Zoltek Automotive公司CEO谈碳纤维在汽车领域的应用方向
By www.carbonfiber.com.cn
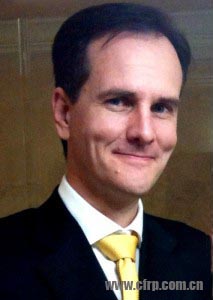
David Stewart, chief executive of Zoltek Automotive, speaks to CM Magazine on the growing use of carbon fiber composites.
Zoltek Automotive(卓尔泰克汽车公司)的CEO David Stewart与记者畅谈了碳纤维复合材料逐渐出现的新用途。
Stewart表示,目前碳纤维在风能产业中的应用要大大高于汽车行业。到底是什么因素驱使汽车制造商如此坚定的引入碳纤维制造。
碳纤维在生产过程中需要应用截然不同的制造工艺:周期时间(Cycle time)最为重要,其中复杂的几何零部件制造工艺比较复杂。
Zoltek公司对碳纤维未来用量做出的估计
哪类美国OEM汽车制造商最易使用复合材料部件?
Stewart:这确实是个巧妙的问题。说实话,我无法对他们每个企业的发展机会做出评论。我会说,GM(通用汽车)和Ford(福特汽车)各自拥有发展预算,能够让他们更容易抓住发展碳纤维汽车部件的机会。近期由于汽油价格的不断上涨,加上人们对保护环境的更多重视,是的OEM制造商们统统将研发的重点投放到碳纤维上。
OEM制造商在开发复合材料过程中面临的最大挑战是什么?
复合材料在可替代材料解决方案中是具有最大争议的,理由是,这种新型材料所采用的加工工艺与传统材料完全不同。设计与制造工艺完全改变,使得制造商现有的加工机械要完全更新换代才能完成这一新材料的制造。这对于制造商来说,无疑是一项巨大的投资和挑战,例如:设计,测试,质量管理等等。
为什么目前汽车工业还未能最大程度的应用碳纤维到制造工业中?
对于目前的汽车制造商来说,要将碳纤维制造技术应用到量产汽车中,确实还有一个努力的过程。在过去的几年中,我们确实看到了一些显著的发展。使得碳纤维在汽车中的应用进程大大加快。汽车工业在应用一款新型替代材料之前,制造商需要选择一种较小生产规模和资本投入,以及对环境友好的原材料。经过了这么多年,我们公司能够达到CAFÉ(平均燃油效率)的要求。
Zoltek公司对碳纤维未来价格走势做出的估计
未来Zoltek是否在批量生产中型汽车部件中看到市场?
我们确实对量产的碳纤维结构件非常感兴趣,包括压缩成型、 注射成型。我们不太喜欢喷涂零部件,因为不同的制造工艺存在一定的难度。驱动器轴、 机箱、 柱、 黄铜梁、 保险杠梁、 进气歧管和油箱。
目前业内将采用何种方法帮助碳纤维实现可回收性?
