实现车体轻量化的杀手锏-碳纤维强化树脂
By www.carbonfiber.com.cn
碳纤维作为汽车车体轻量化的王牌而备受期待。业界齐心协力,力争缩短加工时间。
“21世纪是材料科技的时代”,三菱化学控股集团社长小林喜光说道。
为此,小林社长举出了碳纤维这个例子。如下文所述,由于要和树脂一起使用,因此被称为碳纤维强化树脂(CFRP),主要用于高尔夫俱乐部的球杆等体育用品、飞机和建筑材料等领域。如果该材料能够替代铁和铝,应用到全球最大产业-汽车产业的主要部件中,那么将会改写全球材料史。
丰田2010年12月上市了高性能跑车“雷克萨斯LFA”。该车以每辆3750万日元的日本国产车最高价引起极大关注,同时,在国产车上首次正式采用CFRP,这也成为人们关注的焦点。CFRP占车体结构的65%,与原来的铝结构车体相比,大约轻100kg。内装部件等方面,由日本帝人的子公司东邦特耐克丝供应CFRF材料,发动机罩和车顶方面,从CFRP材料的制造到部材的压制成型,都由东丽负责。
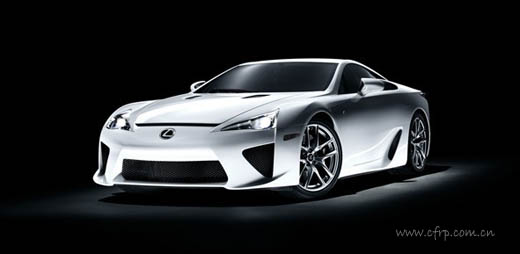
丰田从很早以前就开始自主开发CFRP加工技术。车辆材料技术部有机材料室长间濑清芝表示,“当初为了采用最先进的轻量材料、突出驾驶性能,决定采用CFRP”。


每辆车减排5吨二氧化碳
2011年1月,日本富士重工业推出的运动车型“斯巴鲁 翼豹 WRX STI tS”采用了与东丽共同开发的CFRP车顶。重量大约为钢板的2成左右。如果车顶变轻,车体重心就会变低,操舵性也会得到提高。
三菱化学控股集团旗下的三菱人造纤维公司是与德国CFRP厂商西格里公司(SGL)共同设立的合资公司。将面向德国宝马公司计划2015年上市、目前正处于开发阶段的EV的核心部件,供应作为碳纤维原料的丙烯纤维。另外,2010年4月,东丽与德国戴姆勒公司就CFRP汽车部件的共同开发达成协议。计划3年后将这些部件配备于梅赛德斯·奔驰乘用车上。
碳纤维的特点是质量轻、强度大、硬度高且不生锈等。重量为铁的4分之1左右。拉伸时的强度是尼龙(聚酰胺)的10~20倍、铁的10倍,弹性指数达到尼龙的20~60倍、铁的7倍。
碳纤维在一般情况下,作为CFRP与环氧树脂等组合使用。据称最常见的比例是,体积的60%左右为纤维,剩余40%是树脂。
据碳纤维协会介绍,“如果在普通乘用车上应用目前已实现的技术,那么车体重量的17%可替换为CFRP,重量可减轻约30%”。从汽车制造、组装、行驶直至废弃的生命周期来看,与原来的汽车相比,每辆车在10年之内可减排5吨二氧化碳。
日本企业占据全球市场7成份额
碳纤维历史悠久。1879年,托马斯·爱迪生燃烧棉线和竹丝,制造出了灯泡的灯丝。在日本,碳纤维的基础原理和技术被开发出来,1971年,东丽正式开始商业生产,这在全球尚属首次。由丙烯长纤维、以及石油和煤炭等的副产物-沥青在高温条件下炭化而成。汽车车体等使用由丙烯长纤维制成的碳纤维。
目前,东丽、东邦特耐克丝和三菱人造纤维等日本企业占据全球市场7成份额。起初在钓竿等体育用品领域开拓市场,从20世纪90年左右起,还开始应用于一旦破损就会导致坠机的主翼等飞机框架结构材料上。20世纪90年代,开始全面应用于土木建筑和产业机械等产业用途,市场得到进一步扩大。作为美国知名航空公司波音公司的新一代中型机,“787”重量的5成左右是CFRP。
