大数据与碳纤维复合材料制造浅谈
By www.carbonfiber.com.cn
随着美国工业联网、德国工业4.0计划和中国制造2025等智能制造概念的兴起,标志着制造行业即将全面由自动化进入智能化时代。
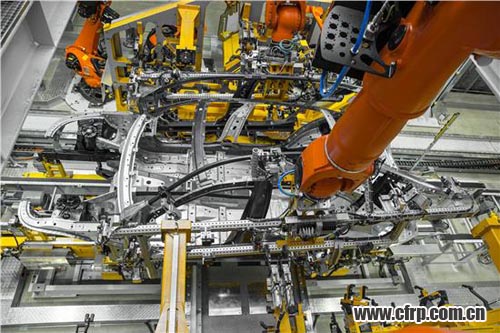
自从1953年雪佛兰corvette跑车第一次使用了碳纤维复合材料零件,60多年来,碳纤维材料被新材料的光环围绕,一直以来与普通大众有种若即若离的感觉,而直到2013年宝马i3量产型碳纤维轿车的亮相,普通民众才猛然发现碳纤维时代似乎已经来到了。
所谓一个“时代”,必将由与普通大众息息相关的规模化生产而引领。碳纤维能否引领一个时代,其工业化应用能否跟上自动化的脚步而迈入智能制造的门槛,还面临着诸多难题。
2016年1月23日参加了卢秉恒、高金吉、王立鼎、谭建荣、徐宗本等装备制造与数据分析方面的几位院士主持的“大数据与智能制造”专项论证会,发现不同行业专家对大数据分析与智能制造的具体理解都不尽相同,每个行业实现智能制造的条件和时间也不一样。
碳纤维复合材料的智能化制造离我们也许很近也许很远,但是用中国商飞刘卫平研究员的话来讲,使用先进数据分析技术全面提升先进复合材料结构制造水平是现代化制造的必由之路,提前思考总是好的。
智能化制造必然基于自动制造技术与数据分析技术,没有数据分析、没有分析结果的反馈与程序判断指令的再发出,就不会有智能。
因此,这里先谈谈碳纤维复合材料智能化制造的基本元素——数据。复材的制造过程主要涉及材料数据、设计数据与工艺数据,下面简要分析一下其特点:
1.材料种类多、性能参数多且离散度大
碳纤维只是一个笼统的概念,仅仅按照原丝类型区分就有聚丙烯腈基碳纤维、粘胶基碳纤维、沥青基碳纤维等;
其次,树脂基体材料的复杂性地球人都知道。
另外,碳纤维复合材料本身就是一种结构性材料,树脂与纤维之间存在复杂的力学关系。
因此,材料的力学与物理特性离散度往往较大,关键性能参数往往需要大量样本进行统计,还不一定会收敛。
基体的树脂材料在固化前化学稳定性不是很好,材料部分属性会随着储存时间不同而发生改变。
另外,材料在固化过程中发生相变,要准确描述这一过程没有七八十个参数谈何容易。
碳纤维复合材料一旦要进入工业应用,大量许用值试验是必须要开展的,因此,碳纤维工业化进程中引入的材料数据将是传统材料的几十倍甚至上百倍。
2.结构设计难度大、变量多
结构设计难度体现在设计变量多,最基本的有铺层方向和铺层顺序参数,其次碳纤维分为单向带和织物,而织物又有平纹、斜纹及更复杂的编织方式。
另外,碳纤维复合材料结构的强度设计非常困难。复合材料的破坏模式比较复杂,简单的有纤维拉伸破坏、基体拉伸/压缩破坏、基体剪切分层破坏,还有Tsai-Hill、Tsai-Wu等准则所表征的更加复杂的破坏模式。
复合材料结构的强度破坏模式都需要配合大量试验进行确定。因此,复合材料结构设计与强度校核中所发生的数据量是传统材料的数十倍。
3.基于制造过程复杂、工艺参数多
复合材料制造与传统材料完全不同,主要有热压罐工艺、液体成型工艺和模压工艺等。
每一种工艺针对的材料体系就有可能不同,另外制造过程还涉及如隔离膜、透气毡、腻子条、胶膜等十几种辅料。
多数传统材料零件制造都是基于对坯料加工的基础上进行的,质量方面主要关注几何精度,而复合材料零件制造工艺与传统零件完全不同,不仅仅要关注几何精度、更要关注零件内部的缺陷问题。不同的工艺参数,如时间、温度、压力等与零件内部质量有非常密切的联系。