目前有很多不同的方法,可以评估最终用途。在欧洲,你必须考虑原材料在达到使用寿命后如何回收的问题。这对于热固性和热塑性复合材料就要面临不同的问题。目前与我们合作的公司正在着重开发碳纤维的回收利用技术。使用回收碳纤维制作的部件也是可回收的,因为碳可以保留原始性能中重要的一部分,即便是在二次利用后也是如此;此外,回收过程本身就已经大大减少了能源消耗。
行业背景
作为构成汽车以塑代钢的重要轻量化材料——玻璃钢/复合材料,与汽车节能、环保、安全有着密不可分的关系。采用玻璃钢/复合材料制造汽车车身壳体及其他相关部件,是使汽车轻量化最有效的途径之一;玻璃钢/复合材料的问世,为汽车造型设计提供了重要的变革条件,利用其设计自由度大和成型方便的特点为汽车产品的造型、功能增添了新奇与美感,实现汽车车身流线型的设计理念;同时,玻璃钢/复合材料还具有安全、低噪音、保温隔热等优良性能。由于汽车的质量减轻,滚动阻力减少,进而收到降低油耗、节约能源、减少环境污染以及保证安全等一系列效能。
福特公司研究表明,复合材料可以将零部件的数量减为原来的80%,加工费用相对钢材降低60%,粘结费用相对焊接减少25%到40%。复合材料是汽车工业保持竞争优势的潜在源泉。近年来,复合材料在促进汽车零部件模块化设计和生产方面取得了长足发展。所谓模块化生产,即是以一个零件(或部件)为中心将周边的零件组合在一起经一次成型加工而成,这样可以减少许多制造工艺和模具数量,进而降低整车的生产成本,使汽车在市场上有强大的竞争能力。如:1)福特F250/340“皮卡”及Explorer和Mountaineer SUVs的脚踏板采用40%长玻纤聚丙烯注塑成型制造的,取代用43个零件组装的部件。2)福特金牛座和水星黑貂轿车的前围里下散热器托架,原钢制的有22个零件,而采用SMC的才需2个件,重量大减,成本降14﹪。3)BMW系列的汽车变速箱组件采用35%玻纤增强PA66制成,它集成了许多零部件于一体,节约了发动机体内的宝贵空间。4)德国梅德赛斯-奔驰汽车公司在Atego、Vario、和Unimog三种型号轻型载货汽车上,使用玻璃纤维增强热塑性塑料(5%玻璃纤维增强尼龙)代替传统的铝金属材料制造摇臂盖,实现油分离器和摇臂盖的一体化设计,显着降低发动机的工作噪音。
未来的汽车与现在的汽车在很多方面不会有太大的区别,但设计思想会有很大不同。当今社会,人们目光的角度已逐渐转到人与自然的关系问题上,环境与能源问题成为世界上每个国家能否生存和发展的关键。随着人们环保意识的不断提高以及各国环保法规的相继出台,绿色汽车已经成为未来汽车发展的必然趋势。而复合材料作为未来汽车材料发展的主流,必将在其中扮演非常重要的角色。构筑材料、成型加工、设计、检查一体化的材料系统,形成联盟和集团化的组织系统,这将更充分的利用各方面的资源(技术资源、物质资源),紧密联系各方面的优势,以推动复合材料工业的进一步发展。汽车工业的发展日新月异,复合材料的研究也是一日千里,各种新型的车型,新式的材料不断地涌现。可以预测在不久的将来,更高性能的复合材料将更大范围地应用在汽车领域中。
Q&A: Which Automakers Are Most Likely to Use Composites?
David Stewart has been working in the automotive industry for over 20 years, taking technology out of labs and applying it to mass production environments. He owns a research firm, Stewart Automotive Research, and was just named chief executive of Zoltek Automotive, a new subsidiary from the carbon fiber supplier.
Zoltek’s CEO is quoted as saying carbon fiber is easier to use in wind energy than automotive. What makes automotive tougher to work with?
The volume requirements involve very different requirements on the manufacturing process. Cycle time is important, and the part geometry is substantially more complex. The chemistry of the curing process for thermosets needs to be tailored to the faster cycle time requirements. For preforming, getting the fibers into the appropriate alignment with the part geometry and structural requirements is a very different process for smaller parts with more curvature as compared to the structural parts in wind blades.
Why did Zoltek form this subsidiary?
The primary factor was renewed interest in automotive composites from the OEMs. Several OEMs have announced production programs where they’ll be delivering production vehicles that utilize lightweight carbon fiber materials. There are a few examples in production right now. In lower volumes, Tesla has carbon fiber body panels; in higher volumes, BMWs are being manufactured with carbon fiber structural and exterior body panel components. It has given some confidence to other OEMs that there’s a place for these materials in low-volume niche manufacturing and higher-volume production applications.
Which American OEMs are more likely to use composites?
That’s a tricky question. They all have equivalent incentives. I can’t comment on any of their individual development programs because of their proprietary requirements. I will say that GM and Ford have the development budgets that allow them to pursue these opportunities. It is worth noting that the latest wave of gasoline price increases and changes in the regulatory environment has led to that renewed interest among the OEMs in composites.