虽然2009年因雷曼危机供货减少,年供货仅2万5000吨,但东丽的大西盛行常务表示,“目前需求已超出预期”,预计2010年度的全球CFRP需求将超过3万吨,2013年的全球需求大约为5万吨。预计到2013年度,建筑材料、发电用风车等产业用途方面将比上一年增长21%。另外,2010~2015年,汽车用途方面市场需求的全面扩大同样备受期待。
这是因为,随着全球汽车燃效规定越来越严格,需要进一步实现车体轻量化。现在,F1等赛车、以及“法拉利”等高级车的车体很大一部分都使用了CFRP。
从三菱“帕杰罗”开始,日本国内也有多款汽车采用了CFRP传动轴(传递发动机动力的部件)。
不过从目前来看,成本较高的缺点妨碍其应用于量产车核心部件。虽然过去曾用于日产“Skyline GT-R”的发动机罩等,但该车种的现行车型并未继续采用CFRP。“目前,在汽车上使用CFRP的目的还主要在于宣传造势。用于量产车的主要部件将成为技术开发上的突破性进展”,东丽的大西常务介绍道。
克服高成本
之所以能被“雷克萨斯LFA”采用,其前提是按单生产。要应用于量产车,提高加工速度是不可或缺的。要想用CFRP取代铁和铝,需要把加工时间缩短到与铁的冲压时间相等的1~1.5分左右。
目前,市场上流通的9成以上的CFRP,其树脂原料是环氧树脂等“热硬化性树脂”。这种树脂的性质是,在常温下呈液态,粘度较低,很容易与纤维相结合,加热后会变为固体。此前制造汽车部件采用的加工法是,把碳纤维织物放到模具中,注入树脂使之硬化成型,然后从模具中取出。
但这种加工法有着加工时间过长的缺点。以前由于需要高温固化成型等,因此CFRP的成形总共需要160分钟。目前,在日本新能源产业技术综合开发机构(NEDO)委托东丽和日产汽车等进行的研究中,开发出了超高速硬化树脂等,可将成形过程缩短到5分钟。
此外还存在一个问题,热硬化性树脂在加热固化后会发生化学反应,即使再次冷却也不会还原为原来的液体。必须准确地一次性固化成型,与金属相比,加工难度较高。
因此,使用“热可塑性树脂”的CFRP的研究开发也正在进行之中。热可塑性树脂中最具代表性的就是聚乙烯和聚丙烯。在常温下呈固体状,但加热后可熔化流动。即使已经固化成型,也可多次重复进行软化熔融,因此较易加工。不过由于粘度较高,因此很难与纤维相结合。
东丽、三菱人造纤维和东京大学等的研究小组,受日本新能源产业技术综合开发机构的委托,确立了在维持与热硬化性树脂同等性能的同时、将加工时间控制在2分钟之内的目标。据称,东邦特耐克丝已经独立研发出可将使用热可塑性树脂的加工时间控制在1分钟之内的方法。
每公斤碳纤维的价格是2000~3000日元,比铁要高出一位数。要实现量产化,还需要降低纤维的制造成本。2009年度,日本国内钢铁厂商接到的国内汽车用普通钢材订单是876万吨。大西常务认为,如果CFRP应用于量产车的趋势全面展开,那么“碳纤维原材料目前3万吨的年产能可能会无法满足市场需求,到时候还需要对这个问题进行深入探讨”。
丰田有机材料室长间濑表示,“虽然在成本、生产效率和接合性等方面,CFRP仍存在许多亟待解决的课题,但作为新一代轻量材料,CFRP仍然具有很大魅力,今后我们将全力进行研发”。目前,日本国内外的材料和汽车厂商正纷纷加速进行研发,一旦出现突破性进展,CFRP甚至可能会提前得到普及。