另外,复合材料由于其各向异性所导致固化变形问题很难避免,会直接影响零件几何外形,因此提前对模具进行型面补偿的过程,也涉及到大量设计数据处理。
如何利用碳纤维复合材料工业化应用过程中产生的数据,如何使这些数据变为一个有机的整体,还需要解决几个方面的问题,如,数据分析平台的顶层设计问题、数据的生成问题,数据的采集问题,数据筛选问题、数据定义问题、非结构化数据处理问题、计算建模问题、模型求解问题、数据分析结果验证问题等。
因为正如开篇所讲的,没有数据、没有让数据动起来的分析技术与平台,就没有智能。
对于碳纤维复合材料制造过程如此复杂,要实现高品质规模化生产,必须要用自动化技术与数据分析技术提升制造水平,而这一过程中,有几个方面我们可以关注:
1.工艺流程的数字化设计无疑是重点与难点。相比于设计参数、材料特性等较直观的数据,如何将工艺流程数字化表征,体现工艺的特点,形成智能空间的分析依据,是未来开发的重点。
2.利用CAE虚拟仿真技术对材料数据和工艺数据进行数学与力学建模,建立上述数据与复材零件质量的内在联系,形成核心数据关系链条,是解决“制造—质量”的核心关键问题。
3.复合材料制造过程中的材料参数与工艺参数密切相关,在铺带、铺丝、RTM设备及模具上考虑安装监测传感器,形成材料参数与工艺参数在线监测与反馈机制,尤其是形成材料固化过程中的材料属性监测与固化条监测的闭环,是智能制造条件下零件质量的重要保证。
4.实现基于虚拟空间的制造技术,形成基于大数据分析与CAE仿真技术为核心的虚拟分析平台,对“设计—制造”过程中的结构设计参数、材料参数、工艺参数、设备参数进行预先迭代匹配,形成最优工艺方案,然后发送指令至制造设备,再利用在线监测数据对生产过程控制与优化,最终生产出高品质的零件。
本文作者:杨青,中国商飞-上海飞机制造有限公司-复材中心,博士后研究员,研究方向复合材料工艺与虚拟仿真制造技术
随着美国工业联网、德国工业4.0计划和中国制造2025等智能制造概念的兴起,标志着制造行业即将全面由自动化进入智能化时代。
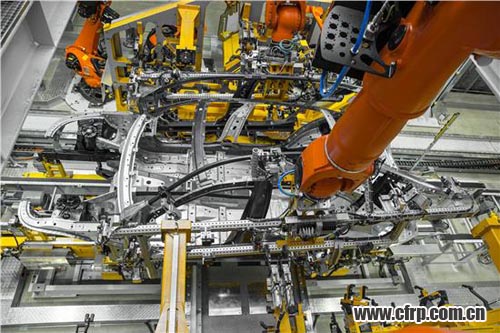
自从1953年雪佛兰corvette跑车第一次使用了碳纤维复合材料零件,60多年来,碳纤维材料被新材料的光环围绕,一直以来与普通大众有种若即若离的感觉,而直到2013年宝马i3量产型碳纤维轿车的亮相,普通民众才猛然发现碳纤维时代似乎已经来到了。
所谓一个“时代”,必将由与普通大众息息相关的规模化生产而引领。碳纤维能否引领一个时代,其工业化应用能否跟上自动化的脚步而迈入智能制造的门槛,还面临着诸多难题。
2016年1月23日参加了卢秉恒、高金吉、王立鼎、谭建荣、徐宗本等装备制造与数据分析方面的几位院士主持的“大数据与智能制造”专项论证会,发现不同行业专家对大数据分析与智能制造的具体理解都不尽相同,每个行业实现智能制造的条件和时间也不一样。
碳纤维复合材料的智能化制造离我们也许很近也许很远,但是用中国商飞刘卫平研究员的话来讲,使用先进数据分析技术全面提升先进复合材料结构制造水平是现代化制造的必由之路,提前思考总是好的。
智能化制造必然基于自动制造技术与数据分析技术,没有数据分析、没有分析结果的反馈与程序判断指令的再发出,就不会有智能。
因此,这里先谈谈碳纤维复合材料智能化制造的基本元素——数据。复材的制造过程主要涉及材料数据、设计数据与工艺数据,下面简要分析一下其特点:
1.材料种类多、性能参数多且离散度大
碳纤维只是一个笼统的概念,仅仅按照原丝类型区分就有聚丙烯腈基碳纤维、粘胶基碳纤维、沥青基碳纤维等;
其次,树脂基体材料的复杂性地球人都知道。