What are some of the biggest challenges OEMs have working with composites?
Composites are a challenge for material substitutions because the technology required to manufacture composites differs so much from the traditional materials they replace. The design and manufacturing infrastructure both change and that makes it challenging for existing capital industries to change over from one material to another. There’s such a huge investment in the existing way of doing things in the engineering, design, testing, quality control, etc.
Why hasn’t the automotive industry embraced carbon fiber more until now?
There’s a long lead time for developing these technologies for high-volume production. A number of efforts in the past have seen a three-year development cycle and a seven-year cycle for re-engineering an entire vehicle platform. Implementing substantial amounts of carbon fiber in the vehicle platform greatly impacts the engineering of the fundamental platform, painting process and crash analysis. Those changes need to be made up front in that development cycle.
Before moving a large amount of vehicle production to an alternative material, there’s a desire to have the material validated in a smaller-scale, less capital-intensive, less risky environment. A lower volume platform is selected initially, which is also a seven-year development cycle. You can get sufficient data to project the warranty costs and performance in an actual service environment. We’ve been through that cycle a few times, but every time when we have incentives from a fuel economy, the price of fuel has gone back down again. That volatility has never provided a sustained incentive to re-engineer vehicle architecture as well as maintaining the variable cost incentives to spend additional money on more expensive materials. Fuel prices need to be at a sustained projected level where the materials pay for themselves over the life of the vehicle.
Are we reaching that point, or will more instability follow?
After so many years, we finally have an increase in the corporate average fuel economy (CAFE) requirements. There is now a hard target that North American manufacturers have to meet. That hasn’t happened since the 1980s. Most manufacturers are projecting the price of oil to remain above $60 a barrel for a sustained period of time going forward.
What difficulties will you face in starting the subsidiary?
We need to establish a solid relationship with a fairly new and changing supply base. Recent difficulties in the auto industry have put most of the Tier 1 suppliers through Chapter 7 or 11 bankruptcies. There are some financially strong suppliers that do composite materials, but it’s always been a fragmented industry with a large number of suppliers and contracts for a fairly small volume of components. The OEMs and Tier 1s started to re-evaluate their relationship and the applications appropriate for the structural composite materials. We need to re-evaluate what that supply chain looks like and what support they’ll need.
What do manufacturers need to get involved in that re-evaluation?
The manufacturers with the largest ability to respond to new demand are those with the greatest investment in capability and design testing and manufacturing process equipment. So it requires a substantial investment. There’s not a lot of existing capacity out there that is drop-in and ready for a significant shift toward lightweight composites.
What does Zoltek see as the future of carbon fiber in medium to large production automotive parts?
We are most interested in structural components that lend themselves to high-volume manufacturing, compression molding and injection molding. We stay away from components that are painted because of the difficulties in reconciling the painting process with different manufacturing processes. We’re utilizing our material in this fashion, but we think it will remain a niche market from a volume sales standpoint, and by far the largest tonnage of carbon fiber is with the structural and underhood components such as drive shafts, chassis, pillar, brass beams, bumper beams, intake manifold and oil pans.
What production processes will the subsidiary incorporate?
We’re working with our customer base on all volume-capable carbon fiber manufacturing processes. These include preforming, resin transfer molding, compression molding for thermosets and thermoplastics, thermoplastic compounding for short and long fiber reinforced molding compounds, filament winding. If a process doesn’t have an established history, the development cycle for implementation into a high-volume vehicle platform is quite long. We’re focusing most of our efforts around established processes incorporating fiberglass, analogs or filament winding.
How can the industry improve its recycling of carbon fiber to improve its “green” aspect?
There are different ways for evaluating this aspect of end use requirements. It varies from one OEM to another. In Europe, you must identify exactly how this material will be recovered at its end of life. It’s a different question for thermosets and thermoplastics, and we’re working with companies who are developing techniques to reclaim carbon fiber at its end of life and recycle it either as short fiber or milled fiber materials. Over the course of the life of the material, the weight savings more than offsets its cost to produce and cost for end of life recycling.