来源:《日经生态》
记者:金子宪治、外薗祐理子
碳纤维作为汽车车体轻量化的王牌而备受期待。业界齐心协力,力争缩短加工时间。
“21世纪是材料科技的时代”,三菱化学控股集团社长小林喜光说道。
为此,小林社长举出了碳纤维这个例子。如下文所述,由于要和树脂一起使用,因此被称为碳纤维强化树脂(CFRP),主要用于高尔夫俱乐部的球杆等体育用品、飞机和建筑材料等领域。如果该材料能够替代铁和铝,应用到全球最大产业-汽车产业的主要部件中,那么将会改写全球材料史。
丰田2010年12月上市了高性能跑车“雷克萨斯LFA”。该车以每辆3750万日元的日本国产车最高价引起极大关注,同时,在国产车上首次正式采用CFRP,这也成为人们关注的焦点。CFRP占车体结构的65%,与原来的铝结构车体相比,大约轻100kg。内装部件等方面,由日本帝人的子公司东邦特耐克丝供应CFRF材料,发动机罩和车顶方面,从CFRP材料的制造到部材的压制成型,都由东丽负责。
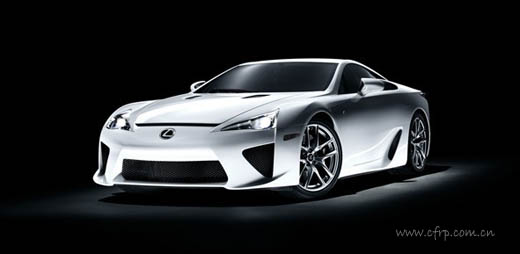
丰田从很早以前就开始自主开发CFRP加工技术。车辆材料技术部有机材料室长间濑清芝表示,“当初为了采用最先进的轻量材料、突出驾驶性能,决定采用CFRP”。


每辆车减排5吨二氧化碳
2011年1月,日本富士重工业推出的运动车型“斯巴鲁 翼豹 WRX STI tS”采用了与东丽共同开发的CFRP车顶。重量大约为钢板的2成左右。如果车顶变轻,车体重心就会变低,操舵性也会得到提高。
三菱化学控股集团旗下的三菱人造纤维公司是与德国CFRP厂商西格里公司(SGL)共同设立的合资公司。将面向德国宝马公司计划2015年上市、目前正处于开发阶段的EV的核心部件,供应作为碳纤维原料的丙烯纤维。另外,2010年4月,东丽与德国戴姆勒公司就CFRP汽车部件的共同开发达成协议。计划3年后将这些部件配备于梅赛德斯·奔驰乘用车上。
碳纤维的特点是质量轻、强度大、硬度高且不生锈等。重量为铁的4分之1左右。拉伸时的强度是尼龙(聚酰胺)的10~20倍、铁的10倍,弹性指数达到尼龙的20~60倍、铁的7倍。
碳纤维在一般情况下,作为CFRP与环氧树脂等组合使用。据称最常见的比例是,体积的60%左右为纤维,剩余40%是树脂。
据碳纤维协会介绍,“如果在普通乘用车上应用目前已实现的技术,那么车体重量的17%可替换为CFRP,重量可减轻约30%”。从汽车制造、组装、行驶直至废弃的生命周期来看,与原来的汽车相比,每辆车在10年之内可减排5吨二氧化碳。
日本企业占据全球市场7成份额
碳纤维历史悠久。1879年,托马斯·爱迪生燃烧棉线和竹丝,制造出了灯泡的灯丝。在日本,碳纤维的基础原理和技术被开发出来,1971年,东丽正式开始商业生产,这在全球尚属首次。由丙烯长纤维、以及石油和煤炭等的副产物-沥青在高温条件下炭化而成。汽车车体等使用由丙烯长纤维制成的碳纤维。
目前,东丽、东邦特耐克丝和三菱人造纤维等日本企业占据全球市场7成份额。起初在钓竿等体育用品领域开拓市场,从20世纪90年左右起,还开始应用于一旦破损就会导致坠机的主翼等飞机框架结构材料上。20世纪90年代,开始全面应用于土木建筑和产业机械等产业用途,市场得到进一步扩大。作为美国知名航空公司波音公司的新一代中型机,“787”重量的5成左右是CFRP。
