀、耐低温和优良的介电性能的新型结构和功能三维编织(或机织)复合材料。目前三维整体编织(或机织)变截面薄壁壳体RTM成型复合材料已替代传统的21)织物铺层壳体复合材料川,成为运载火箭壳体、复合裙、雷达天线罩等构件的首选承载结构之一。由于此类型壳体结构件尺寸大、纤维体积含量高、型面曲线和壁厚公差要求严格川,采用金属闭模RTM成型工艺进行加工时,提高树脂对纤维预制件的宏观和微观浸渗程度川,是确保复合材料质量和性能的技术关键。为解决RTM工艺充模过程中树脂流动规律的可预见性和可控制性的技术难题,国内外研究者多采用有限差分法、有限元控制体积法川、边界元法和贴体坐标法等数值模拟技术,实时地对形状简单的模腔内树脂流动形状和位置、树脂流动速度场、压力场和温度场的分布进行预测,以上数值方法往往程序编制复杂,计算机模拟计算耗时较长五月。本文作者采用分段一集合计算方法对RTM工艺充模过程中树脂流动进行了理论分析和试验研究,获得了典型三维整体编织变截面薄壁壳体树脂流动规律,为优化工艺设计提供重要的理论依据。
1 数学模型的建立
1.1分段一集合计算方法的基本原理
RTM充模的实质是液体树脂饱和充满纤维预制件孔隙并排除其内部所含空气的过程。考虑到三维整体编织变截面薄壁壳体的厚度与其直径和高度相比,数量级较小,且薄壁壳体KTM模具树脂流道的设计一般采用环线注射结构方式,因此树脂充模过程中的流动规律可近似为多孔介质中的一维渗流,即在柱面坐标系统(厂,夕,z)中,压力和速度值仅沿z方向变化。分段一集合计算方法是根据制件截面形状方程的种类数,沿轴线将壳体分成若干单元.利用Darcy分钟定律依次计算出各单元段内树脂流体的运功状态参数,经过数学变换,求得变截面薄壁壳体内不同位置的树脂流动速度场、压力场、位移场和充模时间的分布规律。为简化薄壁壳体树脂流动的理论分析与计算,作如日限设:充模过程中三维编织顶制件不会发生纤维移动和变形;充模过程中不考虑由于化学反应所引起的粘度变化,树脂的粘度值为一定值;充模过程中仅考虑宏观树脂流动现象.惯性和毛细作用忽略不计;树脂注人压力为Po(zo)。行流动前沿处压力为0.



2 试验
2.1三维编织变截面薄壁壳体预制件的编织风电材料设备
采用二步法三维编织工艺,在组合式编织机上,根据图2所示的变截面薄壁壳体预制件的形状结构和尺寸大小.在芯模的周边上合理配置所需数FAVI纱和编织纱,轴向纱和$Tu织纱均使用号数为1200Tex无捻E一玻璃纤维,并利用增、减纱线工罗习实现三维编织薄壁壳体预制件截而厚度尺寸的大小,三维编织工艺参数如表1示。山于变截面薄壁壳体沿二轴方向具有四种截面形状函数方程,因此在数俏模拟理论计算过程中可将两壁壳体分成。
2.2 RTM充模理论计算与试验验证
2.2.1 RTM充模理论计算
利用复化辛卜生数值积分算法和Fortran 99算法语言,对所推导的理论方程(8)、(9)和(11)进行编程和数值计算。由方程(11)可知,在树脂粘度保持恒定及树脂流动前沿位置固定的R丁M充模工艺条件下,注射口压力和三维编织变截面薄壁壳体预制件渗透率与空隙率(妇的乘积值确定了树脂充模溢流时间的大小。图3(a)表示在不同注射口压力条件下渗透率与空隙率的乘积值对树脂充模溢流时间的影响。图3(b)表示在不同的渗透率与空隙率的乘积值条件下注射口压力大小对树脂充模溢流时问变化规律的影响。图4表示在注射r1压力分别为420 kPa和620 kPa的恒压条件下,三个固定位置上(z=100 mm,z2=160 min、=260 mm)压力理论值p(z1)p(z2)和p(z3)与树脂流动前沿位置对应关系曲线。山图4可知,树脂饱和浸润区」或内固定点压力随树脂流动前沿位置递增而增大。
2.2.2试验验证
由方程(8)和(9)可知,固定位置树脂流动压力
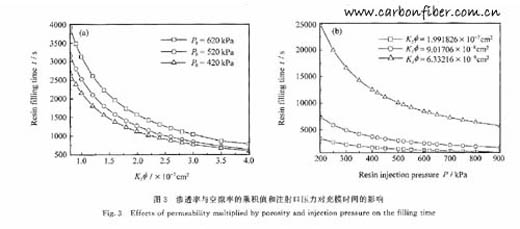


值取决于树脂流动前沿位置和注射日压力的大小。为了验证所提出的三维编织变截面薄壁壳体RTM工艺树脂充模流动分段一集合理论计算方法的正确性,对表1所示的三种规格的三维编织变截面薄壁壳体进行了RTM充模试验。试验选用TDE-85/DDS/BF,乙胺环氧树脂体系,以100:15:1.5的质最比例混配成所需的胶液,在35分钟C经测试,树脂粘度为428.6 mPa·s(树脂粘度测试标准为GB7193-1),固化后其浇注体密度为1. 302 g/crn分钟(密度测试标准为GB 1033-70)。为准确测量树脂充模溢流时间,本试验中采用透明有机玻璃材料加工RTM模具出料口端盖,并且在模具内部相应的位置点上安装压力传感器以测量树脂溢流后固定位置上的树脂流动压力。树脂充模溢流时间理论计算值与实测结果的比较、三个固定位置上树脂流动压力理论计算值与实测结果的对比如表2所示。由表2所列树脂充模溢流时间理论计算值与实测值的比较值可知:当K矛值较大时,树脂充模溢流时间理论计算值具有较高的预测精度场K淤值逐渐减小时,树脂充模溢流时问逐渐增大,并且理论计算值与实测值的相对误差逐渐增大,这主要是由于过长的充模时间引起树脂粘度增加所致。