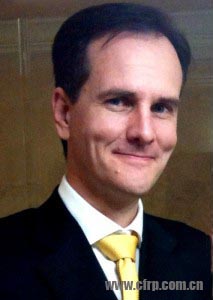
David Stewart, chief executive of Zoltek Automotive, speaks to CM Magazine on the growing use of carbon fiber composites.
Zoltek Automotive(卓尔泰克汽车公司)的CEO David Stewart与记者畅谈了碳纤维复合材料逐渐出现的新用途。
Stewart表示,目前碳纤维在风能产业中的应用要大大高于汽车行业。到底是什么因素驱使汽车制造商如此坚定的引入碳纤维制造。
碳纤维在生产过程中需要应用截然不同的制造工艺:周期时间(Cycle time)最为重要,其中复杂的几何零部件制造工艺比较复杂。
Zoltek公司对碳纤维未来用量做出的估计
哪类美国OEM汽车制造商最易使用复合材料部件?
Stewart:这确实是个巧妙的问题。说实话,我无法对他们每个企业的发展机会做出评论。我会说,GM(通用汽车)和Ford(福特汽车)各自拥有发展预算,能够让他们更容易抓住发展碳纤维汽车部件的机会。近期由于汽油价格的不断上涨,加上人们对保护环境的更多重视,是的OEM制造商们统统将研发的重点投放到碳纤维上。
OEM制造商在开发复合材料过程中面临的最大挑战是什么?
复合材料在可替代材料解决方案中是具有最大争议的,理由是,这种新型材料所采用的加工工艺与传统材料完全不同。设计与制造工艺完全改变,使得制造商现有的加工机械要完全更新换代才能完成这一新材料的制造。这对于制造商来说,无疑是一项巨大的投资和挑战,例如:设计,测试,质量管理等等。
为什么目前汽车工业还未能最大程度的应用碳纤维到制造工业中?
对于目前的汽车制造商来说,要将碳纤维制造技术应用到量产汽车中,确实还有一个努力的过程。在过去的几年中,我们确实看到了一些显著的发展。使得碳纤维在汽车中的应用进程大大加快。汽车工业在应用一款新型替代材料之前,制造商需要选择一种较小生产规模和资本投入,以及对环境友好的原材料。经过了这么多年,我们公司能够达到CAFÉ(平均燃油效率)的要求。
Zoltek公司对碳纤维未来价格走势做出的估计
未来Zoltek是否在批量生产中型汽车部件中看到市场?
我们确实对量产的碳纤维结构件非常感兴趣,包括压缩成型、 注射成型。我们不太喜欢喷涂零部件,因为不同的制造工艺存在一定的难度。驱动器轴、 机箱、 柱、 黄铜梁、 保险杠梁、 进气歧管和油箱。
目前业内将采用何种方法帮助碳纤维实现可回收性?