虽然2009年因雷曼危机供货减少,年供货仅2万5000吨,但东丽的大西盛行常务表示,“目前需求已超出预期”,预计2010年度的全球CFRP需求将超过3万吨,2013年的全球需求大约为5万吨。预计到2013年度,建筑材料、发电用风车等产业用途方面将比上一年增长21%。另外,2010~2015年,汽车用途方面市场需求的全面扩大同样备受期待。
这是因为,随着全球汽车燃效规定越来越严格,需要进一步实现车体轻量化。现在,F1等赛车、以及“法拉利”等高级车的车体很大一部分都使用了CFRP。
从三菱“帕杰罗”开始,日本国内也有多款汽车采用了CFRP传动轴(传递发动机动力的部件)。
不过从目前来看,成本较高的缺点妨碍其应用于量产车核心部件。虽然过去曾用于日产“Skyline GT-R”的发动机罩等,但该车种的现行车型并未继续采用CFRP。“目前,在汽车上使用CFRP的目的还主要在于宣传造势。用于量产车的主要部件将成为技术开发上的突破性进展”,东丽的大西常务介绍道。
克服高成本
之所以能被“雷克萨斯LFA”采用,其前提是按单生产。要应用于量产车,提高加工速度是不可或缺的。要想用CFRP取代铁和铝,需要把加工时间缩短到与铁的冲压时间相等的1~1.5分左右。
目前,市场上流通的9成以上的CFRP,其树脂原料是环氧树脂等“热硬化性树脂”。这种树脂的性质是,在常温下呈液态,粘度较低,很容易与纤维相结合,加热后会变为固体。此前制造汽车部件采用的加工法是,把碳纤维织物放到模具中,注入树脂使之硬化成型,然后从模具中取出。
但这种加工法有着加工时间过长的缺点。以前由于需要高温固化成型等,因此CFRP的成形总共需要160分钟。目前,在日本新能源产业技术综合开发机构(NEDO)委托东丽和日产汽车等进行的研究中,开发出了超高速硬化树脂等,可将成形过程缩短到5分钟。
此外还存在一个问题,热硬化性树脂在加热固化后会发生化学反应,即使再次冷却也不会还原为原来的液体。必须准确地一次性固化成型,与金属相比,加工难度较高。
因此,使用“热可塑性树脂”的CFRP的研究开发也正在进行之中。热可塑性树脂中最具代表性的就是聚乙烯和聚丙烯。在常温下呈固体状,但加热后可熔化流动。即使已经固化成型,也可多次重复进行软化熔融,因此较易加工。不过由于粘度较高,因此很难与纤维相结合。
东丽、三菱人造纤维和东京大学等的研究小组,受日本新能源产业技术综合开发机构的委托,确立了在维持与热硬化性树脂同等性能的同时、将加工时间控制在2分钟之内的目标。据称,东邦特耐克丝已经独立研发出可将使用热可塑性树脂的加工时间控制在1分钟之内的方法。
每公斤碳纤维的价格是2000~3000日元,比铁要高出一位数。要实现量产化,还需要降低纤维的制造成本。2009年度,日本国内钢铁厂商接到的国内汽车用普通钢材订单是876万吨。大西常务认为,如果CFRP应用于量产车的趋势全面展开,那么“碳纤维原材料目前3万吨的年产能可能会无法满足市场需求,到时候还需要对这个问题进行深入探讨”。
丰田有机材料室长间濑表示,“虽然在成本、生产效率和接合性等方面,CFRP仍存在许多亟待解决的课题,但作为新一代轻量材料,CFRP仍然具有很大魅力,今后我们将全力进行研发”。目前,日本国内外的材料和汽车厂商正纷纷加速进行研发,一旦出现突破性进展,CFRP甚至可能会提前得到普及。
来源:《日经生态》
记者:金子宪治、外薗祐理子