由表2所示的理论预测、实测值数据的比较结果可知,当树脂溢流后,随着三维编织变截面壁壳体预制件纤维含量和粘滞性树脂流体浸润高度的增加,流动阻力的累加效应会造成压力损失程度的提高,因此树脂流动压力逐渐减小,理论预测值与实测值的误差会相应增大。
3 结论
在一维Darcy分钟s定律和连续性定律基础上,对三维编织变厚度变截面薄壁壳体RTM充模工艺过程中树脂流动速度、树脂充模时间和树脂流动压力进行了较深人的理论和充模试验研究,对比分析理论方程、计算数值和充模试验结果可知:定压注射、恒定粘度RTM充模过程中,饱和浸润模腔内任意点树脂渗流速度和流动压力随其截面形状函数的大小和树脂流动前沿位置而变化,并且流动阻力的累加效应所造成的压力损失程度随纤维含量和粘滞性树脂流体浸润高度的增加而增加。
(1)通过考虑树脂流动重力影响因素,利用分段一集合计算新方法,有效地提高了RTM数值模拟计算精度。
(2)利用Fortran 99算法语言和复化辛卜生数值积分算法,对所推导树脂充模时间和树脂流动压力理论方程进行数滇计算,与RTM充模工艺试验结果比较证明理论预测值与实验值吻合较好.
(3)对于加工特定结构的三维编织变截面薄壁壳体复合材料制件,借助于方程(7)、(8)、(9)和(11)的理论顶测结果,可合理设计RTM充模工艺参数。
参考文献:
[1]丑李嘉禄,孙颖.二步法方型三维编织预制件编织结构参数与工艺参数[J].复合材料学报,2003,20(2):51-37.ti 1 I,Sun Y. Braiding structure parameters and process parameters of the two-step rectangle 31) braided preform [J]ActaMateriae Compositae Sinica,2003,20(2): 81- 87.
[2]郭世峰.RTM -C艺用耐高(a树脂研制仁1」.字航材料T艺, 2001,20(3):36一37.
[3]邵雪明.纺织复合材料预制件多层机织布内气泡形成机理 C17. Y合材料学报,2003,20(3):57-63.Shoo X M. Mechanism of void formation in textile preform multi-layer woven fabrics〔1〕.Acta Materine Composime Simica,2003,20(3): 57-63.
[4]Long A C. Process modeling for liquid moulding of braided preforms[1].Composites Part A,2001,32(7):941-953.
[5]习秦伟,李海晨,张志谦,等RTM工艺树脂流动过程数 值模拟及实验比较[J〕.复合材料学报,2003,20(4): 77-80.风电材料设备Qin W, 1.i 11 C, Zhang Z Q, et at. Comparison between numerical simulation and experimental result of resin flow in RTM [J]. Acta Materiae Compositae Sinica,2003,20(4)77-80.
[6]江顺亮.树脂传递成型加工注射C1位置的快速优化法〔J」. 复合材料学报,2002,9(4): 19-24.
[7]张国利.RFI树脂流动规律的研究〔1〕.天津工业大学学报,2002,21(2), 3已一40.
[8]Dungan F D, Sastry A M, Saturated and unsaturated polymet flows:Microphenomena and Modeling1〕.Joarna1 of Composite Materials.2002, 36(13)t 1581一1$99.www.cnwpem.net
[9]Lin J L, Young W B. T}飞。effect of preheater on the resin transfer molding [1]. Journal of Reinforced Plastics and Composites,1999,1800):954一965.
[10]焦亚男,李嘉禄.李学明.二步编织法制作三维整休预制件 [J]玻璃钢/复合材料,2000(5):27-28.