另外,碳纤维复合材料本身就是一种结构性材料,树脂与纤维之间存在复杂的力学关系。
因此,材料的力学与物理特性离散度往往较大,关键性能参数往往需要大量样本进行统计,还不一定会收敛。
基体的树脂材料在固化前化学稳定性不是很好,材料部分属性会随着储存时间不同而发生改变。
另外,材料在固化过程中发生相变,要准确描述这一过程没有七八十个参数谈何容易。
碳纤维复合材料一旦要进入工业应用,大量许用值试验是必须要开展的,因此,碳纤维工业化进程中引入的材料数据将是传统材料的几十倍甚至上百倍。
2.结构设计难度大、变量多
结构设计难度体现在设计变量多,最基本的有铺层方向和铺层顺序参数,其次碳纤维分为单向带和织物,而织物又有平纹、斜纹及更复杂的编织方式。
另外,碳纤维复合材料结构的强度设计非常困难。复合材料的破坏模式比较复杂,简单的有纤维拉伸破坏、基体拉伸/压缩破坏、基体剪切分层破坏,还有Tsai-Hill、Tsai-Wu等准则所表征的更加复杂的破坏模式。
复合材料结构的强度破坏模式都需要配合大量试验进行确定。因此,复合材料结构设计与强度校核中所发生的数据量是传统材料的数十倍。
3.基于制造过程复杂、工艺参数多
复合材料制造与传统材料完全不同,主要有热压罐工艺、液体成型工艺和模压工艺等。
每一种工艺针对的材料体系就有可能不同,另外制造过程还涉及如隔离膜、透气毡、腻子条、胶膜等十几种辅料。
多数传统材料零件制造都是基于对坯料加工的基础上进行的,质量方面主要关注几何精度,而复合材料零件制造工艺与传统零件完全不同,不仅仅要关注几何精度、更要关注零件内部的缺陷问题。不同的工艺参数,如时间、温度、压力等与零件内部质量有非常密切的联系。
另外,复合材料由于其各向异性所导致固化变形问题很难避免,会直接影响零件几何外形,因此提前对模具进行型面补偿的过程,也涉及到大量设计数据处理。
如何利用碳纤维复合材料工业化应用过程中产生的数据,如何使这些数据变为一个有机的整体,还需要解决几个方面的问题,如,数据分析平台的顶层设计问题、数据的生成问题,数据的采集问题,数据筛选问题、数据定义问题、非结构化数据处理问题、计算建模问题、模型求解问题、数据分析结果验证问题等。
因为正如开篇所讲的,没有数据、没有让数据动起来的分析技术与平台,就没有智能。
对于碳纤维复合材料制造过程如此复杂,要实现高品质规模化生产,必须要用自动化技术与数据分析技术提升制造水平,而这一过程中,有几个方面我们可以关注:
1.工艺流程的数字化设计无疑是重点与难点。相比于设计参数、材料特性等较直观的数据,如何将工艺流程数字化表征,体现工艺的特点,形成智能空间的分析依据,是未来开发的重点。
2.利用CAE虚拟仿真技术对材料数据和工艺数据进行数学与力学建模,建立上述数据与复材零件质量的内在联系,形成核心数据关系链条,是解决“制造—质量”的核心关键问题。
3.复合材料制造过程中的材料参数与工艺参数密切相关,在铺带、铺丝、RTM设备及模具上考虑安装监测传感器,形成材料参数与工艺参数在线监测与反馈机制,尤其是形成材料固化过程中的材料属性监测与固化条监测的闭环,是智能制造条件下零件质量的重要保证。
4.实现基于虚拟空间的制造技术,形成基于大数据分析与CAE仿真技术为核心的虚拟分析平台,对“设计—制造”过程中的结构设计参数、材料参数、工艺参数、设备参数进行预先迭代匹配,形成最优工艺方案,然后发送指令至制造设备,再利用在线监测数据对生产过程控制与优化,最终生产出高品质的零件。
本文作者:杨青,中国商飞-上海飞机制造有限公司-复材中心,博士后研究员,研究方向复合材料工艺与虚拟仿真制造技术