目前有很多不同的方法,可以评估最终用途。在欧洲,你必须考虑原材料在达到使用寿命后如何回收的问题。这对于热固性和热塑性复合材料就要面临不同的问题。目前与我们合作的公司正在着重开发碳纤维的回收利用技术。使用回收碳纤维制作的部件也是可回收的,因为碳可以保留原始性能中重要的一部分,即便是在二次利用后也是如此;此外,回收过程本身就已经大大减少了能源消耗。
行业背景
作为构成汽车以塑代钢的重要轻量化材料——玻璃钢/复合材料,与汽车节能、环保、安全有着密不可分的关系。采用玻璃钢/复合材料制造汽车车身壳体及其他相关部件,是使汽车轻量化最有效的途径之一;玻璃钢/复合材料的问世,为汽车造型设计提供了重要的变革条件,利用其设计自由度大和成型方便的特点为汽车产品的造型、功能增添了新奇与美感,实现汽车车身流线型的设计理念;同时,玻璃钢/复合材料还具有安全、低噪音、保温隔热等优良性能。由于汽车的质量减轻,滚动阻力减少,进而收到降低油耗、节约能源、减少环境污染以及保证安全等一系列效能。
福特公司研究表明,复合材料可以将零部件的数量减为原来的80%,加工费用相对钢材降低60%,粘结费用相对焊接减少25%到40%。复合材料是汽车工业保持竞争优势的潜在源泉。近年来,复合材料在促进汽车零部件模块化设计和生产方面取得了长足发展。所谓模块化生产,即是以一个零件(或部件)为中心将周边的零件组合在一起经一次成型加工而成,这样可以减少许多制造工艺和模具数量,进而降低整车的生产成本,使汽车在市场上有强大的竞争能力。如:1)福特F250/340“皮卡”及Explorer和Mountaineer SUVs的脚踏板采用40%长玻纤聚丙烯注塑成型制造的,取代用43个零件组装的部件。2)福特金牛座和水星黑貂轿车的前围里下散热器托架,原钢制的有22个零件,而采用SMC的才需2个件,重量大减,成本降14﹪。3)BMW系列的汽车变速箱组件采用35%玻纤增强PA66制成,它集成了许多零部件于一体,节约了发动机体内的宝贵空间。4)德国梅德赛斯-奔驰汽车公司在Atego、Vario、和Unimog三种型号轻型载货汽车上,使用玻璃纤维增强热塑性塑料(5%玻璃纤维增强尼龙)代替传统的铝金属材料制造摇臂盖,实现油分离器和摇臂盖的一体化设计,显着降低发动机的工作噪音。
未来的汽车与现在的汽车在很多方面不会有太大的区别,但设计思想会有很大不同。当今社会,人们目光的角度已逐渐转到人与自然的关系问题上,环境与能源问题成为世界上每个国家能否生存和发展的关键。随着人们环保意识的不断提高以及各国环保法规的相继出台,绿色汽车已经成为未来汽车发展的必然趋势。而复合材料作为未来汽车材料发展的主流,必将在其中扮演非常重要的角色。构筑材料、成型加工、设计、检查一体化的材料系统,形成联盟和集团化的组织系统,这将更充分的利用各方面的资源(技术资源、物质资源),紧密联系各方面的优势,以推动复合材料工业的进一步发展。汽车工业的发展日新月异,复合材料的研究也是一日千里,各种新型的车型,新式的材料不断地涌现。可以预测在不久的将来,更高性能的复合材料将更大范围地应用在汽车领域中。
Q&A: Which Automakers Are Most Likely to Use Composites?
David Stewart has been working in the automotive industry for over 20 years, taking technology out of labs and applying it to mass production environments. He owns a research firm, Stewart Automotive Research, and was just named chief executive of Zoltek Automotive, a new subsidiary from the carbon fiber supplier.
Zoltek’s CEO is quoted as saying carbon fiber is easier to use in wind energy than automotive. What makes automotive tougher to work with?
The volume requirements involve very different requirements on the manufacturing process. Cycle time is important, and the part geometry is substantially more complex. The chemistry of the curing process for thermosets needs to be tailored to the faster cycle time requirements. For preforming, getting the fibers into the appropriate alignment with the part geometry and structural requirements is a very different process for smaller parts with more curvature as compared to the structural parts in wind blades.
Why did Zoltek form this subsidiary?
The primary factor was renewed interest in automotive composites from the OEMs. Several OEMs have announced production programs where they’ll be delivering production vehicles that utilize lightweight carbon fiber materials. There are a few examples in production right now. In lower volumes, Tesla has carbon fiber body panels; in higher volumes, BMWs are being manufactured with carbon fiber structural and exterior body panel components. It has given some confidence to other OEMs that there’s a place for these materials in low-volume niche manufacturing and higher-volume production applications.
Which American OEMs are more likely to use composites?
That’s a tricky question. They all have equivalent incentives. I can’t comment on any of their individual development programs because of their proprietary requirements. I will say that GM and Ford have the development budgets that allow them to pursue these opportunities. It is worth noting that the latest wave of gasoline price increases and changes in the regulatory environment has led to that renewed interest among the OEMs in composites.
What are some of the biggest challenges OEMs have working with composites?
Composites are a challenge for material substitutions because the technology required to manufacture composites differs so much from the traditional materials they replace. The design and manufacturing infrastructure both change and that makes it challenging for existing capital industries to change over from one material to another. There’s such a huge investment in the existing way of doing things in the engineering, design, testing, quality control, etc.
Why hasn’t the automotive industry embraced carbon fiber more until now?
There’s a long lead time for developing these technologies for high-volume production. A number of efforts in the past have seen a three-year development cycle and a seven-year cycle for re-engineering an entire vehicle platform. Implementing substantial amounts of carbon fiber in the vehicle platform greatly impacts the engineering of the fundamental platform, painting process and crash analysis. Those changes need to be made up front in that development cycle.
Before moving a large amount of vehicle production to an alternative material, there’s a desire to have the material validated in a smaller-scale, less capital-intensive, less risky environment. A lower volume platform is selected initially, which is also a seven-year development cycle. You can get sufficient data to project the warranty costs and performance in an actual service environment. We’ve been through that cycle a few times, but every time when we have incentives from a fuel economy, the price of fuel has gone back down again. That volatility has never provided a sustained incentive to re-engineer vehicle architecture as well as maintaining the variable cost incentives to spend additional money on more expensive materials. Fuel prices need to be at a sustained projected level where the materials pay for themselves over the life of the vehicle.
Are we reaching that point, or will more instability follow?
After so many years, we finally have an increase in the corporate average fuel economy (CAFE) requirements. There is now a hard target that North American manufacturers have to meet. That hasn’t happened since the 1980s. Most manufacturers are projecting the price of oil to remain above $60 a barrel for a sustained period of time going forward.
What difficulties will you face in starting the subsidiary?
We need to establish a solid relationship with a fairly new and changing supply base. Recent difficulties in the auto industry have put most of the Tier 1 suppliers through Chapter 7 or 11 bankruptcies. There are some financially strong suppliers that do composite materials, but it’s always been a fragmented industry with a large number of suppliers and contracts for a fairly small volume of components. The OEMs and Tier 1s started to re-evaluate their relationship and the applications appropriate for the structural composite materials. We need to re-evaluate what that supply chain looks like and what support they’ll need.
What do manufacturers need to get involved in that re-evaluation?
The manufacturers with the largest ability to respond to new demand are those with the greatest investment in capability and design testing and manufacturing process equipment. So it requires a substantial investment. There’s not a lot of existing capacity out there that is drop-in and ready for a significant shift toward lightweight composites.
What does Zoltek see as the future of carbon fiber in medium to large production automotive parts?
We are most interested in structural components that lend themselves to high-volume manufacturing, compression molding and injection molding. We stay away from components that are painted because of the difficulties in reconciling the painting process with different manufacturing processes. We’re utilizing our material in this fashion, but we think it will remain a niche market from a volume sales standpoint, and by far the largest tonnage of carbon fiber is with the structural and underhood components such as drive shafts, chassis, pillar, brass beams, bumper beams, intake manifold and oil pans.
What production processes will the subsidiary incorporate?
We’re working with our customer base on all volume-capable carbon fiber manufacturing processes. These include preforming, resin transfer molding, compression molding for thermosets and thermoplastics, thermoplastic compounding for short and long fiber reinforced molding compounds, filament winding. If a process doesn’t have an established history, the development cycle for implementation into a high-volume vehicle platform is quite long. We’re focusing most of our efforts around established processes incorporating fiberglass, analogs or filament winding.
How can the industry improve its recycling of carbon fiber to improve its “green” aspect?
There are different ways for evaluating this aspect of end use requirements. It varies from one OEM to another. In Europe, you must identify exactly how this material will be recovered at its end of life. It’s a different question for thermosets and thermoplastics, and we’re working with companies who are developing techniques to reclaim carbon fiber at its end of life and recycle it either as short fiber or milled fiber materials. Over the course of the life of the material, the weight savings more than offsets its cost to produce and cost for end of life recycling.